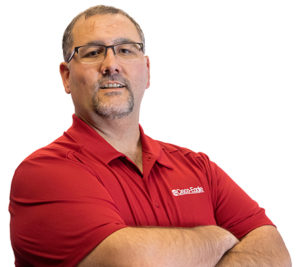
Cisco-Eagle has promoted Bryan Gauger to Vice President of Systems Integration
Cisco-Eagle has promoted Bryan Gauger to Vice President of Systems Integration according to Cisco-Eagle President Darein Gandall. Gauger brings decades
Cisco-Eagle has promoted Bryan Gauger to Vice President of Systems Integration according to Cisco-Eagle President Darein Gandall. Gauger brings decades
When thinking of a modern distribution center, most people will picture a conveyor and sortation system. And while they are
Based in Lancaster, Pa. for more than 45 years, Lumsden Corporation will remain a part of the Central Pennsylvania business
Dorner is never one to rest on its laurels, and that philosophy of constant improvement is shown in its newly
Wexxar Bel integrates its Flex E Pack system with Shuttleworth’s product delivery technology to create a fully functional packing cell
Wexxar Bel, a ProMach brand, is never one to rest on its laurels, and that philosophy of constant improvement is
With the BEUMER Group’s new location in Denver / Colorado, the system provider can better serve customers in the Airport
Huron Technology Corp. has just introduced the Ergo Conveyor, also known as the People Mover Conveyor, which is an ergonomic
The innovative design offers versatility to handle a wide range of item sizes typical of e-commerce fulfillment and parcel distribution
The award-winning products designed to fill the gap between induction and servo motors Bison Gear & Engineering Corp., a provider in the
Multi-Conveyor recently built a series of powered mild steel conveyors including a unique gravity conveyor to transport tall-shaped plastic products.
In this episode, I was joined by Jake Jakobson of Custom Industrial Products for the latest in our partnership with
Christy Valentine has joined Hytrol Conveyor Company, Inc. as the company’s Manager of Academic Partnerships. Valentine will run Hytrol’s Academic
Comprised of the drive, motor, and gearbox, this new distributed drive system is available as a complete solution for motor-mounted
No matter the size or type of material handling organization, safety is frequently a top consideration. How to keep employees
On this episode, I was joined by Avery Dennison’s Vice President of Identification Solutions, Ryan Yost. We discussed Avery Dennison’s
Utilizing enclosed pneumatic divert, combiners, dual lane merge, and more Multi-Conveyor recently built a series of mild steel constructed conveyors
Huron Technology Corp. has introduced the Flattening Belt Conveyor also known as the Bag Flattener Conveyor which is ideal for
Custom Industrial Products (CIP) has announced that their starting minimum wage will be $15 per hour, effective March 29th. CIP
Comprised of the drive, motor, and gearbox, this new distributed drive system is available as a complete solution for motor-mounted