SensThys and Smartrac partner to provide RFID-based moisture, temperature and location sensing solution
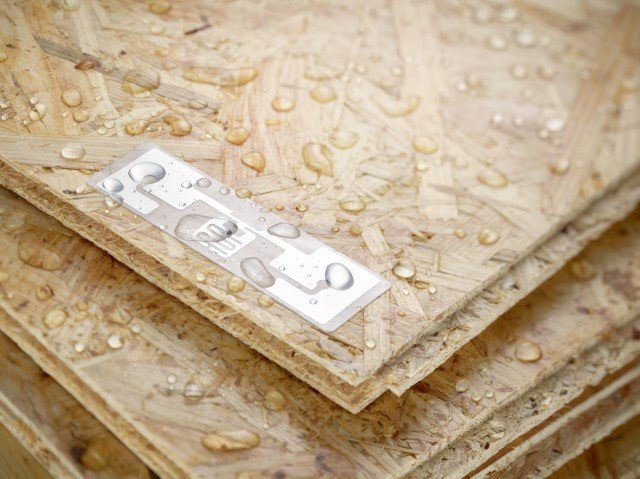
Smartrac Technology Group, a global provider in RFID technology and IoT solutions, and SensThys Inc., a technology company that seamlessly integrates sensors and communications with a high-efficiency networking platform, have partnered to provide an innovative RFID-based moisture, temperature and location sensing solution for facilities management. The new solution combines SensThys’ full line of RAIN RFID (UHF) readers and algorithms with Smartrac’s custom-built moisture and temperature sensing RAIN RFID inlays and tags, based on its successful SENSOR product line of passive products. By detecting moisture and measuring temperatures in a wide variety of building materials, including concrete, gypsum board, insulation and other construction materials, it enables a broad portfolio of innovative applications for facility and construction monitoring and management. Passive sensing inlays and tags from Smartrac To provide the best possible accuracy and reliability when embedded in construction materials with diverse physical characteristics, Smartrac’s high-quality, battery-less SENSOR inlays are optimized for interaction with readers and software infrastructure provided by SensThys. The thin and customized inlays are equipped with Axzon’s Magnus® S3 ICs that can accurately detect and measure temperature and moisture levels in the surrounding environment. Like Smartrac’s other SENSOR RAIN RFID products, this solution-specific product offers cost efficiency and ease of implementation. The sensing inlays are interrogated using SensThys’ solution to monitor and track the physical state of the product at construction sites, distribution yards and manufacturing facilities. Key applications include tracking infrastructure components such as roofing materials, monitoring changes in products including thermal and moisture cycling, and tracking concrete pre-casts that are either in inventory, in transit, at holding facilities, or physically embedded within their final infrastructure. Reader and algorithms from SensThys The SensThys SensX Extreme RFID reader is ideal for the construction industry due to its physical robustness, which includes IP67 rating, key military standards testing, and a wide operating range including cold starts and thermal shock. The 33dBm reader has a sweeping array of sensors, including an accelerometer, gyroscope, barometric pressure, GPS and BLE beacon detection, that together enable situational awareness including its physical position, orientation and movement. Communication is handled natively by internal Ethernet, Wi-Fi or Bluetooth, with an external cellular connection available. SensThys created the algorithms to rapidly compute the location, temperature and moisture of a tag embedded within an object. These algorithms are now available for use on all M-Power readers including the SensArray and the SensX Extreme, and the algorithm can be made available for incorporation into other fixed and hand-held readers. Solutions for real-world problems “This design effort, coupled with extensive in-situ testing, resulted in an upgraded M-Power reader capability to offer customers a practical method to quickly and reliably interrogate Smartrac’s sensor tags. Our IP67 SensX Extreme reader, which uses the M-Power core, allows us to identify the tagged item and provide the location, time, temperature and moisture information of the asset,” said Jo Major, CEO of SensThys. “For example, the seamless integration of sensors enables customers to understand where and when a roof has started to leak or when a concrete foundation is fully cured.” “By embedding our high-quality SENSOR inlays into building materials when they are manufactured, customers can now really make their building material product line smart,” said Bill Barr, VP Product Management at Smartrac. He continued, “The great work we’ve accomplished together with the SensThys team provides a sensor-to-cloud infrastructure for non-destructive testing, so our customers can conveniently deploy temperature and moisture sensors in a variety of tough environments.”
Access Control Group releases new feature for Product Vital
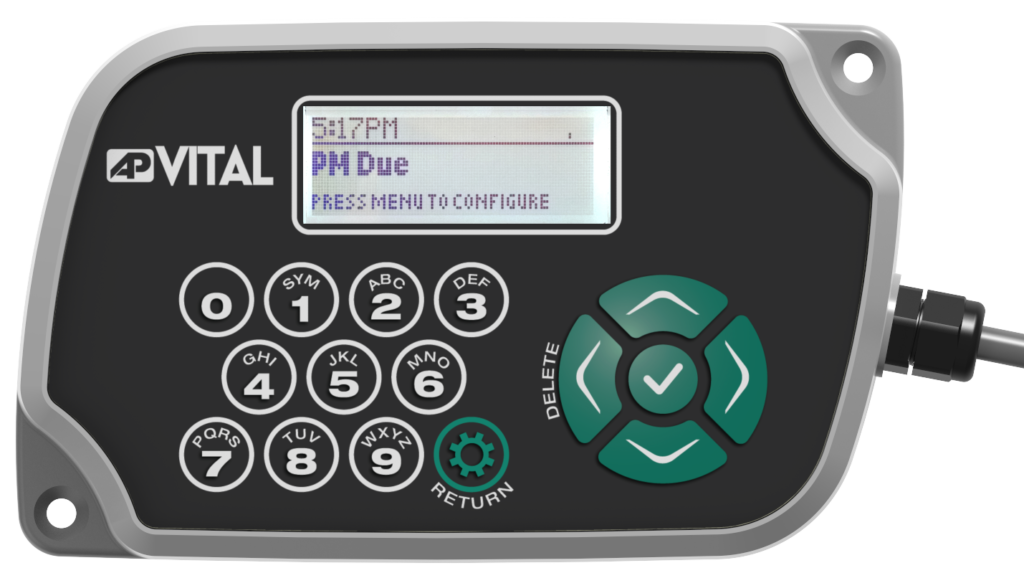
Cutting edge telematics provider adds automated PM scheduling capabilities to its hour meter collector product, Vital. Making simple asset management also cover maintenance efforts Access Control Group (Access) announced a revolutionary update to its wireless asset tracker device, Vital. The latest updates now make it possible for Vital to create multiple automated preventive maintenance (PM) scheduling, send maintenance requests right from the trucks, and receive alerts of approaching due dates via email or SMS. These updates make it possible for fleet managers to utilize Vital to not only capture hour meters and track assets but also manage the entire maintenance process. This new feature will eliminate unexpected downtimes from issues with the assets and any pencil whipping to send a request to maintenance. “Maintenance is just as crucial to an operation as the equipment they fix,” said Access CEO Arun Patel. “We developed Vital with the goal to help rental fleets capture hour meters and track their assets via GPS. However, there was money on the table for dealers and fleet managers to also manage their maintenance processes. With that in mind, we looked for a way to facilitate not only the communication between managers, operators, and maintenance but also serve as a device to set up schedules to take care of the equipment before it breaks.” Multiple automated PM scheduling can now be set up with Vital per recommendation of equipment manufacturers to ensure managers receive reminders before maintenance is due. Dealers can now keep track of those reminders via our cloud platform, AssetPro 360, and send those alerts to service managers that rented their vehicles. Once maintenance is performed, it can be synced with your business system. Managers can now request service right from the equipment, eliminating precious time for filling out reports. The request is sent to the dispatcher or desired personnel, that can choose to either receive the alert via email or SMS. By setting up those reminders, operations will be able to lower avoidable downtime, keep all equipment in good condition and save on budgeted break down. Vital’s new feature makes investing in telematics not only affordable but also attainable.
