Carbon® introduces RPU 130, its latest innovation in advanced materials
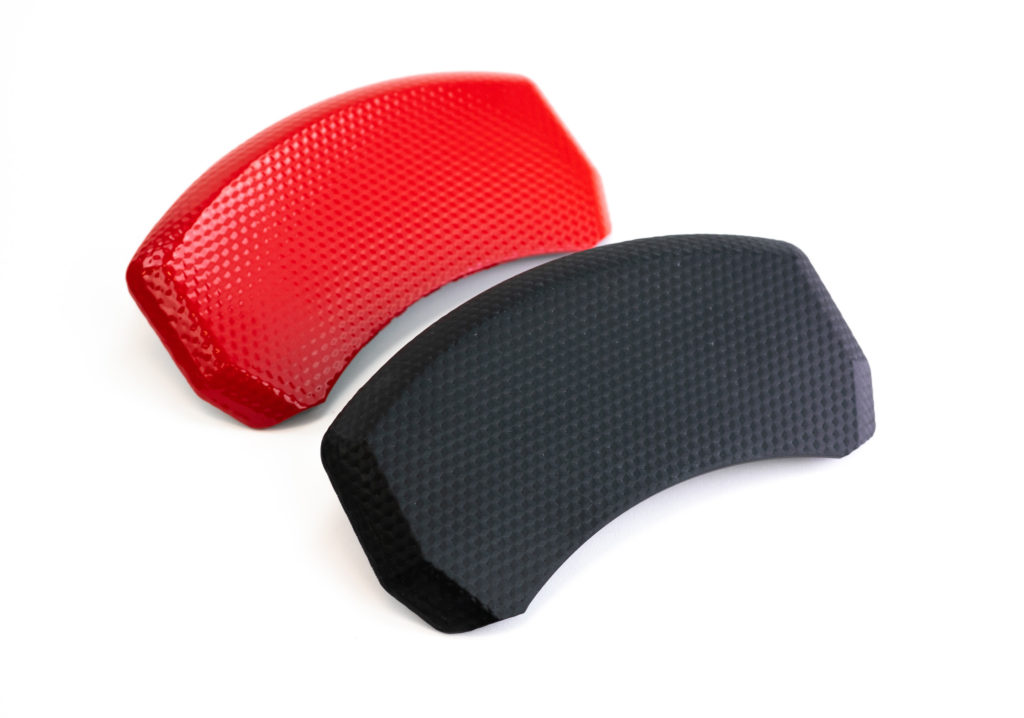
At K Trade Fair, Carbon debuts a groundbreaking new benchmark material, featuring Susterra® propanediol by DuPont Tate & Lyle Next week at the International K Trade Fair in Dusseldorf, digital manufacturing company Carbon will debut its latest innovation in materials, a new resin called RPU 130. With an unprecedented combination of properties, RPU 130 fills the need for a tough, rigid, and high temperature additive manufacturing material suitable for rigorous applications in industries such as automotive. RPU 130 is also partially derived from plants, addressing the growing demand for more sustainable, high-performance materials. Rigid polyurethane is Carbon’s most versatile rigid material family. Carbon developed RPU 130 to address the need for superior impact resistance and dimensional stability at elevated temperatures that no additive material could address. In addition to automotive, RPU 130 is highly relevant for a wide range of industrial and consumer product applications such as air ducts and brake caliper covers for vehicles, sunglasses, tool housings, and device enclosures. RPU 130 combines some of the best characteristics of Carbon’s RPU 70, FPU 50, and EPX 82 resins into a single, tough, heat and impact resistant material, similar to ABS, unfilled nylon, or polypropylene. “Our materials team at Carbon is second to none, and RPU 130 represents a true breakthrough in what is possible for new additive materials,” said Dr. Joseph DeSimone, Co-Founder and CEO of Carbon. “Although some of these properties have been available before in additive, RPU 130 is the first to combine them all into a single manufacturing material suitable for the most demanding conditions. We are really proud of the science that went into bringing this innovative material to market.” RPU 130 is the latest dual-cure engineering resin made exclusively for Carbon Digital Light Synthesis™ technology, at the heart of a new comprehensive solution. Its combination of performance attributes makes this new material wholly unique for additive manufacturing and more comparable to unfilled thermoplastics. Producing RPU 130 required innovations in not only material science, but also software and hardware. In addition to the new dual-cure resin, Carbon is offering a new heated C5 Cassette required for use with the material, a new dispensing solution, and tuning via software to ensure great end-use products. In addition to new hardware and software components, RPU 130 was made with environmentally sustainable raw materials. Carbon partnered with DuPont Tate & Lyle Bio Products to use Susterra® propanediol, a 100% bio-based building block that delivers high performance across a wide variety of polymers, coatings, and ink applications. Compared with conventional petroleum-based alternatives, Susterra® propanediol produces 48% less greenhouse gas emissions and uses 46% less nonrenewable energy from cradle-to-gate. Nearly 30% of RPU 130 is composed