Globe Composite Solutions
Gauer Metal Products, Inc
GAGE Industries, Inc.
JG Steel
Vulcan Manufacturing
Vulcan Springs and manufacturing
Walls + Forms, Inc.
Vertical Systems International
eMachineShop
Easyfit, Inc.
GROB Systems Apprenticeship celebrates 30th Year
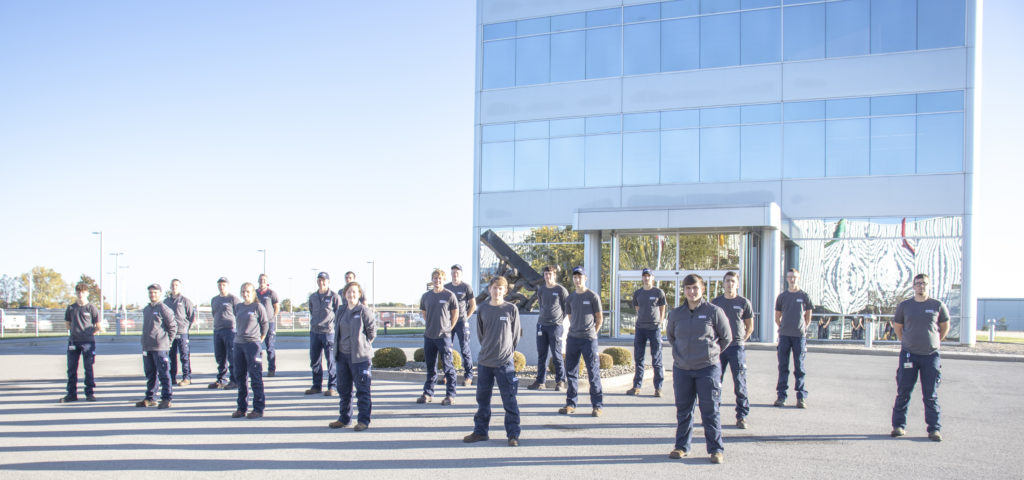
GROB Systems, a global provider in the development of manufacturing systems and machine tools, celebrates the 30th anniversary of its highly successful apprenticeship program. The program offers technical training and soft skills to prepare apprentices to be both highly-skilled technicians and well-rounded employees. It also includes electrical training in how to read electrical diagrams, wire control cabinets, troubleshoots machine faults, and program PLCs. In its 30 years, GROB has hired and trained over 380 apprentices. These trained apprentices now work across the company making an impact everywhere from machine and panel shops, to sub-assembly, debug, final assembly, and even to the engineering, marketing, and sales & proposals departments. Almost 40% of GROB’s current workforce in Bluffton is made up of past and current apprentices and currently includes one C-level, two Managers, 10 Supervisors, and 11 Foreman across various departments. Mike Meyer was a member of the inaugural class of 1990 and is now a Project Leader in GROB’s Mechanical Engineering department. “The people of GROB are really the best part. Starting with local people in Bluffton and the surrounding areas in Ohio, then all of the international people we get a chance to work with, for me this is far and away from the best part of GROB,” says Meyer.
