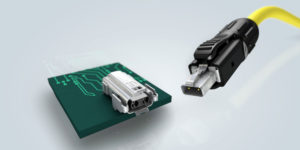
HARTING Americas announces launch of breakthrough Single Pair Ethernet technology
HARTING Americas announced their North American launch of their Single Pair Ethernet technologies. The company has been driving the creation
HARTING Americas announced their North American launch of their Single Pair Ethernet technologies. The company has been driving the creation
Qimarox has strengthened its collaboration with suppliers by implementing the Tradecloud Supply Chain platform. Through this platform, Qimarox communicates with
Panasonic i-PRO Sensing Solutions, formerly Panasonic Security Group, is announcing its new line of economically priced U-Series Network Cameras. Designed
Two major internet service providers are making changes to their home internet broadband plans and services as a result of
Tecsys Inc., an industry supply chain management software company, just announced that Delmar International Inc. has introduced operational and functional
Three years since introducing BluJay brand, the company continues growth streak, expands network and drives double-digit increase in bookings BluJay
The agreement deepens the existing relationship between the companies with the aim to provide complete rugged computing solutions for enhanced
JLT Mobile Computers Joins Ivanti Supply Chain Partner Program to Improve Worker Productivity JLT Mobile Computers, a supplier of reliable computers for
Partnership with the industry provider of mobile connection management solutions will improve mobile device performance, productivity and security JLT Mobile Computers,
ECCO Safety Group (ESG), a global manufacturer of safety solutions for public safety and commercial vehicles, announces the official market
Magazine readers select the best new products, and Seeq takes top honors in the Advanced Analytics for Process Manufacturing Data
Having grown faster than the market over the past seven years and delivering record revenues in 2019, the new JLT
U.S. manufacturing technology orders rose 24 percent in December from the previous month to $404 million, according to the latest
iTRACE Technologies, Inc., a provider of supply chain security applications for anti grey market and anti counterfeit, and Leuze, a
JLT Mobile Computers, a developer and manufacturer of reliable computers for demanding environments, announces the launch of an addition to
U.S. manufacturing technology orders fell 15 percent in November from the previous month to $320 million, according to the latest
Saudi Aramco Energy Ventures joins Altira Group, Chevron Technology Ventures, and existing investors to expand Seeq’s international and cloud-based businesses
The Raymond Corporation was named to Food Logistics’ 2019 FL100+ list, highlighting Top Software and Technology Providers. Raymond makes this year’s list for its expanded
Leveraging decades of product development and industry experience, JLT offers end-to-end rugged computer solutions, consultancy and problem solving for the
CES® 2020 opens today unveiling the next generation of innovation that will redefine industries, create jobs and solve many of society’s