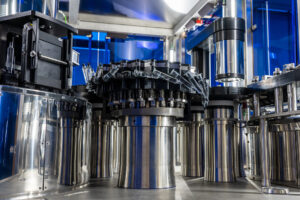
Antares Vision Group to showcase automatic inspection machines for vials and more at INTERPHEX
Company also will emphasize its recently launched DIAMIND ecosystem, a portfolio of interconnected software and hardware systems for comprehensive traceability.