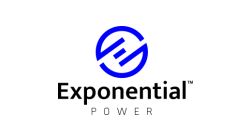
Exponential Power acquires Static Power
Exponential Power, Inc., a provider of stored power solutions, today announced its strategic acquisition of Maryland-based Static Power, a well-known
Exponential Power, Inc., a provider of stored power solutions, today announced its strategic acquisition of Maryland-based Static Power, a well-known
In a market with reported labor shortages and shifts in supply chain conditions, material handling companies have a series of
Integrates Unique Behavioral Analytics for Public Safety Atos has announced its new partnership to integrate viisights software into its Atos
Owing largely to the burst of business activity in the spring and early summer that came in part thanks to
Configura integrates forklift trucks and warehouse equipment from Linde Material Handling into CET Material Handling Planning and engineering offices can
Sternhagen receives Honor for Demonstrating Leadership across Toshiba & Community Affirming her extraordinary leadership at Toshiba America Business Solutions and within
Hikvision, a global provider in delivering high-performance professional security solutions with tremendous value, is introducing a highly versatile standalone mobile
The expanded platform identifies and lowers manufacturing operational costs Synapse Wireless, Inc., a member of the McWane family, recently expanded
Oshkosh Corporation, an innovator of mission-critical vehicles and essential equipment, and Carnegie Foundry, a robotics and artificial intelligence (AI) venture
GEODIS, a global transport and logistics provider, and Advanced Handling Systems (AHS, LLC), a full-service provider of integrated fulfillment and
Built for the highest reliability and certified for Google Mobile Services (GMS), the new JLT6012A™ computer brings the productivity-boosting benefits of the Android 10 operating system to customers in all types of logistics
Gamber-Johnson has announced the availability of six new protective handheld technology docking cradles to support the popular Zebra TC5X and
François Mandeville to lead M&A function and help drive business growth strategy Mandeville brings a wealth of corporate development leadership
Zethcon Corporation, a provider of warehouse software for 3PL providers, announces the latest standard release of its flagship product, Synapse
Provides A Single Platform to Remotely Manage Physical Security Operations Hikvision’s HikCentral Professional platform provides a centralized software solution to remotely
Attendees Will Learn How Savvy Companies Gain Competitive Advantage Using Technology and How They Layer Those Technologies Together as a
Panasonic i-PRO Sensing Solutions Corporation of America, a subsidiary of Panasonic i-PRO Sensing Solutions Co., Ltd. and a global leader
On this episode, I was joined by the Vice President of Product Strategy at SOTI, Shash Anand. SOTI is a
On this episode, I was joined by two guests from Panasonic, Dan Diliberti and Mike Bates. We discuss the new
IDEC Safety Commander provides a unique, practical, and patented way for operators to use modern tablet interfaces with industrial machinery