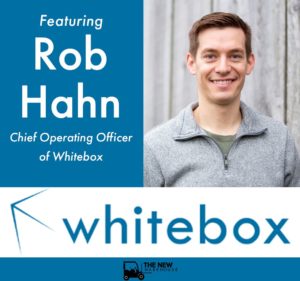
EP 155: Whitebox
In this episode, I was joined by the Chief Operating Officer of Whitebox, Rob Hahn. Whitebox handles all of your
In this episode, I was joined by the Chief Operating Officer of Whitebox, Rob Hahn. Whitebox handles all of your
New cloud-based addition, Fleet Geek, optimizes autonomous mobile robot performance, drives continuous improvement, and demonstrates impact of automation across the
Enhanced Capabilities Transcend Security to Deliver Business Intelligence Panasonic i-PRO Sensing Solutions Corporation of America, a global provider of advanced
Appointing a CEO to lead its separate new software venture, JLT takes the next strategic step towards realizing its vision
The Rufus RADD™ Tab delivers increased visibility into warehouse operations and can be used on warehouse forklifts and vehicles Rufus
Changes reflect market trends, strong subsidiary growth, and the increased importance of KNAPP’s North American Market and Customer Base KNAPP,
Newcastle Systems, a provider of industrial mobile-powered carts designed to make warehouses, manufacturing facilities, and retail floors more efficient, is
Veteran Toshiba Employee to Lead Company’s Toner Operations Toshiba America Business Solutions has promoted Teresa Sternhagen to general manager of
Rapidly Growing Autonomous Mobile Robot Provider Increases Strength and Depth of Leadership to Meet Growing Demand for Industrial Automation Seegrid
FleetCloud™ transforms MHE processes to drive safety, compliance, and productivity Kenco Logistics, one of North America’s leading third-party logistics providers,
In this episode, I spoke with Jon Schechter who is a Business Development Manager at AutoStore. We just recently spoke
Bring together 60 years of expertise to deliver customers and partners an expanded choice of solutions and enhanced capabilities Loftware,
BSN, a one-stop solution provider for RFID and supply chain technology, announces a successful year of industry growth, employee retention,
In this episode, I was joined by James Sramek of SmartBOL. James does enterprise sales at SmartBOL and came on
The new version of the 3D printing Software 4D_Additive uses artificial intelligence algorithms to achieve an optimal heat distribution. For
Video Insight VMS Plug-In and MOBOTIX Thermal Cameras detect elevated skin temperature and issue alerts Panasonic i-PRO Sensing Solutions Corporation of
In this episode, I caught up with the CEO and co-founder of Rufus Labs, Gabe Grifoni. I last spoke with
Reusable IoT Pallet Supplier Recognized for ELIoT™ Embedded Traceability Technology Food Logistics has named RM2 to its 2020 FL100+ Top Software
Vanderlande has installed its advanced AIRTRAX Pocket for de Bijenkorf at its Tilburg warehouse, the first large-scale system of its
In this episode, I was joined by Jonathan Wright of IBM. Jonathan is the Global Head of Cognitive Process Reengineering