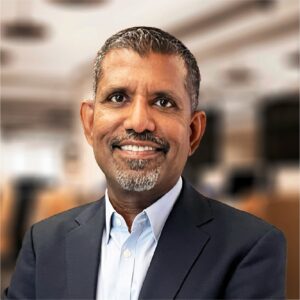
Future proof your supply chain: Embracing automation and AI
Supply chain leaders are turning to automation and AI to enhance operational efficiency, reduce costs, and elevate the customer experience
Supply chain leaders are turning to automation and AI to enhance operational efficiency, reduce costs, and elevate the customer experience
According to a PwC Pulse Survey ….40% of Executives plan to implement significant reorganization, including layoffs. That is up from
Manufacturing technology orders, measured by the U.S. Manufacturing Technology Orders Report published by AMT – The Association For Manufacturing Technology,
Warehouse software market to grow at a CAGR of 12.7% out to 2030 The standalone warehouse management system (WMS) market
Remote engine disable/enable advances the Machine IQ system through two-way functionality A provider in innovation and digital solutions, Bobcat Company
Easy-to-use tools help companies with less complex and smaller operations NetLogistik, a provider of transformative services for supply chain digitalization,
Supply chain leaders are turning to automation and AI to enhance operational efficiency, reduce costs, and elevate the customer experience Automation
Technology Rules. Every business or industry publication you pick up states….IF YOU DO NOT START TAKING ACTION NOW YOU WILL
E Tech Group announces the immediate renaming of Automation Group to E Tech Group, following the strategic acquisition of Automation
IFS has announced the general availability of its latest IFS Cloud release. As the only vendor focused on helping asset- and
The Seeq platform will be leveraged to maximize production and enhance efficiency across Equinor’s global assets. Seeq and Equinor have announced
Peak Technologies has announced a significant milestone, becoming a certified Zebra Technologies partner in Australia, delivering fixed industrial scanning solutions
Bill brings 30 years’ experience working with clients to evaluate, design, and implement innovative solutions to solve complex supply chain
Credits continuous innovation of technologies centered around workers Warehouse workers made 100 billion warehouse picks using Lucas Systems software, according
The new Seeq Vantage app scales subject matter expert-driven insights for accelerated value across the enterprise Seeq has announced the
Softeon’s recognition as a Visionary in the Gartner Magic Quadrant for Warehouse Management Systems for the 13th consecutive time is based
Working at the same company for 25 years is a rare occurrence these days. Global Shop Solutions has announced the
Matrix Design Group, LLC hosted a groundbreaking ceremony for its new headquarters in Newburgh, Indiana on April 18. It was attended
Advanced, real-time, cyber-attack response limits the impact within milliseconds at machine speed, isolates and quarantines the infected production equipment to
The committee selected the Top 100 Logistics IT Providers based on those offering the innovations their customers need to streamline