SAM, LLC first in North America to deploy advanced Aerial Scanning Technology
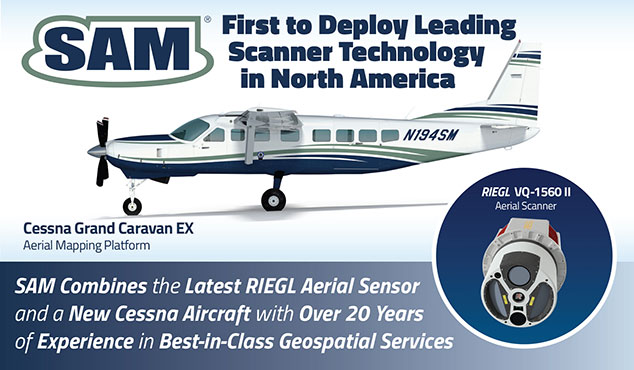
SAM, LLC, (Surveying And Mapping, LLC) a provider in providing geospatial data solutions, will be the first company in North America to acquire and deploy the most recent major advance in aerial scanning technology, the RIEGL VQ-1560 II. The sensor will be installed in SAM’s new fixed-wing aircraft, a 2019 Cessna Grand Caravan EX, to further expand SAM’s national aerial mapping capabilities. “SAM has always been an industry leader when it comes to adopting new technology,” said SAM President and CEO, Chris Solomon. “By combining this RIEGL scanner and new Cessna with our deep experience in aerial mapping, we continue to expand our capabilities and increase the value we deliver for clients.” The RIEGL VQ-1560 II is equipped with a 4 megahertz, dual-channel airborne mapping system that can collect High Density (HD) LiDAR at up to a 2,450 meter swath or a density of 60 points per square meter from a fixed-wing platform. The sensor features two integrated 150-megapixel digital cameras that collect vertical photography simultaneously with HD LiDAR. One camera acquires RGB imagery to generate orthophotos at 2-inch ground sample resolution, while the second camera acquires imagery in the Near Infrared (NIR) band for multispectral analysis. This combination of enhanced capabilities will be beneficial for many different client types, including electric transmission clients needing richer, more detailed data for infrastructure and right-of-way analysis, or forestry and vegetation management clients needing to identify hazards and unhealthy trees. The Cessna Grand Caravan EX housing the scanner is extremely well-suited for aerial mapping. Its ample payload allows it to transport a significant amount of equipment, and it can land on shorter runways than many aircraft, giving it access to more airports. Also, its ability to fly safely at 90 knots allows for the acquisition of denser point clouds and collecting greater detail of our clients’ assets. The dual port aircraft allows for the installation of the HD LiDAR and vertical facing cameras plus two oblique sensors. These enable the simultaneous collection of oblique photos in a single flight. This innovative approach and leading technology efficiently acquires four datasets, providing advanced survey capability and quality for SAM clients. SAM Vice President, Geospatial, Bob Williams emphasized how the new system will benefit SAM clients “The combination of this aircraft and aerial sensor will allow SAM to strategically place multiple systems throughout the country to reduce mobilization and response time,” Williams said. “This system allows SAM to efficiently acquire high-quality datasets that exceed industry standard specifications for remote sensing data acquisition on electric transmission and distribution, renewable energy, transportation, and oil and gas mapping projects. With direct control of its own aircraft, SAM has greater ability for rapid deployment to critical sites.” SAM’s plans to deploy the Cessna Grand Caravan EX with the new RIEGL VQ-1560 II aerial scanner beginning in the first quarter of 2020.
Precise control of double-depth positioning processes
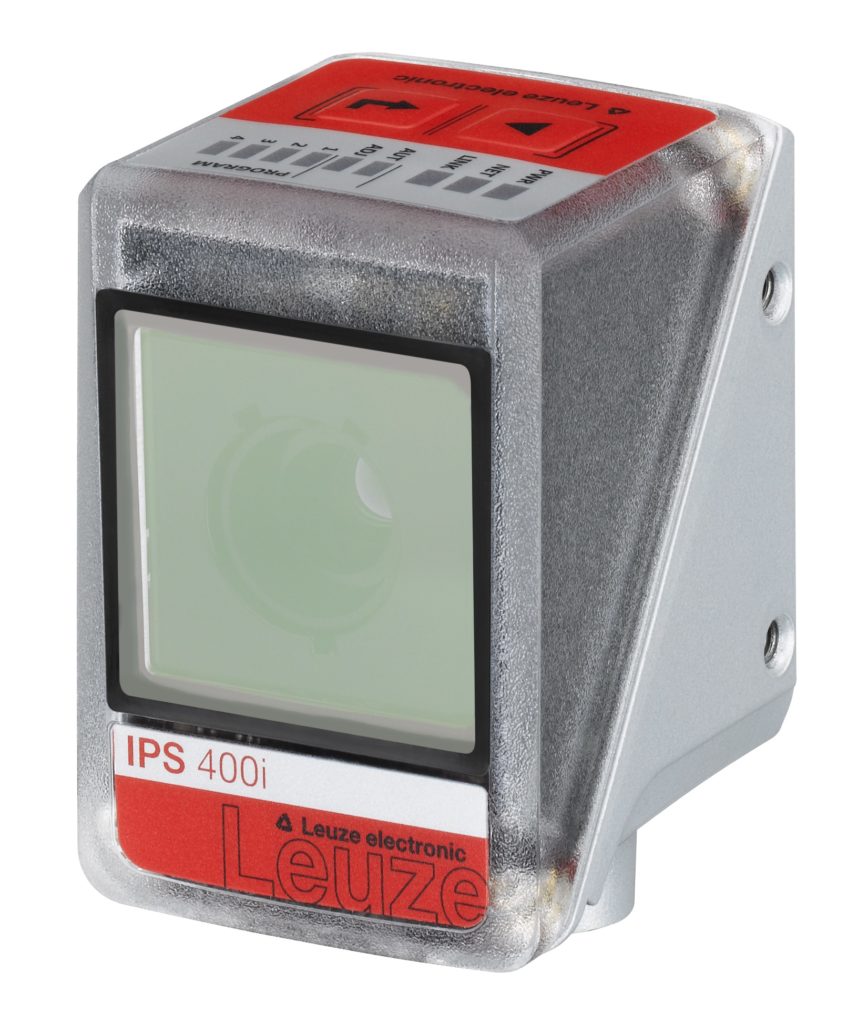
The new IPS 400i from Leuze electronic is the smallest camera-based positioning sensor on the market for double-depth compartment fine positioning. It helps high-bay storage devices to quickly and easily find the right rack. With the new camera-based IPS 400i positioning sensor for high-bay storage devices, Leuze electronic – the expert for sensor solutions for intralogistics – is expanding its IPS range of products with a new model for optical compartment fine positioning. About a year ago, Leuze electronic introduced the IPS 200i, the smallest camera-based positioning sensor for single-depth, which is used for single depth pallet high racks and small-part container storage. The new IPS400i is just as compact as its sibling, the IPS 200i, and thus requires little space on the high-bay storage device – however, it detects round holes or reflectors not only in single-depth, but also double-depth bars and thus determines the position deviation relative to the target position in the X and Y directions. This makes the new camera-based IPS 400i positioning sensor particularly suited for use in double-depth pallet high-bay warehouses. A model with integrated heating for use in refrigerated warehouses down to -30 °C is also available. Both variants – IPS 200i and IPS 400i – offer the user simple and fast commissioning and operation. The sensors are put into operation using a web-based configuration tool with a user-controlled installation assistant (wizard). Printed configuration codes are read in without a PC via “Code Generator,” which means that configuration adjustments can be made directly on the high-bay storage device. An alignment system consisting of four feedback LEDs further facilitates the commissioning process. Due to its powerful, ambient-light-independent IR LED lighting, fault-free use in warehouse technology is possible with just one single device for a working range of up to 2400 mm. With the integrated TCP/IP interface and PROFINET RT, the IPS 400i can be directly integrated into the network environment and enables quick, location-independent diagnostics. Condition monitoring and predictive maintenance take place using a quality score that detects deterioration in the reading performance of the sensor at an early stage. This minimizes downtime and increases the availability and cost-effectiveness of the systems.
