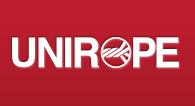
Unirope becomes first AWRF accredited member
Unirope Limited was the first rigging shop to become an Associated Wire Rope Fabricators (AWRF) accredited member. Unirope completed a
Unirope Limited was the first rigging shop to become an Associated Wire Rope Fabricators (AWRF) accredited member. Unirope completed a
New Age Industrial has announced the promotion of Scott Schrum to Assistant National Sales Manager of the Material Handling Division.
Fourth quarter and full year 2023 diluted EPS of $3.16 and $18.00, respectively. Fourth quarter and full year 2023 net earnings before noncontrolling
The system enables pre-pack manufacturing testing of battery cells and battery cell performance data storage capabilities McAlister Design & Automation,
ProVeyance Group will be exhibiting at MODEX 2024 from March 11th through March 14th at Georgia World Congress Center in
New Age Industrial has announced the appointment of Scott Schrum for outside sales in the Material Handling Division. Scott is
The soft landing the U.S. economy generally experienced through 2023 did not affect all sectors of the economy evenly. Even
The Plastics Industry Association (PLASTICS) has opened nominations for the William R. Carteaux Leadership Award, presented to an industry professional
Nucor Corporation announced that the company’s Board of Directors approved $280 million to modernize its steel plate mill in Tuscaloosa,
Kinetic Technologies, an innovator of positioners, fixtures, and tooling for industrial automation cells, has announced the launch of their newest
The Plastics Industry Association (PLASTICS) announced its strong opposition and disappointment in the Break Free from Plastic Pollution Act of 2023, as
Nucor Corporation launched “Made for Good,” a campaign highlighting the company’s more than five decades of producing steel using the cleanest
June 2023 U.S. cutting tool consumption totaled $217.3 million, according to the U.S. Cutting Tool Institute (USCTI) and AMT –
AR Iron has become one of the only companies in the western US to pass the rigorous testing set forth
Nucor Corporation announced its Board of Directors elected Nicholas C. Gangestad as a director effective September 1, 2023. Mr. Gangestad,
Platinum Tooling, the exclusive importer of Heimatec live tools and angle heads plus other global brands of precision machine tool
April 2023 U.S. cutting tool consumption totaled $190.0 million, according to the U.S. Cutting Tool Institute (USCTI) and AMT –
Nucor Corporation today announced guidance for its second quarter ending July 1, 2023. Nucor expects second quarter earnings to be
Nucor Corporation announced today that it will reorganize the Company’s plate group, including ceasing production at Nucor Steel Longview, LLC.
Net earnings attributable to Nucor stockholders of $1.14 billion, or $4.45 per diluted share Net sales of $8.71 billion Net earnings before noncontrolling interests of $1.23 billion;