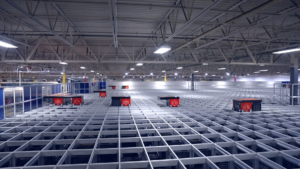
MAHLE aftermarket achieves milestone in Operational Efficiency with AutoStore empowered by Kardex
MAHLE Aftermarket turned to Kardex for an automated storage and retrieval solution following a shift in orders from large pallets
MAHLE Aftermarket turned to Kardex for an automated storage and retrieval solution following a shift in orders from large pallets
The patent-pending solution enhances order-picking speed and accuracy by easily segregating SKU lanes across multiple carton flow types Mallard Manufacturing,
The RNC has sourced a local Milwaukee-area manufacturer, Wildeck, Inc., to provide structural steel platforms supporting media team members and
Easily handles loads of up to 50,000 pounds or more in high-speed, high-cycle environments PFlow Industries, the pioneer in vertical
German Organic vegetable freezing company Westhof BIO has selected easily accessible, plug-and-play automation in the form of a stow Racking silo
PAC Machinery, a provider of packaging for more than 60 years, has introduced new bagger accessories and resources that make
Award dedicated to rewarding people-first culture excellence PFlow Industries, the pioneer in vertical reciprocating conveyor (VRC) technology, announces that it
NORDAC ON/ON+ variable frequency drives deliver intelligent control of conveyor systems with an integrated multi-protocol Ethernet interface to improve efficiency,
Dorner and its partner company montratec are set to unveil its latest innovations in assembly technology in booth 1224 at
Dorner and Garvey are well-established brands with decades of proven success. But now, they are combining their strengths to write
TrewSort sliding shoe sorter provides retail, e-commerce, and warehouse operations with high-capacity reliable throughput with the added benefits of AI-enabled
Trew showcases solutions and cooperation with TGW Logistics Trew, LLC, a North American manufacturer of warehouse automation solutions, is debuting
Visit Booth #B1019 to see how the Versatile VRCs Improve Efficiency and Worker Safety Join PFlow Industries, the founders of the
Comprised of the drive, motor, and gearbox, this new distributed drive system is available as a complete solution for motor-mounted
Flex-Line Automation, Inc., a family-owned business in southern Illinois, has been selected to feature on a national television program. For
MODEX 2024 booth #B6019, attendees will discover how Cimcorp’s automation helps grocery retailers, bakeries, and dairies improve speed, sanitation, and
ProVeyance Group will be exhibiting at MODEX 2024 from March 11th through March 14th at Georgia World Congress Center in
Kadant Inc. (KAI) announced it has completed the acquisition of KWS Manufacturing Company, Ltd. (KWS) for approximately $84 million in
Dorner has hired Dave Giffels as Business Development Manager. Giffels will be working with the sales team to grow Dorner’s
Dorner, a conveyor technology, has introduced the new DualMove Pallet System conveyor. This product excels in many applications, including –