Passive transfers facilitate multiple side case printing
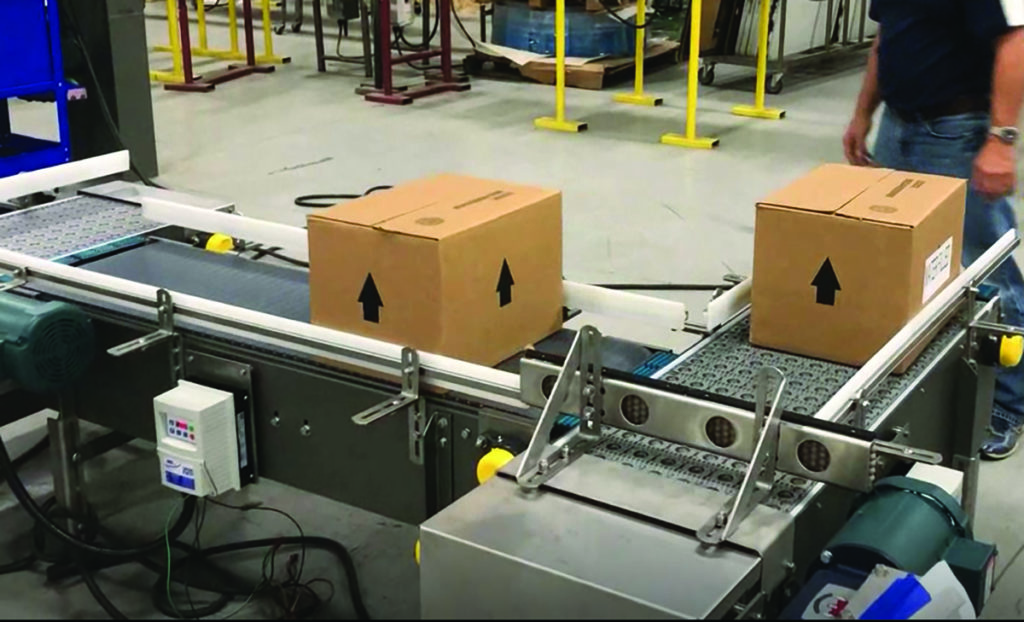
Without elaborate pneumatics or controls and NO pinch points Multi-Conveyor recently built three mild-steel constructed conveyors that passive off transfer from narrow to wide side leading (and back) to facilitate multiple side case printing. The cases start narrow side leading then transfer 90 degrees to wide side leading without using pneumatic pushers or elaborate devices. Precise conveyor placement and ARB roller belt technology transfer the now wide side leading cases onto a straight running flat top plastic belted conveyor where the customer can integrate their label printer(s). A second passive transfer then transfers the cases back to the narrow side leading to position them for transfer onto the customer’s existing check-weigher. The 90° “passive” transfer technology is based on proprietary integrated roller belting and bead rails to achieve the movement. Multi-Conveyor uses a variety of belt technology to ensure accurate product orientation. True passive transfers do not require pneumatics or controls – which means easy operation without pinch points, minimizing safety issues for the Operator. See even more product orienting videos – from simple to elaborate configurations – in their extensive product video gallery.
July 2020 U.S. Cutting Tool Orders down 8.5% from June 2020
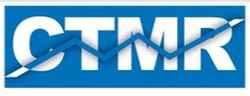
July 2020 U.S. cutting tool consumption totaled $137.8 million, according to the U.S. Cutting Tool Institute (USCTI) and AMT – The Association For Manufacturing Technology. This total, as reported by companies participating in the Cutting Tool Market Report collaboration, was down 8.5 percent from June’s $150.6 million and down 30.6 percent when compared with the $198.5 million reported for July 2019. With a year-to-date total of $1.1 billion, 2020 is down 21.2 percent when compared with July 2019. These numbers and all data in this report are based on the totals reported by the companies participating in the CTMR program. The totals here represent the majority of the U.S. market for cutting tools. According to Brad Lawton, Chairman of AMT’s Cutting Tool Product Group, “The July data shows a slight decline as the cutting tool industry’s major customers have returned to work from the pandemic shutdown. This is likely due to customers seeking to deplete existing tool inventories and adjust to the uncertainty of domestic and global markets before placing new orders. It is clear that the climb to better sales volumes will be extended and bumpy.” “Given the ongoing disruption to the U.S. economy as a result of the COVID-19 pandemic, it’s not surprising that U.S. manufacturing technology orders continue to be battered, with monthly totals for April through July down compared with the total for December 2019,” said Alan Richter, editor-at-large for Cutting Tool Engineering, adding that December typically has the lowest total of any year. “The necessary canceling of major events that generate significant machine tool sales, such as IMTS, only added to the downturn.” The Cutting Tool Market Report is jointly compiled by AMT and USCTI, two trade associations representing the development, production, and distribution of cutting tool technology and products. It provides a monthly statement on U.S. manufacturers’ consumption of the primary consumable in the manufacturing process – the cutting tool. Analysis of cutting tool consumption is a leading indicator of both upturns and downturns in U.S. manufacturing activity, as it is a true measure of actual production levels. Historical data for the Cutting Tool Market Report is available dating back to January 2012. This collaboration of AMT and USCTI is the first step in the two associations working together to promote and support U.S.-based manufacturers of cutting tool technology. The graph below includes the 12-month moving average for the durable goods shipments and cutting tool orders. These values are calculated by taking the average of the most recent 12 months and plotting them over time.
