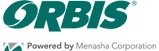
ORBIShield ECO™ receives Readers’ Choice Product of the Year 2024 Award
New eco-friendly dunnage product line provides protective packaging solutions while reducing environmental impacts. Modern Materials Handling, Material Handling Product News,
New eco-friendly dunnage product line provides protective packaging solutions while reducing environmental impacts. Modern Materials Handling, Material Handling Product News,
Kardex demonstrated to manufacturers at Automate 2024 the huge potential offered by Automated Storage and Retrieval System (ASRS) technology to
Latest rankings from GCCA also list company as 12th largest globally Vertical Cold Storage, a developer and operator of temperature-controlled distribution
The New Warehouse Podcast shines a spotlight on a crucial sector of cold chain logistics. Jamie Moriarty and Judd Rosenberg,
METTLER TOLEDO positions itself at the forefront of laboratory weighing when it comes to simplicity, performance, and robustness. With the
Creform Corporation, a manufacturer of unique products, has designed and built a picking cart for a healthcare services company that
Creform Corporation, a manufacturer of unique products for the design and building of material handling structures and AGVs, will showcase
New extended-height containers offer more capacity, higher efficiency, and recyclability ORBIS® Corporation, an international leader in reusable packaging, has announced
QUIET Platforms install PALLITE™ PIX™ storage solutions across their warehousing facilities PALLITE™, the award-winning international designer and manufacturer of high-density
Diversified Plastics, Inc., an international rotational molder based out of Latta, South Carolina, announces that their Business Development Manager, John
Strong Execution Drives Record Top and Bottom Line Results Reiterates Full Year Fiscal 2022 Revenue Outlook and Raises Earnings Outlook
The Plastics Industry Association (PLASTICS) and PLASTICS Recycling Committee will host a Recycling Open House© on August 30th, 2022, from 1:00
Apex Companies, headquartered in Oak Brook, IL, has announced that Engineered Handling, Inc, a storage and warehouse equipment supplier based
Treston, a supplier of smart, ergonomic industrial workstations and storage solutions, launches, as an industry first, wood-based bioplastic bins for
Diversified Plastic, Inc., an international rotational molder based out of Latta, South Carolina, introduces a new rotational molding oven to
Avoid a costly container mistake. Many don’t realize the heavy costs of making the wrong choices when it comes to
The Plastics Industry Association (PLASTICS) just announced shipments of primary plastics machinery (injection molding and extrusion) in North America decreased for
The company sponsors inaugural golf outing and community giving reception to benefit the local community ORBIS® Corporation, an international provider
The Canadian government continued its push this week to label plastic a “toxic” material, publishing an order-in-council in the Canada Gazette Part
Quantum Storage Systems, based in Miami, FL, has opened a new distribution center in the Portland, OR area. This new