EarthCam introduces AI-Powered Visual Data for procore daily log automation
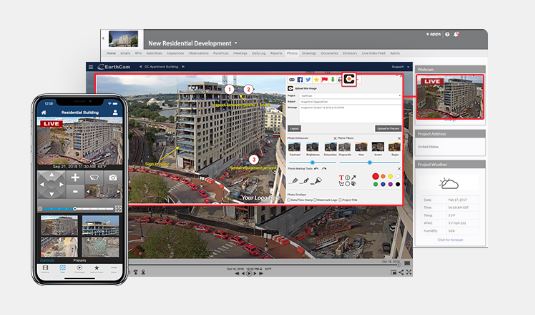
Image Recognition, Weather Analysis and Green Initiatives Improve Workflows Today at Procore Groundbreak, EarthCam, the leading provider of construction camera technology, announced the biggest update to its Procore feature set to date. With a major focus on its new initiative of Daily Log Automation, EarthCam is creating a more efficient and convenient project management process with automatic data integration for weather, waste and equipment tracking. Maintaining a Daily Log of an active jobsite is both critical and requires significant effort. Understanding that importance, EarthCam is leveraging its high-quality cameras already on the jobsite to deliver new levels of informative data that affect the overall project management process. In a major advancement to its growing portfolio of AI-powered image analytics, EarthCam will now deliver AI Image Recognition of jobsite equipment and vehicle tracking. With the ability to detect up to 19 different vehicle classifications, Procore users now have a smarter way to provide visual inspections and populate log entries of the various equipment on the jobsite. Every hour, 24/7, a log entry is automatically created with a list of all detected equipment and an annotated photograph so visual verification can be performed to determine when equipment arrives onsite, is in use and when it is removed. EarthCam is also premiering its new Jobsite Weather Station monitoring and analysis solution. The 4G LTE wireless, solar-powered sensor measures eight points of environmental jobsite conditions and combines them with EarthCam’s live webcams and 360° reality capture imagery. The visually-enhanced data is then automatically uploaded into Procore’s Daily Log. With 24/7 recording of environmental conditions for the entire jobsite, both inside and out, teams will benefit by saving time and generating a more accurate record, all within Procore. “EarthCam’s core purpose is to create better lives through visual information, and this major advancement of our Procore integration speaks directly to that purpose”, said Brian Cury, CEO and Founder of EarthCam. “Through a combination of Procore’s insightful Daily Log and our automated visual content, construction teams can spend less time in the field, minimize waste and support a lean culture for successful project management.” EarthCam’s green initiative led to populating content for the Waste and Dumpster sections of the Procore Daily Log, as well. EarthCam’s cameras accurately document the waste that is placed in the jobsite dumpster, including hazardous or recyclable materials that should not be placed in the dumpster, as well as unauthorized waste disposal. High-quality photos are automatically uploaded to the Daily Log throughout the day. With all of these new services, the content can be easily shared for visual verification and exported as a PDF or CSV file to be included in reports. This latest round of powerful features builds upon EarthCam’s long-standing integration with Procore, which includes innovative markup tools for submitting jobsite photos as RFIs, observations or change events. Combined with EarthCam’s pioneering applications for AI-powered image recognition and editing of its time-lapse movies, EarthCam is driving productivity for a more visually informative jobsite. EarthCam provides end-to-end services, including camera rentals, same-day delivery and professional installation.
Evaluating systems with digital modeling
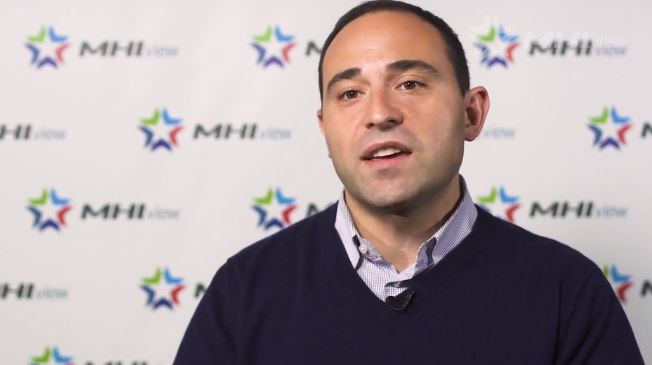
Companies are now turning to robotics and other automated technologies to meet customer demands. Updating facilities with new equipment used to involve purchasing and installing systems to see if they worked in your operation. Now companies are able to see and evaluate their options using digital modeling and virtual commissioning. Click here for the video. Tags: AI automation data digital modeling distribution predictive analytics robotics software update virtual commissioning
Toshiba’s Maegan Lujan appointed 2019 Woman Influencer in Tech
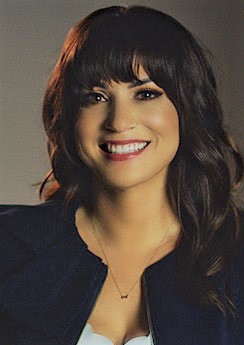
Leading Document Management Publication Selects Lujan for Her Positive Industry Impact Toshiba America Business Solutions is proud to announce that Maegan Lujan has been selected as a 2019 Woman Influencer by The Cannata Report. Lujan, who is currently director of solutions and services marketing at Toshiba, was also previously recognized as a 2016 Young Influencer by The Cannata Report. “Maegan has demonstrated initiative and relentless commitment to both our channel and culture since joining Toshiba. The spirit of innovation that sets Toshiba apart from our competitors runs deep in her DNA,” Toshiba America Business Solutions President and CEO Scott Maccabe said. “Her dedication and proven capabilities have rightfully earned her these recognitions. We are proud to have her as part of our Toshiba family supporting our solutions and services strategy.” Before joining Toshiba in 2013, Lujan accumulated nearly a decade of experience in the technology field linking technology vendors and resellers with the best products and services to advance their lines of business. “I’m honored to be a 2019 Woman Influencer in Tech,” Lujan said. “And, I am thrilled to share my journey and help empower the next generation of women in document solutions technology.” The publication annually highlights women who have made a significant impact in the industry. Lujan was one of three women recognized this year. “Maegan represents the next generation of talent driving the imaging industry today. She stands out as an executive who is completely committed to achieving her customers’ goals. Wise beyond her years, Maegan garners respect for her wide-ranging knowledge and industry acumen, and leaves a lasting impression with everyone she meets,” states CJ Cannata, CEO and President, The Cannata Report. “It is an honor to include Maegan as one of our 2019 Women Influencers, making her one of only two executives in the industry to have been named both a Women Influencer and a Young Influencer by The Cannata Report.”
