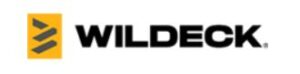
Wildeck unveils new modern logo as part of company rebrand
One of the largest U.S. manufacturers of industrial steel work platforms (mezzanines), material lifts, safety guarding, and access products has
One of the largest U.S. manufacturers of industrial steel work platforms (mezzanines), material lifts, safety guarding, and access products has
TAB Wrapper Tornado allows Penn sheet metal to wrap long pallet loads fast Metal fabrication company Penn Sheet Metal, Allentown,
Nucor reports the safest and most profitable year in Company history, eclipsing prior records set in 2021 Fourth quarter and
The new machine improves product quality and increases production capacity Bison Gear & Engineering Corp., a provider in the power
TerraSource Global, a manufacturer of high-quality material sizing equipment based on the Gundlach, Jeffrey Rader, and Pennsylvania Crusher brands, and
The U.S. plastics industry continued to grow in 2022 against the backdrop of weaker domestic and global economic growth. Data
Nucor Corporation announced that California Steel Industries, Inc. (CSI) will build a continuous galvanizing line at its mill in Fontana,
October 2022 U.S. cutting tool consumption totaled $200.6 million, according to the U.S. Cutting Tool Institute (USCTI) and AMT –
Nucor Corporation announced today that Noah Hanners will be promoted to Executive Vice President effective January 1, 2023. Mr. Hanners began his
New Crosby Balanced Diaphragm and Bellows leak detection pressure relief valve solutions improve performance, safety, and reliability while reducing emissions
New orders of manufacturing technology totaled $457.7 million in October 2022, according to the latest U.S. Manufacturing Technology Orders Report
Nucor Corporation has announced that it has made an equity investment in Electra, a Colorado-based start-up developing a process to
The acquisition is Millwood’s second Waverly, OH location Millwood, Inc. acquired its second location in Southern Ohio and 35th location
Say hello to ChIP, Custom Industrial Product’s newest addition to its family! ChIP acts as the brand ambassador for Custom
Diversified Plastics, Inc., an international rotational molder based out of Latta, South Carolina, announces that their Business Development Manager, John
The shipments of primary plastics machinery (injection molding and extrusion) in North America slowed in the third quarter according to
Developing homegrown leaders is one of the most important things companies can do to pave the way for continued success.
Orbital wrapping machine manufacturer TAB Industries, LLC, Reading, Pa.has increased the amount of component parts that are “Made in USA”
The Plastics Industry Association (PLASTICS) released its annual Global Trends report today during an executive briefing at the K Show in Düsseldorf,
Bally Ribbon Mills (BRM), an industry provider in the design, development, and manufacture of highly specialized engineered woven fabrics, says