Adjustable levers for lifting, swinging and latching available at JW Winco

Adjustable levers are definitely among the most important standard parts for clamping and fixing in place. They are found in all kinds of applications, and the JW Winco portfolio is correspondingly diverse – now even more so with new, more versatile models. For over 40 years, JW Winco has had the standard for all adjustable levers in its selection. The GN 300 is a timeless yet modern standard part that can be used in almost any context. And, it is the basis for a hand lever family that has been successively expanded by JW Winco, with variations for specific applications or with special dimensions and additional functions. An enlarged circular clamping surface can also be found in the GN 300.4. It integrates an axial ball bearing into the washer, which reduces friction during tightening – and allows a doubling of the clamping force. If specially-tipped studs are needed, try the GN 306 – it offers brass- or plastic-tipped studs, hardened tips, ball pins, or circular thrust points to gently distribute the force. The Stainless Steel variants GN 300.5 (matt shot-blasted) and GN 300.6 (electropolished) are intended for applications in corrosive environments. In particular, the special geometry and external hexagon retaining screw make it less susceptible to soiling or standing liquids. Meanwhile, the GN 305 in Hygienic Design is certified by DGUV Test to meet high hygiene standards. It combines zero dead space with a solid Stainless Steel handle and a hygienic seal between the threaded stud and the disengageable handle body as well as against the contact surface. The original model GN 300 has also been further optimized. It is now available with a markedly shorter handle that reduces space requirements with a length of 0.87 inches (22 millimeters) and limits the applied torque during tightening – this variant is intended especially for light applications, such as with M3 and M4 threads. The GN 300 zinc die-cast handle is available in a variety of coating colors. The bushing and retaining screw are made of non-rusting stainless steel in variant GN 300.1, while GN 300.2 features zinc plated and blue passivated steel – all state of the art, as always from JW Winco. More information can be found at www.jwwinco.com.
June 2020 U.S. Cutting Tool orders up 10.1% from May 2020
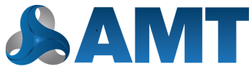
June 2020 U.S. cutting tool consumption totaled $150.6 million, according to the U.S. Cutting Tool Institute (USCTI) and AMT – The Association For Manufacturing Technology. This total, as reported by companies participating in the Cutting Tool Market Report collaboration, was up 10.1 percent from May’s $136.8 million and down 24.6 percent when compared with the $199.7 million reported for June 2019. With a year-to-date total of $1 billion, 2020 is down 19.7 percent when compared with June 2019. These numbers and all data in this report are based on the totals reported by the companies participating in the CTMR program. The totals here represent the majority of the U.S. market for cutting tools. According to Bret Tayne, President of USCTI, “Consistent with recent reports on other industrial activity, the cutting tool industry rebounded somewhat in June. We still have a long way to go to return to activity levels that preceded the pandemic shutdown, but we appear to be headed in the right direction.” Costikyan Jarvis, President of Jarvis Cutting Tools, added the following: The June figures of the Cutting Tool Market Report provide some hope that the worst of the contraction is behind us. With all the challenges that we faced, having a June number that is both a 10% improvement over May and a 5% improvement over April is a good sign. We should also take comfort that some of the initial July indicators show continued growth. The July PMI showed an expansion number of 54.2, the unemployment rate showed a further reduction, and the latest estimate of the Atlanta Fed’s GDPNow is a 20.5% growth. In this recession, both automotive and commercial aerospace industries, the two largest users of cutting tools, stopped producing for many weeks. In previous recessions, production has never gone down to zero; the implications of this are not yet understood. These industries have supply chains that are international and complex, and it is unclear if their supply chains have fully recovered. In addition to a drop in demand, customers are also talking about seeing significant de-inventorying in the supply chain. It will take several more months for everyone to understand both the shape of the recovery and how these industries adjust to the post-COVID world. The Cutting Tool Market Report is jointly compiled by AMT and USCTI, two trade associations representing the development, production, and distribution of cutting tool technology and products. It provides a monthly statement on U.S. manufacturers’ consumption of the primary consumable in the manufacturing process – the cutting tool. Analysis of cutting tool consumption is a leading indicator of both upturns and downturns in U.S. manufacturing activity, as it is a true measure of actual production levels. Historical data for the Cutting Tool Market Report is available dating back to January 2012. This collaboration of AMT and USCTI is the first step in the two associations working together to promote and support U.S.-based manufacturers of cutting tool technology. The graph below includes the 12-month moving average for the durable goods shipments and cutting tool orders. These values are calculated by taking the average of the most recent 12 months and plotting them over time.
