All Integrated Solutions, receives Supplier Award
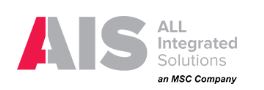
AIS-All Integrated Solutions, an MSC Company, proudly announces its recent award for Outstanding Quality. It was awarded at the Motus Annual 2020 Suppliers Conference. The award recognizes AIS for shipping over 10,000,000 pieces with zero defects. AIS was the only supplier to receive this award in 2020. Everyone from AIS’ quality, warehouse, sales, and account executive teams worked together to provide exceptional service to Motus—they deserve all the credit for the award. “We are extremely proud of our entire team this year. They have truly come together to make sure our customers receive the highest quality services and products. Earning this award is confirmation that AIS’ focus on quality, company culture, and employee training is paying off for our customers,” stated Nick Ruetz, president of AIS-All Integrated Solutions.
CIP turns out material lift in record time to help combat COVID-19
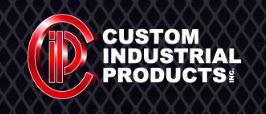
Custom Industrial Products (CIP) announces the production, shipment, and installation in a record time of a Vertical Reciprocating Conveyor (VRC) Lift needed to streamline the production of critically needed ventilators. The entire process from an urgent phone call to an installed operational lift took just seven days as opposed to the typical six to nine weeks. The VRC material lift was expedited in response to the Federal Government’s directive to quickly retrofit domestic factories to produce ventilators which are the most critical machines keeping the sickest COVID-19 patients alive. The call to CIP came from a client, one of the largest domestic automotive manufacturers, who was tasked with renovating an existing multi-level building in order to shift from building automobiles to manufacturing ventilators. The building was a three-level facility located in Indiana. Because the ventilator manufacturing process was to encompass all three levels, an efficient method of moving material between levels was required. The solution was to install a VRC material lift to connect all the floors. The challenge was it normally takes 5-7 weeks just to custom engineer and manufacture a VRC lift to fit a specific space and application. “When the call came in, all of us here at CIP decided we would do whatever was necessary to help our client manufacture ventilators as quickly as possible,” said Kyle Goodwin, Senior Vice President of Custom Industrial Products. “Our entire team, from sales to engineering to manufacturing, came together at a critical time of need for our country and made it happen.” Using video conferencing, CIP was able to remotely analyze the customer’s facility installation area, the production process needs, and the additional requirement to keep the client’s volunteer workforce safe and properly distanced. Based upon the requirements and extremely tight timeframe, CIP chose to utilize the PM Series Modular VRC Material Handling Lift. The CIP PM lift was designed for fast production, quick installation, and safe and simple operation. PM VRCs have a modular design allowing for installation in a quarter of the time needed to install similar VRCs. The lift is just one of the examples of innovations needed to facilitate the lifesaving demands of hospitals, Governors, and the President of the United States during the most critical of times. “The VRC engineering, manufacturing, prewiring, testing, shipping from Florida to Indiana, and installing on three floors took only 7 days – a feat in which we take great pride,” said Tom DePetris, president of Custom Industrial Products. “What a way to celebrate the 20th anniversary of the modular VRC lift that CIP pioneered in 2000.” “This united effort of American manufacturing to battle a global enemy has not been seen in our country since World War II,” DePetris added. The first ventilators produced by the Indiana facility were delivered to hospitals on April 17th.