of this plant-based material. Going forward, Carbon is firmly committed to building on this work by continuing to expand efforts to achieve more sustainable practices through the use of advanced, high-performance, bio-based materials like Susterra® propanediol. “We are focused on ways to incorporate more sustainable approaches to developing materials, and our partnership with DuPont Tate & Lyle emphasizes that commitment. We believe that sustainability can go hand-in-hand with improved performance. In the case of RPU 130, we believe it will make the material even more appealing for our customers, as it makes it possible to create better quality products that are also ultimately better for the environment,” said Jason Rolland, SVP of Materials at Carbon. “With the launch of RPU 130, Carbon is upping the ante yet again by bringing high quality and top performing digital manufacturing to the industrial and automotive markets, and we are thrilled that Carbon chose Susterra® propanediol to help make this happen,” states Steve Hurff, VP of Marketing & Sales at DuPont Tate & Lyle Bio Products. “In addition, Susterra® propanediol, a USDA Certified 100% Bio-based product, enables a lower carbon footprint compared to petroleum-derived materials, making it a win-win for consumers.” Carbon RPU 130 is available via Carbon’s resin store starting today in the USA, Canada, and Europe. To learn more about RPU 130, please stop by Carbon’s booth at K-Show from October 16-23 located at H7.2, F12.
Wilmington Machinery announces the promotion of Jim Boos to Sales and Marketing Manager
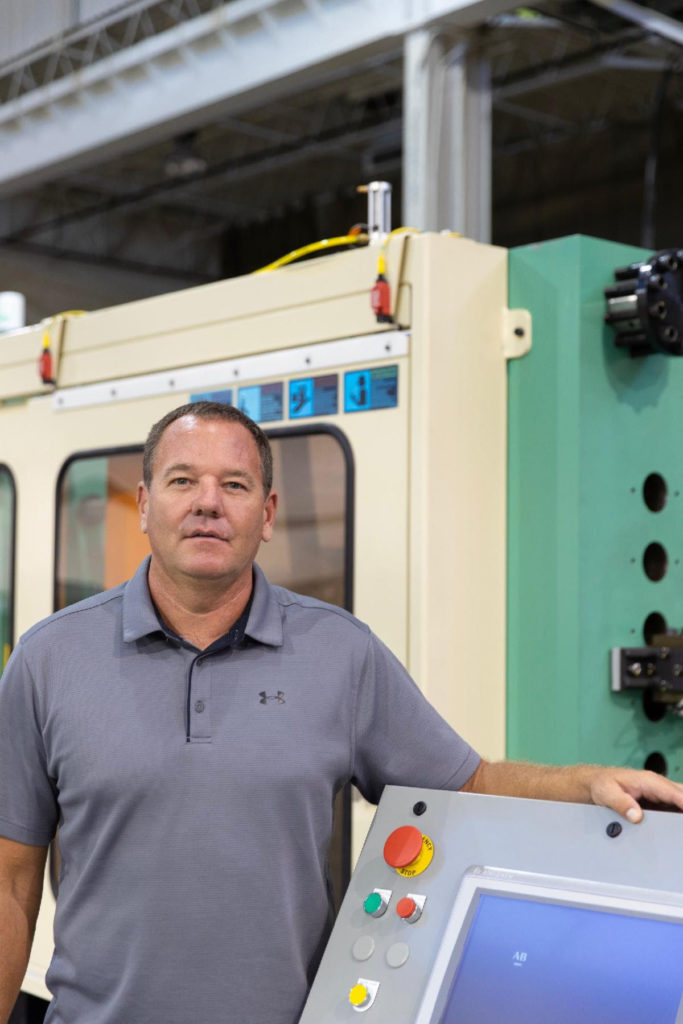
Wilmington Machinery has announced the promotion of Jim Boos to the position of Sales and Marketing Manager. Boos previously held the position of Operations Manager at Wilmington Machinery. Before joining Wilmington Machinery, Boos gained valuable experience in quality and project management with other manufacturers. “In his operations role, Jim developed a vast knowledge of Wilmington Machinery’s structural foam injection molding and rotary blow molding machines. His operations expertise provides the foundation to properly assist our customers on determining the best Wilmington machine to meet their application,” noted Wilmington Machinery President Russ La Belle. La Belle is excited for Boos as he contributes to Wilmington Machinery’s growth in his new role as leader of Wilmington’s sales and marketing team. Since its founding in 1972, Wilmington Machinery has been building high performance, low-pressure structural foam molding machines. In addition, the company has built custom extrusion, thermoforming, and industrial blow molding machinery, along with a primary line of high capacity rotary blow molding systems for polyolefin monolayer/ multilayer barrier blow molded packaging. From a modern 65,000 SF facility in Wilmington, North Carolina, the company can easily meet any customer’s need for extra-large plastics machinery. International shipments can also be arranged through the nearby deep-water Port of Wilmington.