Emerson´s new Aluminum Cylinder boosts machine speeds and cuts downtime
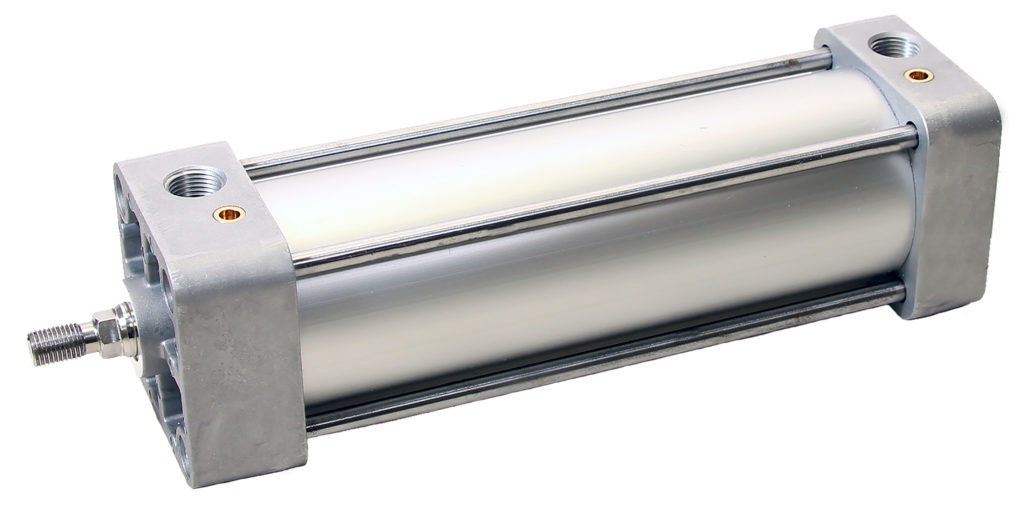
New AVENTICS™ TM5 TaskMaster™ aluminum cylinder increases reliability and productivity, reduces vibration and noise, while being cost-effective Machine builders and their end-user manufacturers can increase machine speeds and reliability with the new AVENTICS™ TM5 TaskMaster™ aluminum cylinder from Emerson. The National Fluid Power Association (NFPA)-compatible pneumatic cylinder reduces cost, energy consumption, equipment wear, and downtime. With its rugged aluminum body construction and a steel piston rod, the TM5 TaskMaster features Emerson´s state-of-the-art pneumatic cushioning technology that allows an ideal cushion adjustment to slow down the piston to a stop by the time it reaches the endcap. Ideal cushioning reduces the time it takes the cylinder to complete a stroke, allowing an improvement in efficiency that significantly boosts machine speed and lowers endcap hammer. Ideal cushioning also reduces cycle time and enables the TM5 cylinders to carry higher loads without sacrificing cylinder performance. The cylinder incurs less stress and there is no end-of-stroke bounce or end-cap slamming, which is the main source of cylinder wear, slowness, and noise. Ideal cushioning thus lengthens cylinder operating life and reduces downtime related to cylinder failure. Additionally, it reduces machine noise and vibration while reducing energy consumption. »The all-new TM5 TaskMaster gives machine builders and end-user manufacturers the tools to make their machines faster and more reliable,» said James Ward, vice president engineering, machine automation, Americas, at Emerson. »It´s the highest performing and most reliable TaskMaster cylinder ever produced, so it gives them an opportunity to build a competitive advantage.» The NPFA-compliant TM5 is the latest addition to the TaskMaster line of aluminum cylinders, an industry standard for 50 years. The TM5 TaskMaster is supported by a full suite of web-based design and integration tools, with many products preconfigured and ready to order. With no additional engineering time for setup, Emerson´s online configurator provides a product part number, pricing, and 2D and 3D CAD drawings in one convenient place. In addition, all product information and spare parts can be found in the AVENTICS Pneumatics Shop. TaskMaster TM5 provides a high-quality and readily available interchange cylinder to meet OEM and machine requirements. In combination with the online tools, a fast-delivery program allows for quick turnaround of orders, reducing lead times for customers. From configuration to production, Emerson´s process is completely automated.