February 2020 U.S. Cutting Tool orders down 4.2 from January
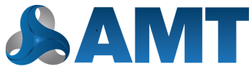
February 2020 U.S. cutting tool consumption totaled $188.2 million, according to the U.S. Cutting Tool Institute (USCTI) and AMT – The Association For Manufacturing Technology. This total, as reported by companies participating in the Cutting Tool Market Report collaboration, was down 4.2 percent from January’s $196.5 million and down 8.5 percent when compared with the $205.6 million reported for February 2019. With a year-to-date total of $384.7 million, 2020 is down 8.5 percent when compared with 2019. These numbers and all data in this report are based on the totals reported by the companies participating in the CTMR program. The totals here represent the majority of the U.S. market for cutting tools. According to Bret Tayne, President of USCTI, “The most recently released February cutting tool statistics reflect the modest slowing we began to see in the latter part of 2019. But these numbers precede the effects of the COVID-19 fallout. I suspect we have all experienced a much steeper drop over the past several weeks. Buckle your seat belts!” “Following a year of consolidation in 2019, cutting tool shipments are set to face a challenging 2020. The 8.5% year-over-year decline in cutting tool shipments in February is slightly worse than the 2.4% year-over-year drop in total durable goods shipments. With the economy facing a coronavirus-induced recession, the outlook through the summer will be challenging. A stronger dollar reduced international demand, and higher corporate spreads will likely add to the sectoral headwinds. However, a gradual relaxation of lockdown measures in the latter part of 2020, along with unprecedented fiscal and monetary policy stimulus should help progressively support activity in 2021,” said Greg Daco, Chief U.S. Economist for Oxford Economics USA. The Cutting Tool Market Report is jointly compiled by AMT and USCTI, two trade associations representing the development, production, and distribution of cutting tool technology and products. It provides a monthly statement on U.S. manufacturers’ consumption of the primary consumable in the manufacturing process – the cutting tool. Analysis of cutting tool consumption is a leading indicator of both upturns and downturns in U.S. manufacturing activity, as it is a true measure of actual production levels. Historical data for the Cutting Tool Market Report is available dating back to January 2012. This collaboration of AMT and USCTI is the first step in the two associations working together to promote and support U.S.-based manufacturers of cutting tool technology. The graph below includes the 12-month moving average for the durable goods shipments and cutting tool orders. These values are calculated by taking the average of the most recent 12 months and plotting them over time.
GROB Systems announces Linear Pallet Storage System for numerous machine types
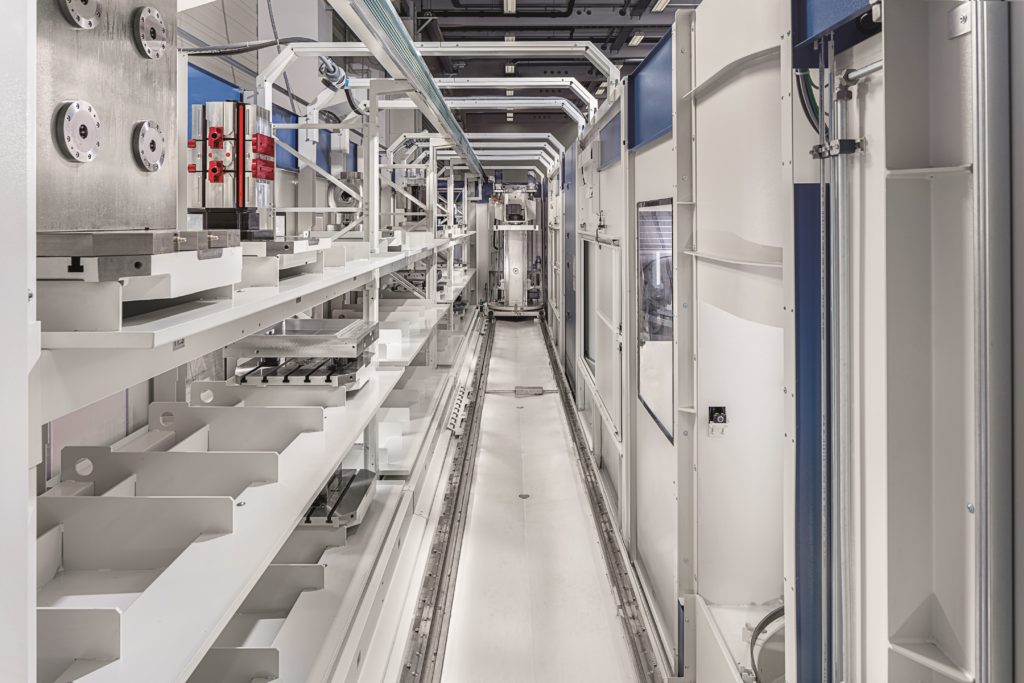