Cornerstone Specialty Wood Products announces new Engineering Manager
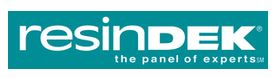
Cornerstone Specialty Wood Products, manufacturer of ResinDek industrial engineered flooring panels for industrial work platforms at warehouses and fulfillment centers, is proud to announce and welcome Kevin Cook to their team as Engineering Manager. In this role, Mr. Cook will be responsible for leading the engineering and estimating team, new product development and oversight for Cornerstone’s internal testing laboratory. Mr. Cook brings more than a decade of experience to Cornerstone Specialty Wood Products (CSWP) team as a Design Engineer and Project Manager. Prior to coming to CSWP, he was a Senior Engineer with Vanderlande Inc., where he worked on medium to large complex material handling projects. He earned his Bachelor of Science degree in Engineering Technology from Central State University, Wilberforce, Ohio. “I am truly looking forward to be a part of the of CSWP’s team. When I first saw the internal testing laboratory and learned how the company goes to great lengths to solve flooring challenges for their customers, I knew instinctively that that this is where I am supposed to be. I am excited to contribute to the growth of CSWP and look forward to helping solve flooring issues for Warehouse Fulfillment Centers and other applications,” stated Kevin Cook. “Kevin brings a wealth of knowledge and experience with him and I am confident he will utilize his design expertise, project management skills, and results driven leadership style to further the growth of Cornerstone Specialty Wood Products,” said President Greg Doppler.
Myers Industries announces resignation of CEO, names interim CEO
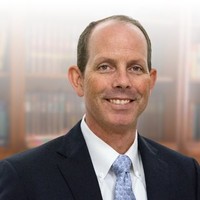
Myers Industries, Inc., an international manufacturer of polymer products for industrial, agricultural, automotive, commercial and consumer markets, today announced that Dave Banyard has resigned as President and Chief Executive Officer, effective October 25, 2019, to accept another professional opportunity. Andrean Horton, the Company’s Executive Vice President, Chief Legal Officer and Secretary, has been named Interim President and Chief Executive Officer. The Board of Directors will engage a global executive search firm to assist in identifying a new President and Chief Executive Officer. Chairman of the Board of Directors of Myers Industries F. Jack Liebau, Jr. commented, “On behalf of the Board of Directors, we would like to thank Dave for his leadership and contributions to Myers. We wish him well in his future endeavors. The Company will remain focused on executing its strategic initiatives, including the transformation underway in the Distribution Segment.”
