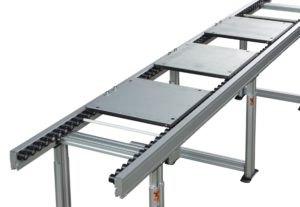
Dorner’s ERT250/150 Conveyor platforms power automation Applications at Automate 2022, June 6-9, in Detroit
Dorner is exhibiting its deep lineup of automation-focused conveyor platforms, including the Edge Roller Technology ERT®250 and ERT®150 models, in booth 4300