The modular system links machining systems for improved production GROB Systems, a global provider in the development of manufacturing systems and machine tools, announces its newly developed linear pallet storage system (PSS-L) – a highly automated, flexible manufacturing line that complements a wide variety of part types. The PSS-L is ideally suited as a modular system for individual machines or for interlinking the same machining systems. With it, up to five machine tools – including the G550a, G552, and G552T – can be connected to a pallet storage racking with a maximum of 87 pallet positions. The PSS-L can also operate “locked out” of a system, as an independent machine. Additionally, with the PSS-L, a significant increase in machine utilization and economic production can be achieved, and a longer unmanned production period is made possible. Other advantages include a high storage density with a small footprint, a cost-conscious acquisition investment, as well as the excellent visibility into the workspace and the pallet storage locations. The PSS-L is equipped with a linear traveling pallet changer system with a pallet gripper to transport the materials between setting stations, work-piece deposits, and machines. No cable track is used and the pallets are staged close to the machine to prevent long exchange times. The system also comes with production control software, so that users have a simple, intuitive organization of pallets and parts with associated process steps. Customers can have autonomous parts and pallet control while considering resources, along with monitoring and verification of tool resources for all scheduled orders.
Z-Incline elevates IQF 14 feet with no problem or mess
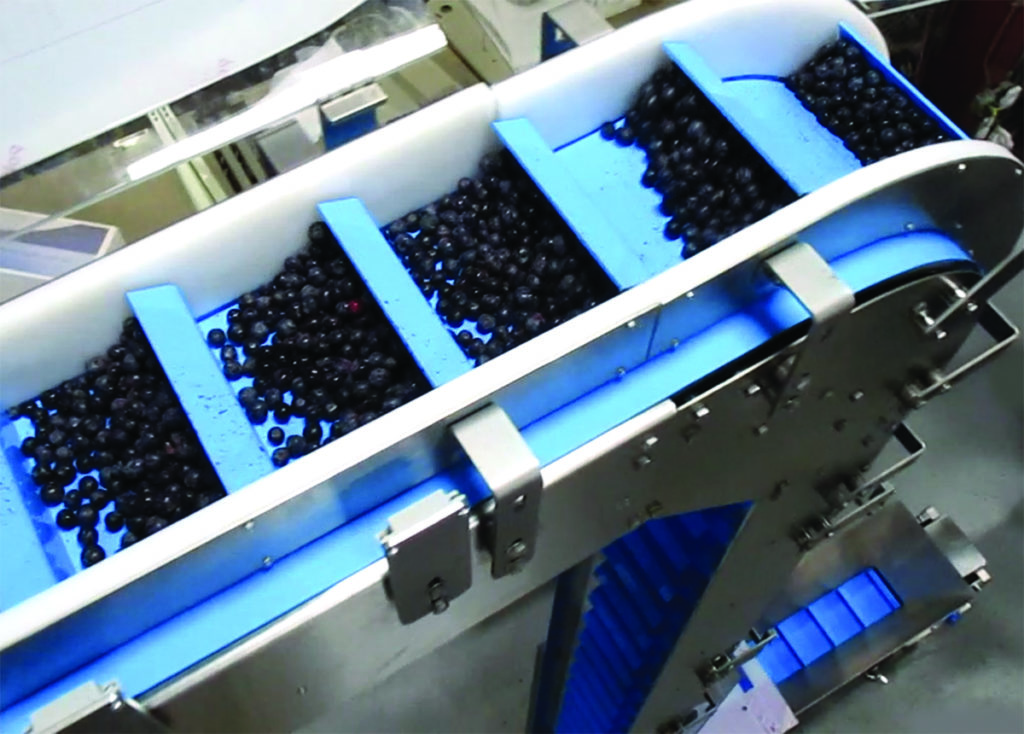
Multi-Conveyor recently built this stainless steel vertical scoop flight elevator that raises fresh frozen fruit over 14′ in a small footprint. The operator manually loads bulk individually quick frozen (IQF) product into a specially designed infeed hopper where it will accumulate until the conveyor can take it away. The product inclines and then discharges onto a customer supplied vibratory scale feeder with a total throughput of approximately 75 pounds per minute. A local NEMA 4X VFD was supplied to start and stop the conveyor as called for by the customer’s scale and to control the motor speed. Hinged polycarbonate covers with magnetic latches keep berries from falling out of the flight pockets when overloaded. Belt hold-down rollers make smooth transitions from horizontal to vertical with simplistic one-bolt removal for maintenance or sanitation. Multi-Conveyor is a leading manufacturer of standard and custom conveyor solutions for End-Users, Integrators, Engineering firms, Automation/Robotics, AI, OEM’s and Contract Packagers across multiple markets. We specialize in conveyor systems for packaging or material handling for nearly every industry, product, shape, and size. Our customers report they select Multi-Conveyor for concept/design, engineering skills, quality product, the best value, and prompt delivery. Multi-Conveyor excels in sanitary conveyor, easy to maintain, clean-in-place or “no tools required” belt changeover systems for nearly any industry. We