Pennsylvania metal fabricator hosts Manufacturing Day tours for general public
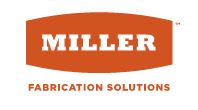
Offering Free Demonstrations of New Equipment, Job Fair and VR Simulation Miller Fabrication Solutions, a strategic metal fabrication partner for original equipment manufacturers (OEMs) across construction, mining, material handling and conveying equipment and other heavy industries, will offer free plant tours to the general public as part of its involvement in the national Manufacturing Day℠ celebration on Friday, October 4. Tours will run every 30 minutes from 8:00 a.m. to 3:00 p.m. EDT at its two Brookville, Pa. locations, Sandy Lick and Maplevale. Guests will be able to watch demonstrations of the fabrication of large metal parts, including robotic and manual welding, machining, painting, and mechanical assembly services. The company’s latest equipment additions, a pair of DMG Mori’s CMX 1100 V machines, will also be on display. Installed in June, the CMX 1100 V gives Miller Fabrication Solutions even greater part production capabilities at its Maplevale location, as it is equipped with over 200 options for workpiece handling, monitoring, measurement and machining. The Manufacturing Day activities at Miller will include a job fair for recent and future graduates and skilled workers, as well as an Oculus Virtual Reality (VR) simulation of Miller’s Sandy Lick headquarters. Miller Fabrication Solutions, formerly known as Miller Welding & Machine, employs approximately 400 people throughout the Western Pennsylvania region. The company ranks within the top 10 employers in Jefferson county and was named among the country’s top fabricators in The Fabricator magazine’s 2019 FAB 40 list [The Fabricator magazine’s 2019 FAB 40 list __title__ The Fabricator magazine’s 2019 FAB 40 list]. Manufacturing Day is an annual celebration of modern manufacturing meant to inspire the next generation of manufacturers. Started in 2012 and sponsored by the National Association of Manufacturers, the celebration invites members of the community across the country — including students, educators, business people, media, and politicians — to manufacturing facilities in a collective effort to educate visitors about manufacturing career opportunities and improve public awareness of the profession. Register for a tour at one or both of Miller’s Brookville facilities by visiting https://www.millerfabricationsolutions.com/event/mfg-day-2019/ today.
Venture Plastics celebrate their 50th anniversary
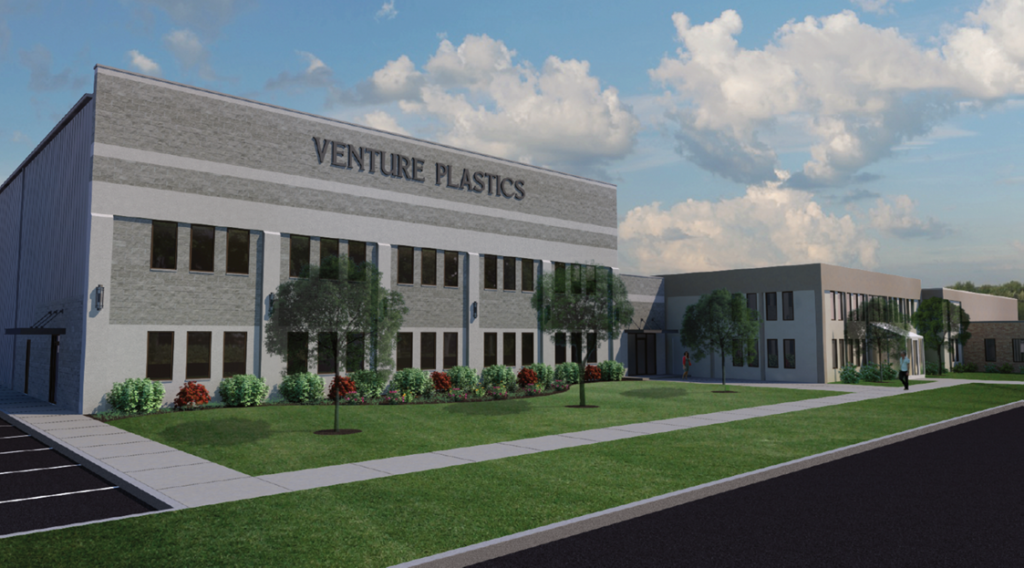
Kenneth M. Groff founded Venture Plastics Inc. in October of 1969 in a small plant in Warren, Ohio. Today, Venture Plastics celebrated 50 years of continuous business with an open house for customers, suppliers and various members of the local community. Founder Ken Groff was presented the Key to the City by the Mayor of Newton Falls while many of his long-time employees participated in the event. “It continues to amaze me that I am an owner of a successful custom injection molding company that has thrived for 50 years,” stated Ken Groff. “I got my start in the late 1950s in the estimating department of a producer of rubber and plastic parts. In 1969, I had the opportunity to launch a company to mold a clothes steamer for a specific customer and I jumped for it. However, this project was full of challenges that almost closed our company for good. Luckily, I found a way out and swore I would never let my company become dependent on a single project ever again. I know this is the biggest reason we are standing in this first-rate plastics molding plant today 50 years later.” Groff said he believes his company has survived by ensuring the company lives by these five simple rules: Never, ever, be satisfied with where you are or what you’ve achieved Take advantage of opportunities and problems Be fair and honest to earn the trust of your employees and customers Never stop looking for ways to separate yourself from competitors Choose your customers wisely Today, Venture Plastics operates a Newton Falls plant comprised of a total of 92,000 square feet across three facilities, with 50,000 square feet dedicated to molding, 25,000 square feet for warehousing and the rest for engineering. There is also a 60,000 square foot molding operation in El Paso, Texas. Both ISO-IATF 16949 facilities contain a wide range of injection molding machines ranging from 55 tons to 1,440 tons. They serve a diversified customer base in the industrial-consumer, appliance, truck-agriculture, automotive, fuel delivery and communications industries. In addition, the company provides customers with many secondary value-add services such as engineering and project management support, over-molding, insert molding, decorating, plating, assembly, welding, plus expertise in a wide variety of engineered grade materials.