Körber acquires majority stake in Cohesio Group
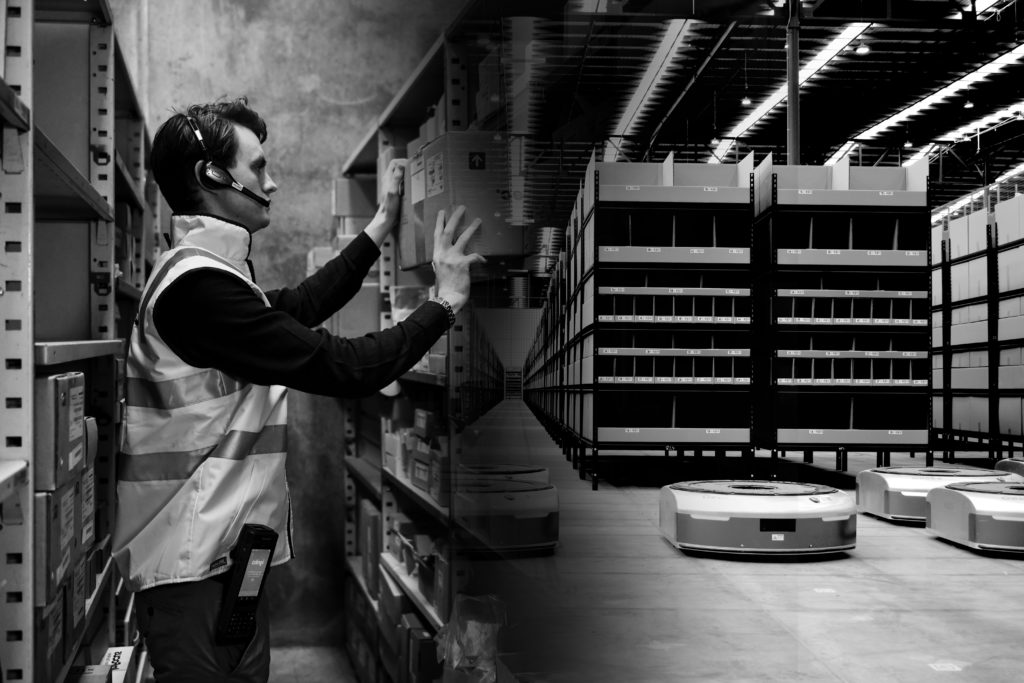
The international technology group Körber strengthens its Business Area Logistics Systems by acquiring a majority stake in Cohesio Group Ltd. The Australian-based company is a leading integrator of voice-directed and autonomous mobile robotics (AMR) solutions for logistics. The acquisition was completed effective September 20, 2019. The Cohesio Group, headquartered in Melbourne, within just a few years established itself as one of the leading providers of voice-controlled and robotics software solutions for the logistics industry, particularly in the Asia Pacific region (APAC). Cohesio will complement the Business Area’s existing voice solutions business with its market-leading brand Voiteq. This strengthens one of the world’s largest and most experienced Honeywell Vocollect voice integration teams. Cohesio has also pioneered the deployment of autonomous mobile robotics solutions in the region. “With Cohesio, we are underpinning our claim to ‘market leadership through technology leadership’ in the future-oriented fields of voice and robot technology,” says Stephan Seifert, Chairman of the Group Executive Board at Körber AG. “We are also expanding our presence in the particularly fast-growing markets of the APAC region, where we are able to inspire and support our customers with the best products and solutions for the supply chain”. Dirk Hejnal, CEO of the Körber Business Area Logistics Systems, adds: “With its broad, technology-oriented product and service portfolio, Cohesio is an ideal fit for us and our growth ambitions. By adding Cohesio, we are in an even stronger position to offer customers the right supply chain technologies and service them on a global level. The Cohesio team is characterized by entrepreneurship, years of experience with logistics technologies, and a history of good partnership with its customers”. Nishan Wijemanne, CEO of Cohesio Group Ltd. says: “We feel fortunate to have found a partner in Körber that can help accelerate the next stage of growth for Cohesio. Körber offers us an innovative culture, a broader portfolio of complementary supply chain technologies and access to customer relationships on a global scale. The Cohesio founders and the entire Cohesio team are very excited to be part of this international technology group”.
Toshiba spotlights Best-in-Class Printing Systems at PACK EXPO 2019
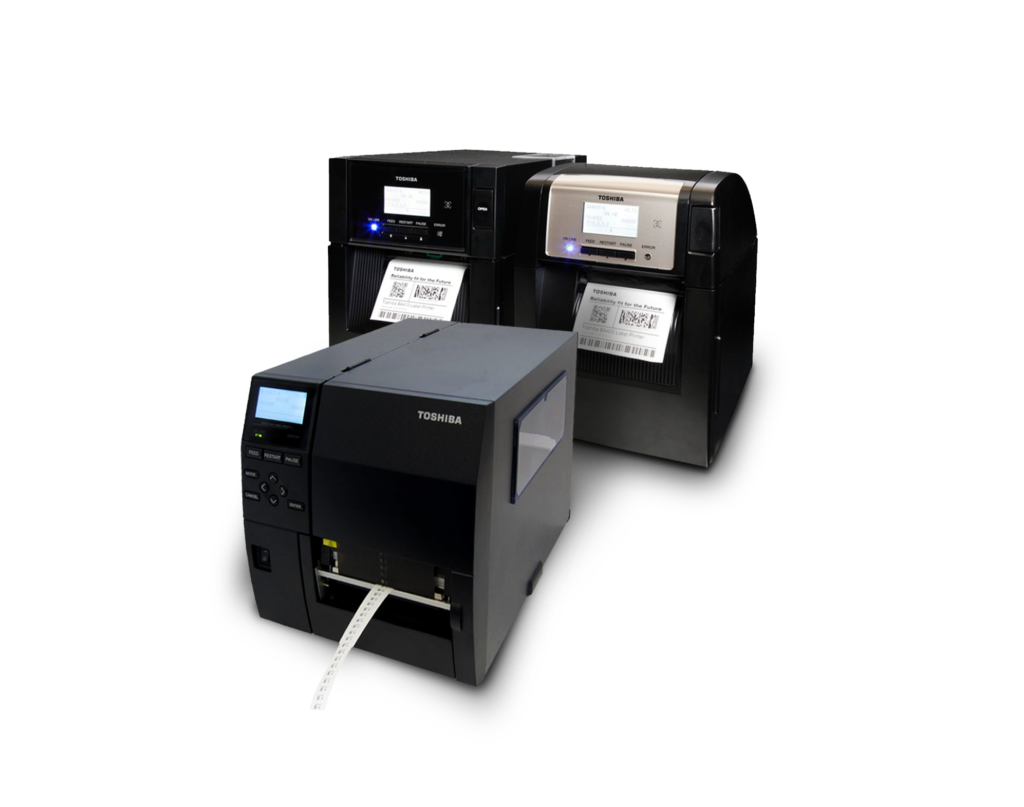
Toshiba’s New Thermal Barcode Printers and Automated Shipping System Collaboration Ensure Shipping Speed, Accuracy and Customer Satisfaction Toshiba America Business Solutions is showcasing two new products at PACK EXPO 2019, Sept. 23-25, booth Upper South Hall 7677, at the Las Vegas Convention Center. The company’s best-in-class pair of thermal barcode printers blend compact and durable designs with precision-accurate labeling. Toshiba also spotlights the Sprinter™ automated shipping system, a product collaboration with Panther Industries and StreamTech. Toshiba’s just-introduced BA400 thermal bar code printer combines the latest in connectivity – USB, Bluetooth, Ethernet and Near-Field Communication – with the necessary throughput (up to eight inches-per-second) to fulfill virtually any manufacturing, distribution, retail and healthcare labeling requirements. Featuring a sturdy, compact design with top-loading for fast media and ribbon swaps, the BA400 integrates easily within most office and warehouse settings. Parts lifecycle alerts and simple printhead and platen replacement further ease product usage. Toshiba’s newly-minted B-EX4T3HS thermal bar code printer creates clear, acutely scannable, high-resolution labels – up to 600 dots-per-inch – with precision accuracy. The B-EX4T3HS is distinctly engineered to tackle pharmaceutical, medical device and electronic component label applications while also addressing the meticulous labeling needs of other compliance-driven organizations. Toshiba’s B-EX4T3HS handles the complexity of printing smaller labels – width and height as small as 0.51 and 0.12 inches respectively – with speed (up to six inches per second) and extreme precision. The printer’s center alignment eliminates media shifts to ensure the consistently accurate placement of barcode data on labels. Toshiba representatives will additionally showcase Sprinter, a product collaboration with StreamTech and Panther Industries. Sprinter leverages Toshiba’s best-in-class thermal barcode printer technology, Panther Industries’ Shadow print and apply product, and StreamTech’s conveyor featuring automatic weight and dimensioning capabilities. Sprinter easily integrates within existing supply chain and logistics environments to affordably fulfill e-commerce orders while automating the shipping process. “We are looking forward to visiting with supply chain and logistics professionals from across North America while demonstrating the compelling blend of innovation and low total-cost-of-ownership our products deliver,” said Toshiba America Business Solutions Chief Marketing Executive Bill Melo. “Toshiba’s newest printers and latest product collaboration with Panther Industries and StreamTech will simplify as well as accelerate the shipping and e-commerce fulfillment process for logistics operations, which is essential to maintaining customer satisfaction and retention.” “Panther Industries’ Shadow Printer-Applicator using the Toshiba B-EX4T1 is a great fit for StreamTech’s Sprinter automated dimension, weigh, label and scan order-fulfillment application, which delivers up to 1,500 parcels per hour in an all-in-one, cost-effective manner,” said Bob Miller, StreamTech’s Applications Manager. “Sprinter may also be implemented as overall control platform for small to medium fulfillment conveyor system operations.” Toshiba’s BA400 and BEX4T3HS printers have a beginning list price of $1,195 and $4,780, respectively. Both products are now available for purchase via authorized Toshiba resellers. To learn more about Toshiba thermal barcode printers or to locate an authorized Toshiba reseller in your area, visit www.business.toshiba.com. A one-year return to depot warranty is standard with Toshiba’s B-EX4T3HS, BA400 and all other Toshiba printers.