direct manufacture stainless steel and mild steel construction conveyors for tabletop chains, modular plastic belts, fabric belting and now custom MDR. Our in-house electrical and engineering departments execute the controls, panels, devices, PLCs, VFDs, HMIs, safety, inspection and sensors needed to integrate our systems with multiple packaging platforms. Quick ship plastic chain and low-profile, small transfer, pre-engineered sanitary and non-sanitary belt systems are available for quick delivery.
January 2020 U.S. Cutting Tool Orders up 5% from December 2019
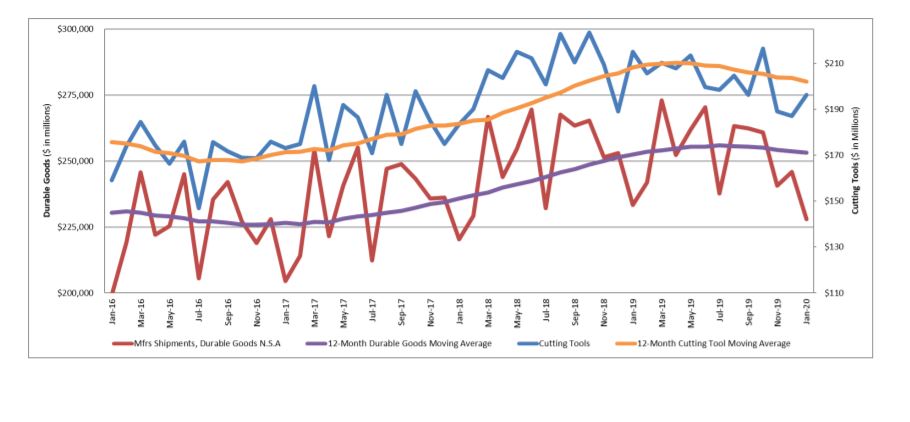
January 2020 U.S. cutting tool consumption totaled $196.5 million, according to the U.S. Cutting Tool Institute (USCTI) and AMT – The Association For Manufacturing Technology. This total, as reported by companies participating in the Cutting Tool Market Report collaboration, was up 5 percent from December’s $187.2 million and down 8.6 percent when compared with the $215.1 million reported for January 2019. These numbers and all data in this report are based on the totals reported by the companies participating in the CTMR program. The totals here represent the majority of the U.S. market for cutting tools. According to Brad Lawton, Chairman of AMT’s Cutting Tool Product Group, “What is uncertainty? For the cutting tool industry, it could be slowly declining sales volumes for at least the last half of 2019, all international markets declining with the U.S. being the last to follow the pattern, stock market volatility, an election year and COVID-19! Did I miss anything? Now that is uncertainty, welcome to the new decade!” “Starting the 2020 calendar year behind January 2019 is not a surprise based on last year’s strong start and the economic headwinds facing the market today. The metalworking industry is feeling the negative effects of a flat automotive market and an aerospace market that has virtually halted the entire supply chain of the 737MAX. IHS forecasts have warned of a drop in consumption in the first quarter and this has unfortunately come to fruition,” said Tom Haag, President of SGS Kyocera. The Cutting Tool Market Report is jointly compiled by AMT and USCTI, two trade associations representing the development, production, and distribution of cutting tool technology and products. It provides a monthly statement on U.S. manufacturers’ consumption of the primary consumable in the manufacturing process – the cutting tool. Analysis of cutting tool consumption is a leading indicator of both upturns and downturns in U.S. manufacturing activity, as it is a true measure of actual production levels. Historical data for the Cutting Tool Market Report is available dating back to January 2012. This collaboration of AMT and USCTI is the first step in the two associations working together to promote and support U.S.-based manufacturers of cutting tool technology. The graph below includes the 12-month moving average for the durable goods shipments and cutting tool orders. These values are calculated by taking the average of the most recent 12 months and plotting them over time.
