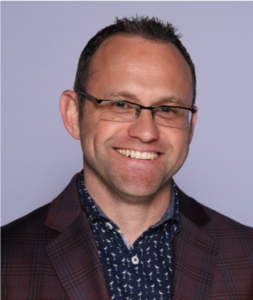
Enhancing AI Chatbot Interactions with Context-Rich Personas
Imagine having access to the expertise of a lawyer, accountant, or warehouse manager, wherever and whenever you like, for pennies.
Imagine having access to the expertise of a lawyer, accountant, or warehouse manager, wherever and whenever you like, for pennies.
NORD provides their Authorized Distributors, sales partners, and internal team members with valuable, comprehensive training to ensure they can better
Orders of manufacturing technology, measured by the U.S. Manufacturing Technology Orders (USMTO) report published by AMT – The Association For
AutoScheduler.AI, an innovative Warehouse Orchestration Platform and WMS accelerator, announces that. He will replace Stephen Zujkowski, who is retiring. Ian
IFS has boosted its offering in the six hardcore industries it serves to 60+ in-depth Industrial AI scenarios, which are
You’ve heard the buzz around Generative AI-powered chatbots like ChatGPT, Claude, and Gemini. But are they worth the hype? Absolutely.
In this episode of The New Warehouse Podcast, Ajoy Krishnamoorthy, CEO of Cin7, discusses how their platform transforms operations by
In this episode of The New Warehouse Podcast, Josh Roffman, EVP of Marketing at Loftware, explores the pivotal role labeling
In this episode of The New Warehouse Podcast, Danny Glass, co-founder of Cellaware Technologies, explores the innovative ways artificial intelligence
Award Recognizes Women providing positive impacts for their organizations & within the Orange County, California, Community Orange County Business Journal
Nucor is pleased to announce the promotion of two esteemed teammates – Daniel Aguirre who is now Commercial Director and
Another year-end is approaching. But I’m not sure what to expect for next year. Before we do anything further, I
I’m thrilled to join Material Handling Wholesaler as their newest columnist. I jumped at the opportunity when Garry Bartecki suggested
15 Plus Years of Experience in Enterprise Sales and Supply Chain Leadership AutoScheduler.AI has announced that it has added Jordan
The company brings a deep legacy of driving industry standards to the Margo initiative, enabling more flexible, scalable automation for
With 30 years of experience in the supply chain industry, he specializes in designing and implementing innovative and cost-justified distribution
However, there is optimism that Industrial AI will improve quality control and bring new sustainability gains Research from IFS, a technology
Generative AI Expo and TMCnet are accepting applications for the 2024 Generative AI Product of the Year Awards. Suppose your organization
Peak Technologies ranked 65th on The Channel Company’s CRN Solution Provider 500 list, the annual ranking of the largest solution
The distribution process is burdened with consumer expectations demanding faster deliveries, warehouse labor shortages, scarcity of physical storage space, and