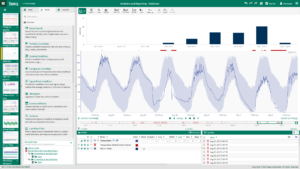
Seeq Number 76 Fastest-Growing Company in N.A. on Deloitte’s 2020 Technology Fast 500
Recognition for Seeq revenue growth and innovation reflects the success of their customers for improving business and operations outcomes through
Recognition for Seeq revenue growth and innovation reflects the success of their customers for improving business and operations outcomes through
New capabilities make product throughout more efficient and provide advanced analytics Stoecklin Logistics, a supplier of innovative supply chain solutions,
Built for easy integration into industrial environments and systems, this new RFID device lets OEMs and end-users implement secure equipment
In this episode, I was joined by former guest Mark Wheeler of Zebra Technologies. Mark is the Director of Supply
U.S. Manufacturing Technology Orders totaled $373.7 million in September 2020, an increase of 26.4% from August 2020, and the highest
Easy to hold due to its small form factor and lightweight—and includes a touchscreen, function keys, and switches—making it a
Zethcon Corporation, a provider of modern warehouse software, has successfully implemented its flagship product, Synapse WMS, to manage 6 million
In this episode, I was joined by Ranga Bodla of NetSuite. Ranga is the VP of Field Engagement and Marketing
Crosby|Straightpoint has launched its multifaceted INSIGHT software that allows users to monitor up to 126 load cells from up to
Engineered to fit into tight vehicle cabins, JLT’s new RISC-based VM3010A computer brings the operational efficiency advantages of Android to a
In this episode, I was joined by Dave Crist who is the President of Brother Mobile Solutions. We discussed their
Septentrio’s first-of-a-kind SECORX-S GPS/GNSS receiver product line offers sub-decimeter accuracy without the need for additional positioning service subscriptions Septentrio, a provider in high-precision GNSS positioning solutions, announced today
The EtherNet/IP update for IDEC MicroSmart FC6A Plus PLCs is also a free upgrade for existing CPUs, enabling interconnection with
Second expert guide by a leading supplier of rugged mobile computing devices and solutions for logistics, warehousing, and other challenging
Expanded capabilities provide advanced data sharing, capacity planning, shipment tracking and optimized payment, insurance, and compliance processes across global supply
Welcome to the new normal. COVID-19 has left a legacy of communication obstacles that we never thought possible prior to
ROVA, a revolutionary on-demand delivery platform headquartered in the Boston market, has named Charles (Chuck) Moyer of Franklin, TN to
U.S. manufacturing technology orders decreased 5% in May from the previous month to $219.4 million, according to the latest U.S.
In this episode, I was joined by Colin Mansfield who is the Director of Sales and Marketing at Yard Management
A supplier of rugged mobile computing devices and solutions for challenging environments announces first in a series of ‘how-to’ guides