DENSO, Creator of the QR Code, reflects on the technology’s progress 25 years after its invention
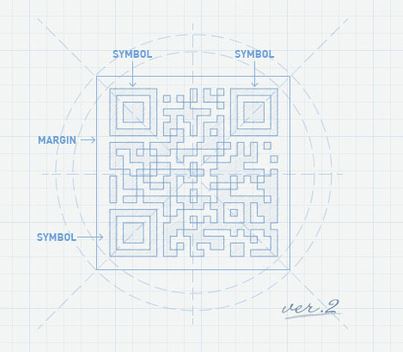
A quarter century after its creation, DENSO’s invention has evolved to become an essential technology across the globe DENSO, the world’s second largest mobility supplier, is celebrating the 25th anniversary of its invention of the QR code. The technology, a machine-readable code used for storing information, was created by DENSO-subsidiary DENSO WAVE with the goal of achieving more detailed production management at manufacturing sites. To commemorate the anniversary, DENSO WAVE has launched a new website that traces the history, future and benefits of this now-ubiquitous technology. In the 1980s, barcodes were widely used for manufacturing and distribution processes. However, within a decade, an industry shift from mass manufacturing to more flexible production required a stronger barcode. A two-person DENSO development team was tasked with the challenge, needing to create a code that could store more information, be read at a higher speed and fit on smaller surfaces. To accomplish this, the team spent nearly two years creating a design with a specific position detection pattern ratio – 1:1:3:1:1. These codes were two dimensional and could hold approximately 7,000 numerals, allowing them to be read more than 10 times faster than a traditional barcode. Though QR codes were originally developed to create efficiencies in manufacturing processes, DENSO encouraged its use more broadly by making the technology license-free. Since its invention, the popularity of QR codes has spread to encompass numerous industries, including: hospitality and tourism, education, and real estate. The codes have contributed to the growth of cashless payment systems, are used to trace foods, pharmaceuticals and other merchandise, and are regularly seen on event tickets and advertisements. “Throughout its development, the QR code represented the type of innovation that DENSO strives for in its efforts to shape the future of mobility,” said Kenichiro Ito, senior executive officer for DENSO Corporation and chief executive officer of DENSO’s North American Headquarters. “Twenty-five years later we can clearly see its vast and impactful results. It is this sort of long-term vision that we look to emulate today to not only improve upon what has already been built, but to create new products and services that will inspire a better future.” Since launching the QR code in 1994, DENSO WAVE has further advanced QR technology to meet social needs with its iQR code, its SQRC code and its Q-revo protection service.
e-matica and Seeq announce partnership to deliver Advanced Analytics Solutions
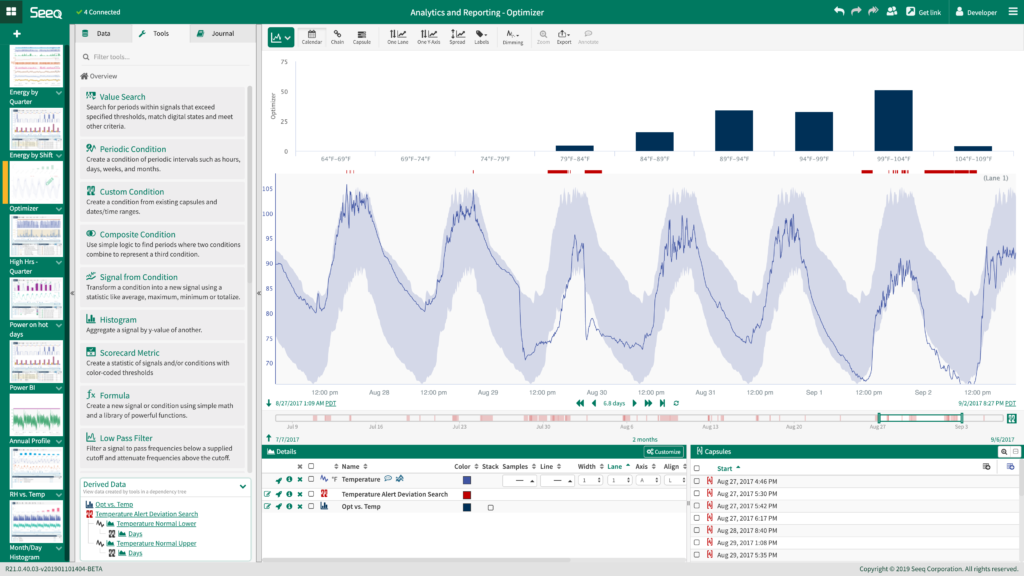
Partnership will provide acceleration of digital transformation in Italy e-matica, a systems integrator and applications development firm and a Select Partner for OSIsoft® and Seeq®, headquartered in Seattle, Washington, will partner to deliver advanced analytics solutions to their customers. The partnership will accelerate digital transformation by harnessing diagnostic and predictive analytics to enable greater operational efficiency and deeper insights across organizations. Seeq software applications, Seeq Workbench and Seeq Organizer, enable manufacturing organizations to rapidly analyze, predict, collaborate, and distribute insights to improve production outcomes. Seeq is designed to run on-premise, on Microsoft Azure or Amazon Web Services cloud platforms, or in mixed on-premise and on-cloud deployments. e-matica has provided innovation and process improvement to their clients for over 20 years in industries like power generation, oil & gas, pharmaceuticals, specialty chemicals, and others. Combined with Seeq’s advanced analytics solution, the partnership is a natural fit that will benefit e-matica customers as they strive to get more value from their operations data. “The decision to enter into a partnership with Seeq is in line with our growth strategy aimed at offering innovative solutions to help our customers improve their operations. Our customers work with data from different sources and have the need to analyze them effectively and efficiently—time is a key factor! Seeq makes it possible to find insights and share critical information quickly,” says Luca Spingardi, e-matica Business Development Executive. This sentiment is shared by Ernesto Bove, CEO, and Giuseppe di Bartolo, Sales Director, who have deployed many systems based on the use of historicized data for important Italian customers. “Thought leaders like e-matica, with local customer and vertical market expertise, are critical to the success of Seeq,” adds Will Knight, Head of Partner Sales for Seeq. “Our customers rely upon them to deliver advanced analytics solutions that provide insight and drive results.”