April 2020 U.S. Cutting Tool orders down 14.4% from April 2019
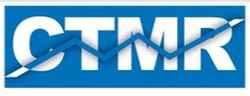
April 2020 U.S. cutting tool consumption totaled $142.9 million, according to the U.S. Cutting Tool Institute (USCTI) and AMT – The Association For Manufacturing Technology. This total, as reported by companies participating in the Cutting Tool Market Report collaboration, was down 24.7 percent from March’s $189.8 million and down 31.1 percent when compared with the $207.5 million reported for April 2019. With a year-to-date total of $717.5 million, 2020 is down 14.4 percent when compared with April 2019. These numbers and all data in this report are based on the totals reported by the companies participating in the CTMR program. The totals here represent the majority of the U.S. market for cutting tools. According to Bret Tayne, President of USCTI, “The precipitous drop in April cutting tool industry sales numbers confirms what many of us have experienced. The good news is that some economic forecasts and macro market indicators point to improvement as we enter the second half of the year.” “The latest data from April simply quantifies ‘how bad’ the news is for our industry. It also appears the bad news will continue through the months ahead. The drop in oil prices along with COVID-19’s impact on automotive, aerospace and support industries has left its trail of destruction,” said Steve Stokey, Executive VP and Owner of Allied Machine and Engineering, adding, “Survival and understanding the ‘new normal’ is what is driving most decisions nowadays. One positive tidbit to note is the resiliency of our industry. Companies have implemented changes and innovated at unprecedented speeds. The phrase ‘Innovate or Die’ has never been more relevant than it is today.” The Cutting Tool Market Report is jointly compiled by AMT and USCTI, two trade associations representing the development, production, and distribution of cutting tool technology and products. It provides a monthly statement on U.S. manufacturers’ consumption of the primary consumable in the manufacturing process – the cutting tool. Analysis of cutting tool consumption is a leading indicator of both upturns and downturns in U.S. manufacturing activity, as it is a true measure of actual production levels. Historical data for the Cutting Tool Market Report is available dating back to January 2012. This collaboration of AMT and USCTI is the first step in the two associations working together to promote and support U.S.-based manufacturers of cutting tool technology. The graph below includes the 12-month moving average for the durable goods shipments and cutting tool orders. These values are calculated by taking the average of the most recent 12 months and plotting them over time.
U.S. Manufacturing Technology orders decreased in April 2020, the lowest monthly total since May 2010
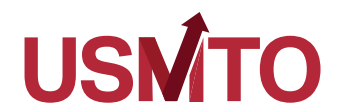
U.S. manufacturing technology orders decreased 26% in April from the previous month to $225.8 million, the lowest monthly total since May 2010, according to the latest U.S. Manufacturing Technology Orders report published by AMT – The Association For Manufacturing Technology. New orders were 39% lower than in April 2019. Total orders through April 2020 were just shy of $1.1 billion, 28% lower than 2019 orders during the same period. “It should not come as a surprise that April numbers were low given the large-scale shut down of the global economy,” said Douglas K. Woods, president of AMT. “Data confirms that U.S. industrial production dropped lower than during even the Great Depression. “The encouraging news is that we are seeing an uptick in May MT orders. The aerospace and automotive sectors have begun retooling and are placing orders for new equipment to ramp up production in the fall. Some MT orders are being delayed, but we are not seeing any cancellations; in fact, April cancellations were lower than the 2019 average. “2020 will still be a down year for MT orders, and we think it is likely that manufacturing will experience uneven growth for the next several quarters. Oxford Economics has forecast a 50% decline in machine tool orders in 2020 (from 2019), and while they have also forecast a robust 84-plus percent increase in MT orders in 2021, this is still a 10% decline from where the industry stood before the pandemic. Consumer confidence, capacity utilization, and the unemployment rate are the key indicators that we will keep our eyes on as they chart future performance.”
