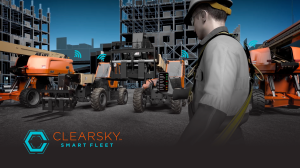
JLG expands Its ClearSky Smart Fleet™ IoT Platform
Evolving traditional telematics to comprehensive IoT capabilities JLG Industries, Inc. a global manufacturer of mobile elevating work platforms (MEWPs) and telehandlers,
Evolving traditional telematics to comprehensive IoT capabilities JLG Industries, Inc. a global manufacturer of mobile elevating work platforms (MEWPs) and telehandlers,
Stahlin® Enclosures, manufacturers of high-performing non-metallic electrical and industrial enclosures announce the availability of its new side panels and weight distribution shelves which
Siemens is presenting its latest solutions for smart and networked drive technology. By networking entire drive systems, machine and plant
BeerBoard, a provider in technology and automated intelligence for the on-premise hospitality industry, announced that Florida Distributing Company (FDC), which
Aptean, a global provider of mission-critical enterprise software solutions, announced the launch of Aptean EAM, an all-new, cloud-based enterprise asset
Unlike vendors with multiple WMS products, Softeon Warehouse Management System serves large, mid-level, and smaller operations across a fulfillment network
On this episode, I was joined by the US Regional Sales Director at JLT Mobile Computers, Glenn Lundgren. JLT Mobile
In this episode, I reconnected with Jim Lawton of Zebra Technologies. Jim is the Vice President and General Manager of
Rugged, reliable forklift computers with superior network connectivity help Solar run complex warehouse operations, minimize errors, and increase on-time customer delivery
Renowned Retail, CPG, and Supply Chain Veteran brings a world-class track record to a global provider of Internet of Things
While vulnerability disclosures increased 21% in the second half of 2021 and increasingly sophisticated criminal attacks made regular news, organizations
STXI Motion, a global motion control, and servo solution company, introduces the stepIM NEMA 17 EtherCAT model, the newest addition to its family
Variable Frequency Drives with Modbus TCP/IP supports machine builders in-process applications KEB America, Inc., a provider of industrial automation solutions
Connected Industrial Mobility provider, SIERA.AI, announced the completion of a $6.8 million-dollar seed funding round. The funding round was supported
Hikvision, a manufacturer and supplier of security products and solutions, continues to build on its popular line of AcuSense surveillance
At the dawn of the year 2022, HGH Group is celebrating a unique milestone, marking its 40th anniversary with a renewed
On this episode, I was joined by Co-Founder and President at Inspectorio, David Klein. Is it a supply chain SaaS
Seeq’s annual partner awards program honors excellence in delivering the next generation of process manufacturing improvements Seeq Corporation, a manufacturing
As part of JLT’s growth strategy to strengthen its sales channel, the acquisition reinforces the company’s French presence and commitment
On this episode, I was joined by Dan Gilmore who is the CMO at Softeon. Dan was previously on the