Toshiba’s latest Thermal Barcode Printer tackles compliance-driven applications
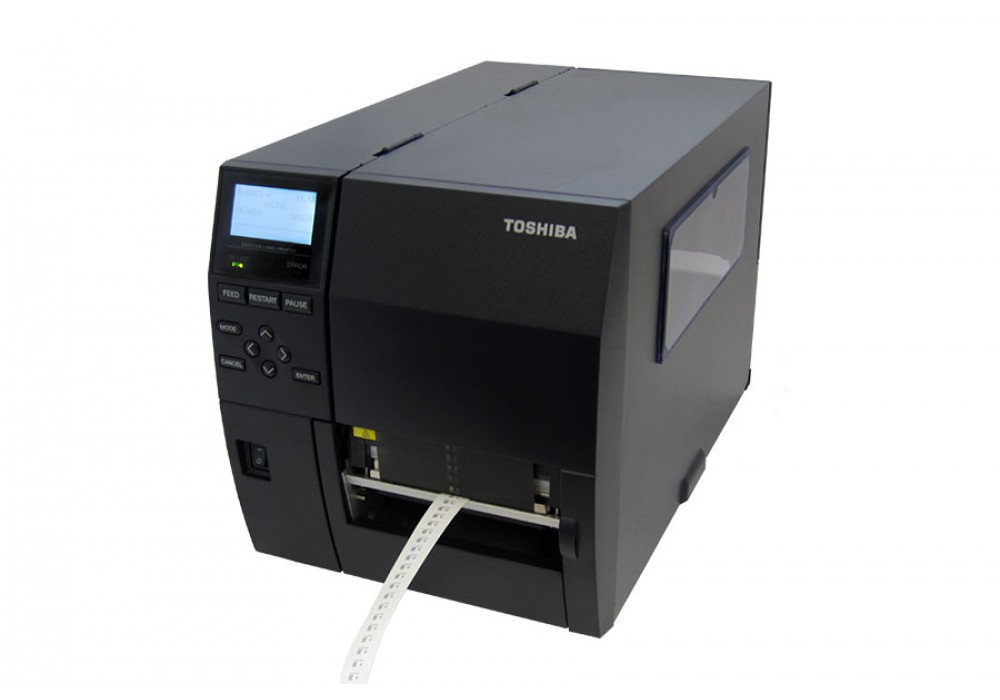
Specialized new printer delivers high-resolution labeling with precision accuracy Toshiba America Business Solutions today unveils its premium thermal barcode printer which delivers high-resolution labels with precision and speed. Toshiba’s B-EX4T3HS prints 600 dots per inch at speeds up to six inches per second. In addition, Toshiba’s printer delivers extreme accuracy and can print labels as small as 0.51 inches wide by 0.12 inches high. Toshiba’s new device combines accuracy and high-resolution by using center alignment which eliminates media shifts to ensure consistently accurate placement of barcode data on small labels. Producing these specialized labels in-house lowers the cost of operations by eliminating compliance issues and costs associated with printing unusable tags. “Toshiba’s latest thermal barcode printer is the ideal product for pharmaceutical, medical device and electronic components businesses, as well as logistics and manufacturing professionals within compliance-centric companies,” said Toshiba America Business Solutions Chief Marketing Executive Bill Melo. “Ultra-high resolution with precision accuracy labeling helps to improve supply chain efficiency and meet global quality compliance standards that our customers require.” Toshiba’s B-EX4T3HS printer has a list price of $4,780 and is now available for purchase from authorized Toshiba resellers. To learn more about Toshiba thermal barcode printers or to locate an authorized Toshiba reseller in your area, visit www.business.toshiba.com. The B-EX4T3HS and all other Toshiba printers feature a one-year standard return to depot warranty.
Septentrio introduces a new GNSS/INS system in a rugged housing
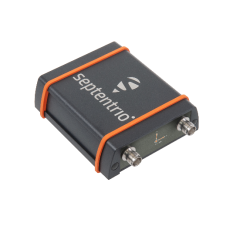
Septentrio expands their GNSS/INS portfolio with AsteRx SBi. This ruggedized receiver fuses high-accuracy GPS/GNSS with a high-performance inertial sensor to provide reliable positioning and 3D orientation, ideal for machine control and logistic applications Septentrio, a global supplier of high-accuracy positioning technology for demanding applications, unveiled recently AsteRx SBi, a new housed GNSS/INS receiver. Within its rugged, waterproof enclosure a high-performance GPS/GNSS is coupled with an industrial-grade inertial sensor to provide high-accuracy, reliable positioning and 3D orientation (heading, pitch, roll). Offering the flexibility of either single or dual antenna, AsteRx SBi is designed for quick and easy integration into any machine monitoring or control system. AsteRx SBi packs performance and durability into a single, compact box. Reliable location and 3D orientation data is streamed with a high update rate and constant low latency. “AsteRx SBi was designed with ease of integration and reliability in mind. Its compact, ruggedized housing is optimized for easy clamping to any machinery,” said Danilo Sabbatini, Product Manager at Septentrio. “It has all the features and tools needed for straightforward integration into machines or large robotic systems.” Septentrio reliable centimeter-level positioning is based on true multi-frequency, multi-constellation GNSS (GPS, GLONASS, Galileo, BeiDou, QZSS) technology. AsteRx SBi combines GPS/GNSS and an industry-grade IMU (Inertial Measurement Unit) to deliver precise positioning together with 3D attitude. Septentrio’s unique GNSS – IMU integration algorithm enables continuous positioning in environments of low satellite visibility where short GNSS outages are possible. This is referred to as coasting or dead reckoning and can happen near high structures, under bridges or under thick foliage. This makes AsteRx SBi a robust positioning solution for machinery operating in environments challenging for GNSS, such as in container yards, urban canyons or near cliffs. AsteRx SBi comes with built-in industry leading Advanced Interference Mitigation (AIM+) technology. In busy urban environments electromagnetic waves can interfere with GPS and GNSS signals. AIM+ offers protection against such interference resulting in faster set-up times and robust continuous operation. A built-in power spectrum plot allows users to analyze interference, helping locate its source and mitigating it.
Sensera Systems launches PTZ500 Panoramic Jobsite Camera
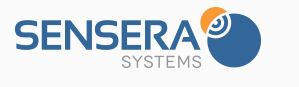
Sensera Systems, Inc., a leading provider of comprehensive, real-time jobsite monitoring solutions today announced the release of its new PTZ500 Solar and AC-Powered camera models. Sensera PTZ500 site cameras offer Sensera’s essential and advanced features while enabling customers additional flexibility to round out their jobsite solution. The Sensera PTZ500 camera was designed as a flexible site monitoring solution for progress documentation, productivity, and safety applications on jobsites. Ideal for large-scale sites requiring a wide coverage area and fine detail, this powerful camera provides professional-grade time-lapse video, ultra-high-resolution panoramas, and live video streaming with interactive pan-tilt-zoom. The PTZ500 is Sensera’s most advanced camera model, yet still provides breakthrough price points for a solar/wireless PTZ system. It offers simple setup while delivering fully automated panoramas, daily automatic and on-demand time-lapse, as well as edge recording to capture safety and security events. The wide optical zoom and pan-tilt ranges provide coverage for the largest projects while capturing detailed as-built imagery. The unit supports live video streaming, as well as standard SiteCloud camera features like public URL, LiveView, and more. Features & Benefits Ultra-high resolution, wide angle panoramas On-demand pan-tilt-zoom to view fine detail on the largest job sites in real-time Automated scheduled panoramas Integrated modem for cellular/LTE or WiFi connectivity Compact solar, lightweight, easy to move/reposition Sensera site cameras are powered by Sensera’s SiteCloud® platform which provides easy-to-use software for viewing, monitoring, and sharing real-time site data, detecting actionable insights, and simplifying work-flow. SiteCloud is tightly integrated with Sensera’s complete line of jobsite cameras, SitePOV™ mobile app, and SiteCloud-AERIAL™ drone photography services to support improved productivity, quality, safety, and automated documentation from one simple web interface. SiteCloud service includes WiFi and 4G LTE connectivity making it a true end-to-end solution. Integrations with Autodesk® BIM 360, Procore®, and PlanGrid simplify and automate workflow across the enterprise. “One of our goals has been to continue to drive down costs and create more convenient options for the deployment of jobsite cameras to provide 100% site coverage. By listening to our customers, our product team developed the PTZ500 model to be our most flexible and powerful camera system yet. The automated panorama capability is amazing and will be a great fit for wide projects, tall urban buildings, and larger sites. The PTZ500 is an important step in continuing to deliver on our mission of providing General Contractors and Owners powerful tools for improving productivity, quality, safety and site security,” said David Gaw, Founder and CEO, Sensera Systems.
Cybersecurity best practices
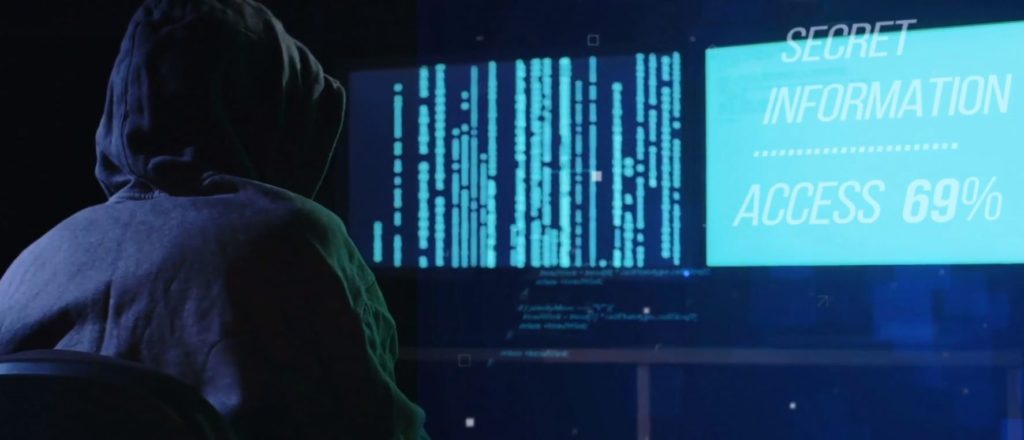
Security is essential to any business. People don’t question security precautions for the people, building, or machines in an organization. But what about your data? To view this video, click here.
