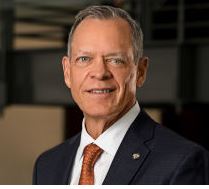
Nucor Chief Financial Officer Jim Frias to retire; Steve Laxton to be promoted
Nucor Corporation has announced that Jim Frias, Chief Financial Officer, Treasurer, and Executive Vice President, plans to retire effective June
Nucor Corporation has announced that Jim Frias, Chief Financial Officer, Treasurer, and Executive Vice President, plans to retire effective June
Civan’s OPA 6 Weld, an entirely new class of laser that modulates beam shape at MHz rates without any moving
Nucor Corporation announced today that it has successfully completed its acquisition of a majority ownership position in California Steel Industries,
The Plastics Industry Association (PLASTICS) has promoted Patrick Krieger, Senior Director for Materials & Sustainability, to the newly created role
Hyster Company announces an expansion of the certified Explosion Proof (EX) lift truck line, in which traditional Hyster lift trucks
As global trade slowed in 2020, the US plastics industry experienced its first trade deficit after many years of a
The Plastics Industry Association (PLASTICS) just announced that shipments of primary plastics machinery (injection molding and extrusion) in North America
In a world where machine shops are struggling to stay open and maintain their business and in a day when
Global Shop Solutions, a developer of ERP software for manufacturers around the world, has named John Davis as Chief Technology
Thomson Industries, Inc., a manufacturer of linear motion control solutions, is celebrating the 50th anniversary of its legacy Ball Screws
There’s a lot buried in the multitrillion-dollar social spending package currently moving through Congress. One provision under consideration that has
The Plastics Industry Association (PLASTICS) released the following statement from president and CEO Tony Radoszewski in reaction to the passing of Jay Gardiner.
The Plastics Industry Association (PLASTICS) recently issued its 2021 Global Trend Report. This PLASTICS’ flagship publication takes a deep dive into
Nucor Corporation has announced two acquisitions today on behalf of The David J. Joseph Company (DJJ). The addition of these
The Plastics Industry Association (PLASTICS) just announced shipments of primary plastics machinery (injection molding and extrusion) in North America decreased for
The annual list recognizes the nation’s most successful metal fabricating operations Miller Fabrication Solutions, a strategic metal fabrication partner for
The acquisition further expands and strengthens Myers’ rotational molding platform Provides Myers’ customers access to a more complete portfolio of
Today, the Plastics Industry Association (PLASTICS), the only industry group with membership throughout the entire plastics supply chain, announced its Plastics
Nucor Corporation announced today that it has entered into an agreement to purchase Hannibal Industries, Inc. for $370 million, which
Diversified Product Development, marketer of the LineWise™, LiftWise™, RailWise™ and DesignWise™ brands, hosted a grand opening ceremony on June 22, 2021, at