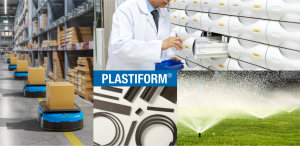
Arnold Magnetic Technologies highlights the PLASTIFORM® High Energy Flexible Magnets, Made in America
Arnold Magnetic Technologies Corporation (Arnold), a subsidiary of Compass Diversified and a global manufacturer of high-performance magnets and precision thin