New midrange, Industrial Toshiba Printers accelerate and simplify labeling
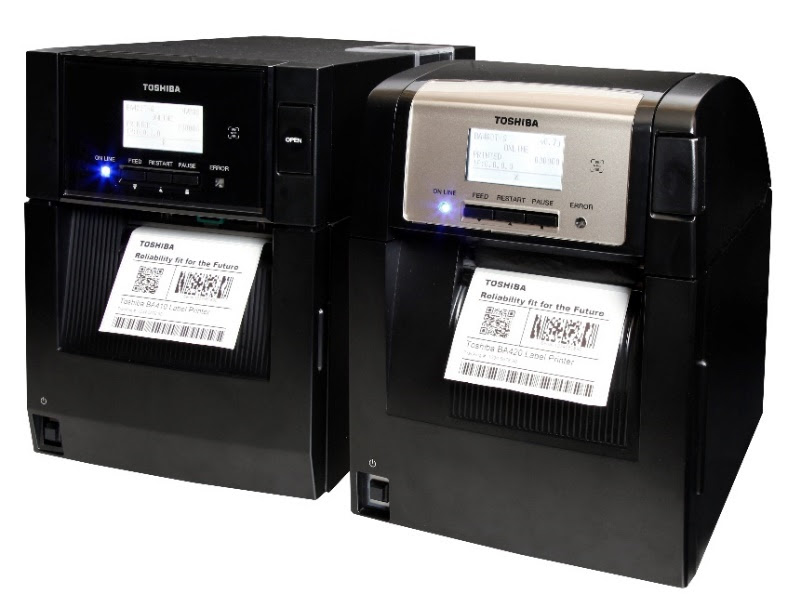
Printers combine Speed, Accuracy & Intuitive functionality to optimize labeling needs for logistics operations Toshiba America Business Solutions simplifies labeling applications with the unveiling of its next-generation BA400 midrange, industrial thermal barcode printers. Toshiba’s new printers combine speed (up to eight label inches-per-second) and high-print quality (up to 300 dots-per-inch labels) to support professionals in manufacturing, distribution, retail and healthcare. The streamlined and durable chassis – available in both metal and rugged plastic models – allows for easy installation within even the most space-sensitive environments. The design and simple operation enable consistent and continuous labeling output for mid-volume applications. The BA400 printers incorporate intuitive elements for ease-of-use and low maintenance. A top-loading design provides user-friendly media and ribbon replacement. Parts lifecycle alerts and simple printhead and platen replacement increase uptime for logistics professionals. The Toshiba printers also integrate the latest in USB, Bluetooth, Ethernet and Near-Field Communication (NFC) connectivity. NFC connectivity enables BA400 printers to pair with other NFC embedded devices such as smartphones, handhelds and mobile computers. Compatibility with Zebra ZPL®, Sato and Toshiba program languages allows easy emulation and seamless integration within existing warehouse and retail settings. “We introduced our latest thermal barcode printers to simplify organizations’ labeling applications,” said Toshiba America Business Solutions Chief Marketing Executive Bill Melo. “Toshiba’s intuitive functionality and next-generation technology accomplish this objective by empowering logistics professionals to operate more efficiently and effectively.” Toshiba’s BA400 printers have a starting list price of $1,195 and are now available for purchase via authorized Toshiba resellers. To learn more about Toshiba thermal barcode printers or to locate an authorized Toshiba reseller in your area, visit www.business.toshiba.com. A one-year return to depot warranty is standard with Toshiba’s BA400 and all other Toshiba printers.
Industrial Scientific introduces Wi-fi Battery for Ventis® Pro5 Multi-Gas Monitors
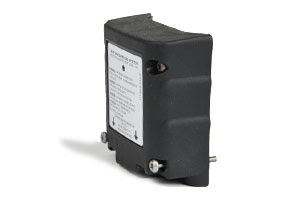
New wi-fi battery instantly transmits data from Ventis Pro5 monitors to iNet Now for real-time monitoring using existing infrastructure Industrial Scientific, a global provider in connected sensing technology, has announced the expansion of its connected safety portfolio to include a new wi-fi battery for the Ventis Pro5 Multi-Gas Monitor for customers in the United States and Canada. The new battery uses standard wi-fi networks to instantly transmit data directly to cloud-based iNet® Now software, providing real-time alerts and visibility into gas hazards, panic, and man-down situations. With data transmitted instantly to iNet Now, safety managers can receive real-time alerts when a worker is in distress and quickly access the data they need to monitor sites, keep workers safe, and make smart decisions in the moment. Real-time insights on where workers are located and what hazards they face gives organizations the power to increase productivity, reduce risk, and strengthen their safety culture. “We believe that instant visibility into worker safety will save more lives and provide our customers with valuable insights to continuously improve worker safety,” said Tae-Yeon Won, product manager at Industrial Scientific. “The new wi-fi battery gives organizations easy, cost-effective access to live monitoring.” The new wi-fi battery will run 16 hours on a single charge and is compatible with existing chargers and the DSX™ Docking Station. Current Ventis Pro5 customers can easily convert their personal multi-gas monitor to a wirelessly-connected wi-fi monitor by simply switching the battery pack. The wi-fi battery is also available as an option for all new Ventis Pro5 Multi-Gas Monitors. Learn more about wi-fi batteries for the Ventis Pro5.
Koch Engineered Solutions to offer Powerhouse Analytics capabilities with addition of EFT analytics
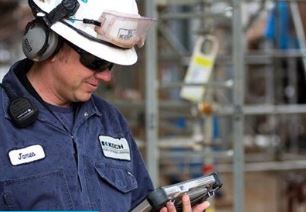
KES will expand its solutions offerings, strengthen its industry expertise, and broaden its global presence through EFT’s analytics platforms Koch Engineered Solutions (KES), a unit of Koch Industries, Inc. focused on developing and delivering innovative technical and service solutions for industrial value chains, today announced it is adding advanced analytics and energy management solutions to its wide-ranging and growing product portfolio. EFT Analytics (EFT), a leading provider of predictive analytics, process optimization, and energy management solutions, will join the KES family of companies, broadening KES’s global presence and allowing it to deliver more unique value to customers across various industries. “KES is always striving to offer actionable solutions to our customers, and the addition of EFT allows us to bring a whole new set of data-focused capabilities to the table,” said Dave Dotson, president of KES. “By combining EFT’s analytics platforms with KES’s deep domain expertise and knowledge in advanced engineering capabilities and equipment, we’re creating truly world-class solutions for our industrial customers. We’re able to help them use their data to be more efficient, more compliant, and ultimately, more profitable.” EFT provides operations experts in the field with actionable insights via complex analysis to make work more effective and meaningful. The company brings its innovative CORTEX advanced analytics and Energy Manager platforms, which are proven solutions used across a variety of industries from refining, to pulp and paper, to the steel industry and beyond. Customers are now poised to gain greater value than ever before with EFT’s data analytics expertise integrated into KES’s full-service solutions. “KES has a long history of creating innovative hardware, design, and process solutions for its customers across a wide range of industries,” said Brent Youngers, president of EFT. “When we layer on EFT’s advanced analytics and machine learning capabilities, we can offer those customers the next evolution of service by operationalizing their data and putting the power of real-time actionable analysis into the hands of subject matter experts and operators.” The addition of EFT to KES builds upon a successful partnership history between the two companies. In January 2019, EFT began working with KES subsidiary John Zink Hamworthy Combustion on Smart Combustion technology. As part of that partnership, the companies are focusing on the commercialization of a Smart Combustion solution – Ember – for customers in industrial value chains. Ember will allow facilities to optimize control of their combustion systems, improving production efficiency, asset health, and environmental performance.