Custom Caldwell Beam lifts Electricity Cable Reels
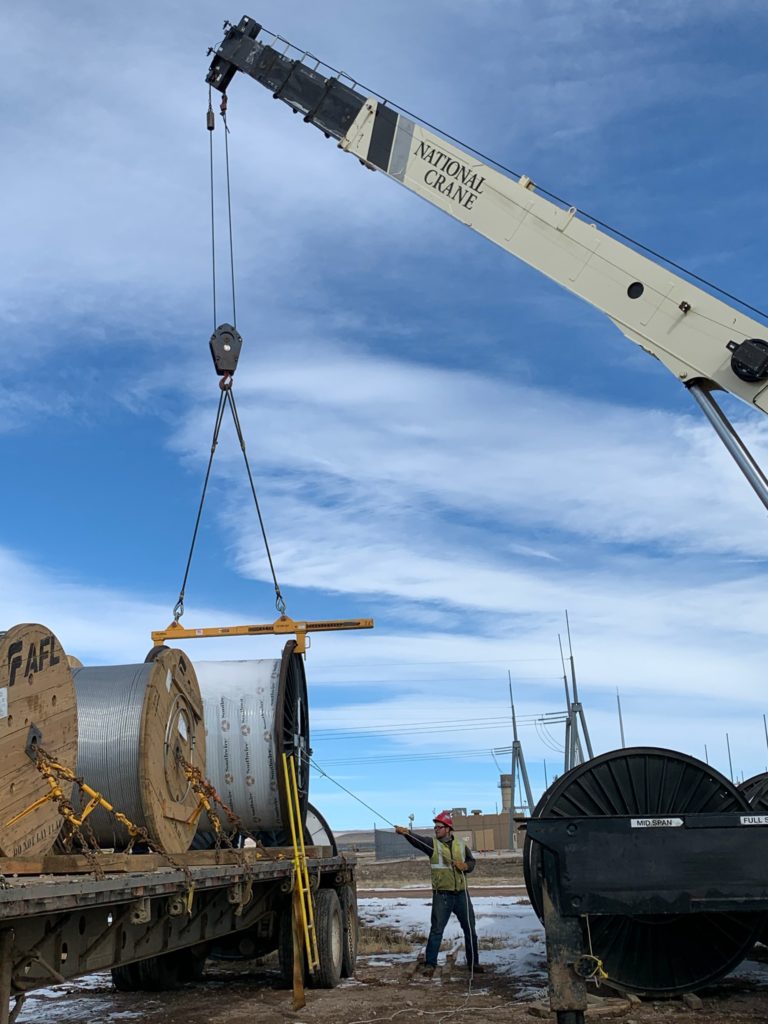
A 26,000-lb. (13-ton) capacity custom lifting beam from Caldwell is being used to lift reels of electrical cable off flatbed trailers. The adjustable beam, which spans 48 in. to 87 in., was recently delivered to a high voltage electrical transmission contractor by Caldwell distributor Western Sling. The provider of lifting and rigging equipment has facilities in Denver, Colorado and Casper, Wyoming. The end-user was seeking a solution for repeated offload of reels of the electrical line that arrive by semi-trailer, where the weight and dimensions can vary with each lift, depending on the type, size, and length of cable. The custom reel lifter met the specifications where a standard, fixed below-the-hook solution would have added time and complexity to each lift. Joey Detrick, inside sales at Western Sling, said: “The bottom hook dimensions were the key here. Beyond the adjustability of the solution, we always enjoy providing Caldwell solutions because the products are backed by history, quality, and safety. Further, we know the equipment will be delivered with all the relevant paperwork needed to satisfy buying decision-makers and supervisors at the modern-day job site.” In a recent case study (pictured), the beam was used beneath the hook of a National Crane boom truck. However, it can be rigged with any crane that suits the requirements of the site, reels, and specifics of the project. Detrick explained that in this instance, 28,000-lb. capacity, 10 ft.-long wire rope slings were used at the recommended 45-degree angle to achieve the most efficient, safest lift. They were sourced from the Western Sling rigging store. The beam and rigging configuration also saves the high voltage electrical transmission contractor time because only one rigger is required in addition to the crane operator. Detrick outlined the step-by-step rigging process: the crane hook lowers the wire rope slings that are already attached to the beam down to the reel. The rigger then utilizes the handle on the side of the adjustable portion of the beam and aligns it with a lip as it sets over the flange of the reel. Detrick reported that this application is indicative of current trends that see a slowing of coal and oilfield work. He said: “Business remains steady because we are actively diversifying and moving into the electrical and wind farm sectors. Construction and re-power jobs are also driving demand; we continue to service oil and coal projects as the need arises.”
