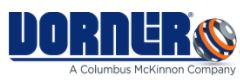
New compact curve conveyor from Dorner
Dorner has introduced the C3 Compact Curve Conveyor. This product excels in many applications, including- but not limited to confectionery,
Dorner has introduced the C3 Compact Curve Conveyor. This product excels in many applications, including- but not limited to confectionery,
Hapman highlights our Vacuum Conveyors, which are designed for efficient material movement across various industries. This line of conveyors showcases
Epax Systems, a supplier and installer of waste compaction systems, including stationary compactors, rolling compactors, vertical balers, and horizontal balers,
Robots in warehouses aren’t a novelty, but with the infusion of AI, they’re becoming integral players in operations. These intelligent
Robots in warehouses aren’t a novelty, but with the infusion of AI, they’re becoming integral players in operations. These intelligent
Hapman, a custom bulk material handling equipment, has highlighted our Vacuum Conveyors, designed for efficient material movement across various industries.
Pacline Conveyors has announced its participation in the highly anticipated ProMat 2025 trade show, taking place March 17-20 in Chicago,
Hapman has announced its Vacuum Conveyors, designed for efficient material movement across various industries. This line of conveyors showcases Hapman’s
ROYPOW has announced the launch of a new fully automated forklift battery module production line, further enhancing its manufacturing capabilities.
ALPS Inspection is the global industry-leading manufacturer of non-destructive, in-line leak inspection equipment for empty plastic containers of all sizes,
NORD Direct drive solutions offer an innovative alternative to traditional belt drives that deliver more outstanding performance, reliability, and lower
Wildeck, Inc., a manufacturer of industrial work platforms (mezzanines), vertical reciprocating conveyors (VRCs), rideable material lifts (RMLs), custom ladders, access
Multi-Conveyor designed and manufactured a series of independently powered plastic chain conveyors to transport single-lane products to a customer’s existing
Mallard Manufacturing, a provider of gravity flow solutions, has announced the appointment of Brian Meyer as National Accounts Manager. With
Garvey Corporation, Morrison Container Handling Solutions, and Garrido USA, and are excited to debut a new collaboration at PACK EXPO International this
Versatile solutions for diverse industry needs SupplyOne, Inc. spotlights its expansive range of packaging equipment and support services. These offerings
Add Rennco in booth S-3660 to your PACK EXPO 2024 itinerary to see how its vertical bagging solutions can add
Cyclonaire Corporation, a provider of pneumatic conveying solutions, announces the appointment of Jay Anzelmo as Vice President of Sales and
Mark Schmid has been appointed Regional Sales Manager, covering the upper Midwest portions of the U.S. for Dorner. Schmid will
Easily handles loads of up to 50,000 pounds or more PFlow Industries, the pioneer in vertical reciprocating conveyor (VRC) technology,