Honeywell helps Apparel Logistics Group triple daily output from its e-commerce distribution center
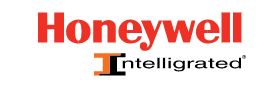
Honeywell has signed an agreement with retail supply chain services provider The Apparel Logistics Group to help the company expand the e-commerce order output at its distribution center in Dallas. Under the agreement, Honeywell Intelligrated will deliver automated material handling solutions to The Apparel Logistics Group, a leading provider of third-party logistics and order fulfillment services for apparel, footwear and accessories. Honeywell Intelligrated’s technology and technical support services will help the logistics provider expand its e-commerce parcel shipping capability, increase productivity at the shipping dock, ensure order accuracy and expand its value-added services capacity, which includes returned merchandise management and product customization. These material handling solutions and services will enable The Apparel Logistics Group to more than triple its daily e-commerce order output. “The third-party logistics (3PL) sector is experiencing unprecedented growth as more retailers require cost-effective order management, reverse logistics and product customization services,” said Pieter Krynauw, president, Honeywell Intelligrated. “In turn, 3PLs need to deploy automation solutions to help them ensure quality control, reduce risks associated with labor availability and deliver on their service-level agreements.” Located in Dallas to support fast shipping throughout the U.S., the 240,000-square-foot facility features an array of dedicated automation solutions including a high-volume sortation system and more than five miles of controlled conveyors. “To keep pace with growing consumer expectations, both traditional retailers and online-only e-tailers need to outsource their order fulfillment, returned merchandise management and product customization. In addition, available warehouse space in North America is at an all-time low,” said Aric Schwab, Senior Vice President, The Apparel Logistics Group. “With these new facility enhancements, we’re able to offer our customers increased volume, faster shipping and more value-added services.” Honeywell Intelligrated will install new material handling solutions to more efficiently move products through nutat The Apparel Logistics Group’s distribution center, which provides retailers with a one-day turnaround on e-commerce orders. In addition, Honeywell Intelligrated will implement and support the facility’s warehouse control system, which operates the production activities and equipment. This provides The Apparel Logistics Group with direct support from Honeywell Intelligrated’s world-class technical services center and 24/7 access to maintenance technicians to maximize facility uptime. Large retail brands and online-only retailers in the U.S. and Canada turn to The Apparel Logistics Group for warehousing, multi-channel order fulfillment and Foreign Trade Zone services to deliver products to distribution centers, stores or directly to individual consumers’ homes.nuts Honeywell Intelligrated is a leading provider of automation solutions for distribution and fulfillment applications with decades of experience helping 3PLs achieve maximum productivity and efficiency by transitioning from manual to automated processes. The Apparel Logistics Group provides multi-channel fulfillment and supply-chain services to clients in the apparel, footwear and accessories industry. The company is a business unit of The Apparel Limited (TAL), a global manufacturer of woven and knit apparel producing more than 50 million garments annually. Honeywell Safety and Productivity Solutions (SPS) provides products, software and connected solutions that improve productivity, workplace safety and asset performance for our customers across the globe. We deliver on this promise through industry-leading mobile devices, software, cloud technology and automation solutions, the broadest range of personal protective equipment and gas detection technology, and custom-engineered sensors, switches and controls.
Smartrac launches new NFC PRO Series
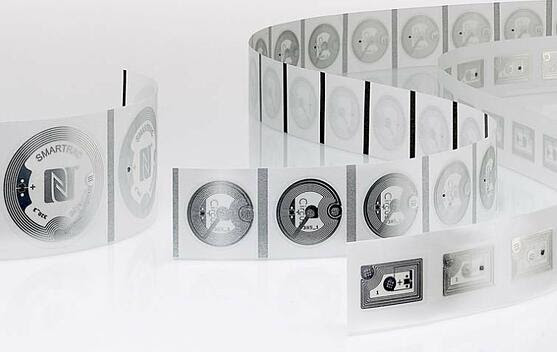
Smartrac Technology Group, a global provider in RFID technology and IoT solutions, has launched the new PRO series of its market leading portfolio of NFC tags and inlays. The company’s NFC tag CIRCUS PRO, equipped with NXP’s NTAG® 424 DNA IC, will be the first member of the new product series optimized for highly secure product authentication. By embedding Smartrac’s new CIRCUS PRO – or any other future PRO inlays or tags – into physical products, customers such as brand owners and branded product manufacturers can turn their products into secure digital platforms, delivering unmatched value during the product lifetime from point of manufacture, through the supply chain, distribution channels, point of sales, customer usage phase, to reselling and recycling. Key applications enabled by secure product authentication are counterfeit and diversion protection as well as exclusive content and rewards for consumer engagement and customer loyalty programs. Protection against “the most sophisticated counterfeiting attempts” “As the number of connected objects is expected to reach a record 40 billion by 2022, organizations of all sizes are seeking not just feature-rich, connectivity solutions but ones that can securely protect their brand, their products, and their customers,” said Philippe Dubois, Vice President and General Manager of IoT Security, Smart Mobility and Retail at NXP. “Our NTAG 424 DNA sets the bar when it comes to delivering such trusted experiences and Smartrac’s CIRCUS PRO takes full advantage of its cutting-edge security and privacy features to deliver an all new generation of NFC tags that can fight even the most sophisticated of counterfeiting attempts.” NFC PRO series: secure authentication with tailored security and layers Smartrac’s new CIRCUS PRO inlays and tags with NXP’s NTAG 424 DNA IC’s work with all NFC-enabled devices and support real-time tag and message authentication based on AES-128 encryption on attack-resistant certified silicon. The Secure Unique NFC (SUN) authentication feature enables authentic, integrity protected and confidential data exchanges between tags and servers. This high-end security IC option offers enhanced privacy features and a sensitive on-chip data storage, protected by a sophisticated three-pass mutual authentication scheme. Future PRO features and options will also include different security layers, allowing customers to enable secure product authentication for a wide range of needs and applications. Offering a variety of different NFC product designs, form factors and IC options for individual customer demands, Smartrac will soon introduce further PRO versions of its popular NFC inlays and tags such as BULLSEYE and MIDAS. Fighting counterfeiting and boosting digital consumer engagement Moreover, the NFC-based secure product authentication can be achieved through a choice of verification services, in order to comply with the greatest possible array of individual customer requirements. As the secret keys cannot be copied or tampered, physical product authenticity can be proven in a highly reliable manner once the PRO inlays and tags are irremovable embedded into or attached to the physical product. Smartrac’s new PRO series will also allow to fully leverage the company’s IoT solutions portfolio, enabling customers not only to minimize product counterfeiting through secure authentication, but also to deliver exclusive digital content to consumers for enhanced customer loyalty and satisfaction. “Today’s introduction of the new CIRCUS PRO NFC tag with NXP’s NTAG 424 DNA IC is a milestone for us in two respects: As the forerunner of our innovative PRO series, the new tag enables our customers to effectively fight counterfeiting with a variety of highly secure functionalities, and at the same time provides consumers with exclusive, instant digital content through existing devices and channels. Moreover, CIRCUS PRO NFC tag based on NXP’s superior IC is another confirmation of our proven, long-time partnership with NXP that will reshape the RFID market,” says Hal Hikita, SVP Product Market Development at Smartrac. Regarding its physical and performance characteristics, the new CIRCUS PRO falls within the highly successful product line that features CIRCUS DURA, CIRCUS FLEX, CIRCUS ON-METAL and CIRCUS TAMPER LOOP NFC inlays and tags, which all combine small size, cost-effectiveness and superior performance. For regular and demanding physical environments Smartrac’s CIRCUS PRO NFC inlays and tags with NTAG 424 DNA will become available in large quantities in Q3 2019 as wet inlays, as well as the new CIRCUS PRO FLEX wet inlays, which come with an additional “glop top” protective layer for the IC and antenna connection area for enhanced durability in challenging environments.