Raymond welder awarded gold medal in group skills competition
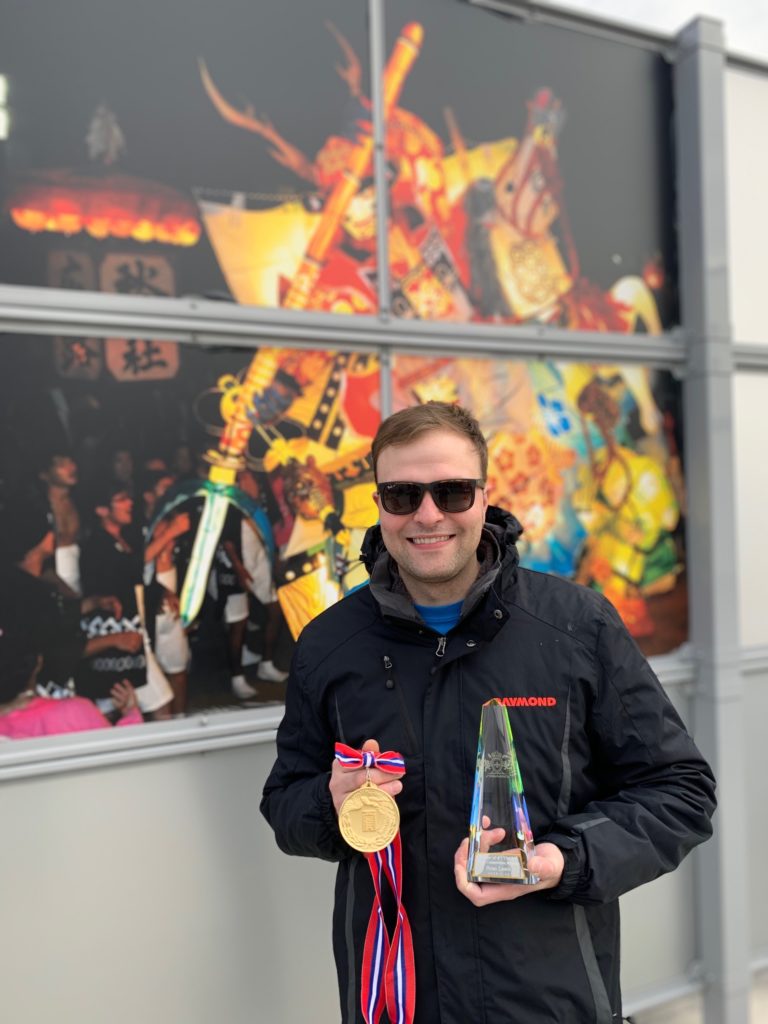
The Raymond Corporation was represented by Raymond welder Ryan Lewis at the Toyota Material Handling Group (TMHG) Skills Competition in Takahama, Japan, in February 2020. To showcase their skill sets, participants had to weld a steel pressure vessel performing tack welding, semi-automatic welding, and finishing of the surface. Lewis placed first in the competition among other competitors across TMHG facilities in the United States, Italy, Sweden, France, and China. “It was a great honor to be invited to participate in the prestigious TMHG Skills Competition among such amazing competitors from around the world,” Lewis said. “Placing first and receiving the gold medal was a dream of a lifetime and truly showcased that I put my all into the training and into my position at Raymond each and every day.” Accompanying Lewis was Steve Lewey, Raymond welder and welding competitor from the 2019 TMHG Skills Competitions in Japan. Lewey placed second last year in the competition. In 2015, Raymond’s internal welding competitions began, helping promote friendly competition and enhancing welding skills and knowledge. Each year after, the welding competition winner has earned the invitation by Toyota to travel to Japan to compete in the TMHG Skills Competition. “Toyota held the fourth annual TMHG Skills Competition to know and understand where our company’s manufacturing skills are and to promote higher skills learning in the Toyota Material Handling Group. While other welders’ skills are improving year by year, Ryan demonstrated his welding skills beautifully and won the gold prize,” said Hisanori Miyajima, executive officer, Toyota Industries Co. “We would like to congratulate and thank not only Ryan but also his supporting members at Raymond. We hope Ryan will continue to improve his expert welding skills while also continuing to support the quality of Raymond products.”
2019 U.S. Cutting Tool Orders close at 2.4 Billion
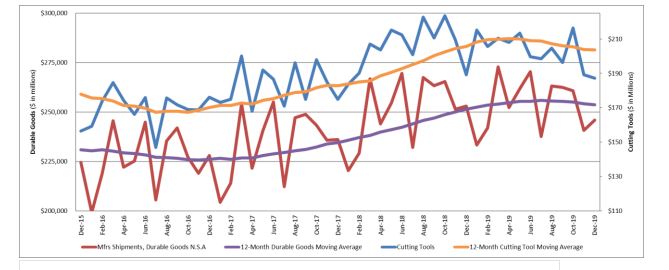