Wilmington Machinery unveils new Dual Mold Pallet Molding System
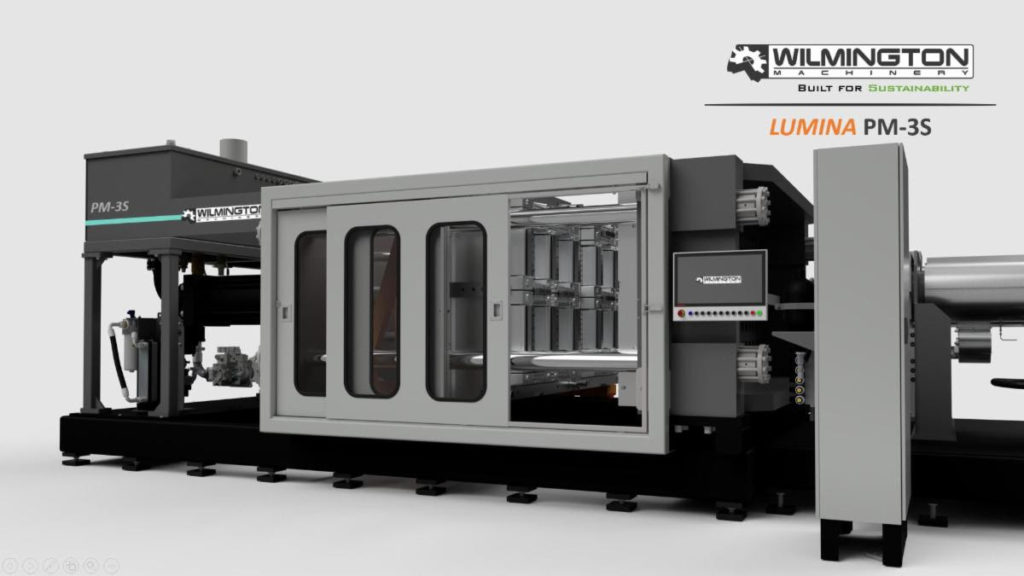
Wilmington Machinery introduced the company’s first LUMINA Pallateer Series molding machine in 2010 because of the increased demand for plastic pallets. Today, Wilmington introduces the newest model of its popular LUMINA Pallateer Series of Plastics Pallet Molding Systems the Model PM-3S. The Model PM-3S is capable of molding two of the same or two different pallets of sizes “up to 52” X 48” and weighing from 16 – 50 pounds each. Hourly production rates of 48 – 72 pallets per hour are achievable with minimal labor, floor-space, and utility requirements. The PM-3S like the other LUMINA Pallateer Models is a low-pressure type injection-molding machine with a two-stage injection unit. The Wilmington two-stage unit processes 100% recycled plastics in either pelletized or flake form. It injects at mold fill rates up to 20 pounds per second with velocity and shot size control from Wilmington’s unique Versafil sequential injection control system. The result of these features is lightweight and low-cost pallets. A PM-3S System includes the molding machine, molds, robot, and all accessories plus know-how and training. It is very versatile with the capability to mold nestable, stackable, or rackable pallets of both one-piece and two-piece construction from a wide variety of virgin or recycled raw materials including blends. Wilmington Machinery has built pallet molding machinery, general-purpose low and medium pressure injection molding machinery, and high capacity extrusion blow molding machinery since its’ founding in 1972. From a modern 65,000 square foot facility in Wilmington, North Carolina, the company is well prepared to meet customers’ unique needs for large plastics machinery products for the circular economy. International shipments are commonplace and can be arranged via the nearby deep-water Port of Wilmington.
IMTS 2020 still on, for now

The International Manufacturing Technology Show (IMTS) is still committed to opening the show in Chicago on September 14 – 19, 2020 at McCormick Place. In a press release Peter Eelman, AMT Vice President, and CXO say that they are committed to opening IMTS as scheduled on September 14. “There are many indications that show us the Manufacturing Technology community is looking forward to IMTS. At this point, from an overall standpoint, IMTS 2020 is at 94% of capacity for exhibit space, some exhibitors are hoping to take more space and grow their booth, and registrations have been steady throughout the onset of the crisis.” “We recognize that IMTS will need to look different in order to keep our audience safe and secure – so we are investigating ways to keep you protected. We are currently redesigning high traffic areas (such as registration, conferences, and receptions), working with trade show partners to ensure a higher level of cleaning protocols are made, and considering new entry point measures such as temperature checks and mask distribution,” Eelman added. In 2020 they are welcoming a new audience to IMTS. The Smart Manufacturing Experience (SMX), originally scheduled to be in Pittsburgh in June, will now be co-located at IMTS. More information on this can be found at www.smartmanufacturingexperience.com “As for Chicago, we remain in constant communication with McCormick Place, the City of Chicago and the State of Illinois to stay abreast of their ever-changing landscape. We have been advised that 2,000 beds have been removed from the alternate care facility and, to date, have had less than a dozen patients. We have also been advised that they are planning to move the entire facility out by June for shows to start up again in July.” said Eelman.