U.S. Cutting Tool year to date consumption up 2.6 percent in July
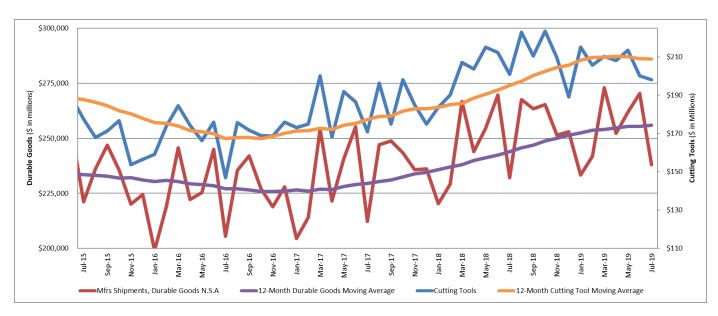
U.S. cutting tool consumption totaled $198.4 million according to the U.S. Cutting Tool Institute (USCTI) and AMT – The Association For Manufacturing Technology. This total, as reported by companies participating in the Cutting Tool Market Report collaboration, was down 0.6 percent from June’s $199.7 million and down 1.3 percent when compared with the $201.0 million reported for July 2018. With a year to-date total of $1.5 billion, 2019 is up 2.6 percent when compared with 2018. These numbers and all data in this report are based on the totals reported by the companies participating in the CTMR program. The totals here represent the majority of the U.S. market for cutting tools. According to Brad Lawton, Chairman of AMT’s Cutting Tool Product Group, “While orders for production machines are down 12 percent, cutting tool shipments are still holding up in comparison to 2018 figures. The impending downturn in investment is expected to be short and shallow but it is still likely to yield a couple of tough quarters for cutting tool manufacturers.” “As expected based on trends in the Gardner Business Index, cutting tool orders continued to contract on a month-over-month basis in July. Year-over-year, cutting tool orders will likely start contracting in the fourth quarter of 2019. However, the likely contraction does not appear to be anything out of the ordinary for the industry. My current expectation is that the International Manufacturing Technology Show (IMTS)*, as it typically does, will mark the bottom of this downturn and orders will improve from there,” said Steve Kline Jr., Chief Data Officer at Gardner Business Media. “The Purchasing Managers’ Index dip below 50 in July suggests that the year over year growth in cutting tools is likely to turn negative when August shipment levels are published. Still, some industries demand for cutting tools continues to expand as cautiousness shifted production downstream deeper into the supply chain or into contract machine shops,” said Dave Burns, President of Global Business Advisory Services, LLC.. The Cutting Tool Market Report is jointly compiled by AMT and USCTI, two trade associations representing the development, production and distribution of cutting tool technology and products. It provides a monthly statement on U.S. manufacturers’ consumption of the primary consumable in the manufacturing process – the cutting tool. Analysis of cutting tool consumption is a leading indicator of both upturns and downturns in U.S. manufacturing activity, as it is a true measure of actual production levels. Historical data for the Cutting Tool Market Report is available dating back to January 2012. This collaboration of AMT and USCTI is the first step in the two associations working together to promote and support U.S.-based manufacturers of cutting tool technology. The graph below includes the 12-month moving average for the durable goods shipments and cutting tool orders. These values are calculated by taking the average of the most recent 12 months and plotting them over time.