December 2019 U.S. cutting tool consumption totaled $187.2 million, according to the U.S. Cutting Tool Institute (USCTI) and AMT – The Association For Manufacturing Technology. This total, as reported by companies participating in the Cutting Tool Market Report collaboration, was down 1 percent from November’s $189.1 million and down 1 percent when compared with the $189.1 million reported for December 2018. With a year-to-date total of $2.4 billion, 2019 is down 1 percent when compared with 2018. These numbers and all data in this report are based on the totals reported by the companies participating in the CTMR program. The totals here represent the majority of the U.S. market for cutting tools. According to Bret Tayne, President of USCTI, “The cutting tool industry ended the year with a small decline from 2018, which was consistent with the forecasts that were produced for our industry. Despite some signs of continued slowness into the first quarter of this year, there are rays of optimism in various reports, and there may be an opportunity for a rebound as discreet problems (Coronavirus, commercial aviation issues, etc.) recede.” “Orders for cutting tools fell at the end of 2019, in line with continued weakness in key manufacturing sectors such as aerospace and motor vehicles. Yet December’s decline in orders was moderate as compared to previous months, down 1% from November, which leaves them down 1% for all of 2019 over 2018,” said Mark Killion, Director of U.S. Industry at Oxford Economics. The Cutting Tool Market Report is jointly compiled by AMT and USCTI, two trade associations representing the development, production, and distribution of cutting tool technology and products. It provides a monthly statement on U.S. manufacturers’ consumption of the primary consumable in the manufacturing process – the cutting tool. Analysis of cutting tool consumption is a leading indicator of both upturns and downturns in U.S. manufacturing activity, as it is a true measure of actual production levels. Historical data for the Cutting Tool Market Report is available dating back to January 2012. This collaboration of AMT and USCTI is the first step in the two associations working together to promote and support U.S.-based manufacturers of cutting tool technology. The graph below includes the 12-month moving average for the durable goods shipments and cutting tool orders. These values are calculated by taking the average of the most recent 12 months and plotting them over time.
Multi-Conveyor accumulates non-rounds using Pneumatic Sweeper Arm
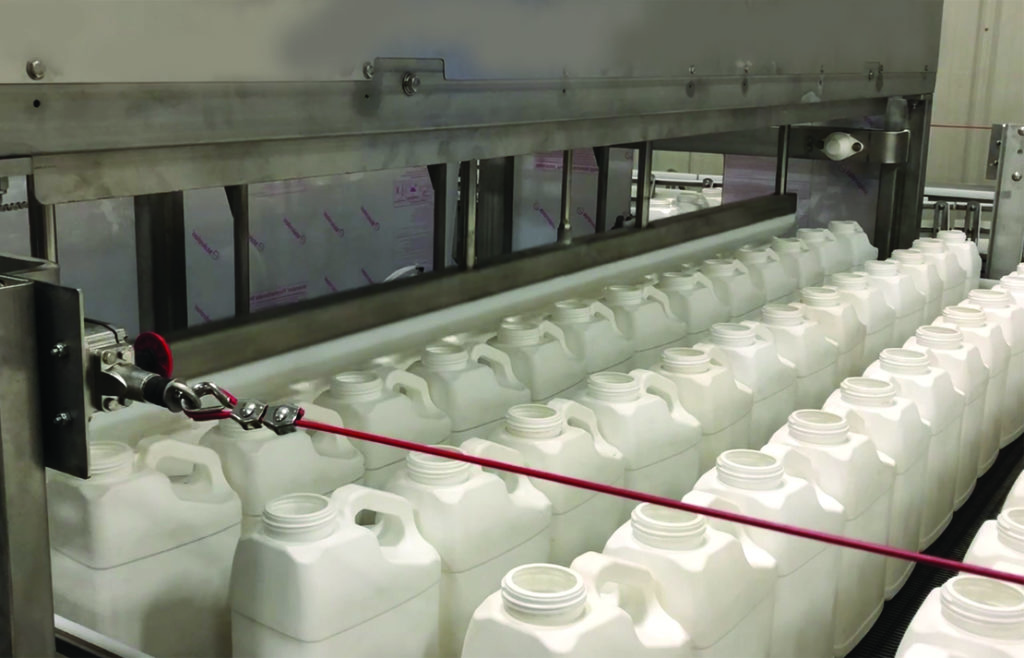
Multi-Conveyor recently designed and engineered this stainless-steel constructed table-top and plastic belt conveyor system featuring pneumatic pusher “sweep arm” accumulation tables designed for “non-round” plastic bottles. The plastic bottles will travel from a customer supplied labeler through over 100 feet of conveyor including elevation changes of up to 21” in some areas, side transfers, and pneumatic merges, diverts, clamps and stops handling both empty bottle and full bottle accumulation along the way – ultimately ending at a case packer. The distinctive bi-directional accumulation tables include pneumatic stops to form a row of products at the face of the table. A pneumatic “sweep arm” will push a single row at a time onto the table when the system is in “Accumulation Mode.” The bi-di tables are designed to index with every row of the product then discharge in the same method, using a “pneumatic puller” to extract each row. The system provides both inline and off-line accumulation on two (2) 200 sq. ft. accumulation tables. The challenge was to accumulate quart, gallon 2.5 gallons and 11 liter nearly rectangular bottle designs in one system. Standard bi-di accumulation table conveyors are used almost exclusively for round shaped products – which makes this system completely unique. NOTE: The conveyor system has the ability to merge accumulated products back into the mainline during normal production flow using the Multi-Conveyor engineered and manufactured control system of devices, sensors, HMI screens, and UL listed panels.
Nucar announces new Board of Directors member
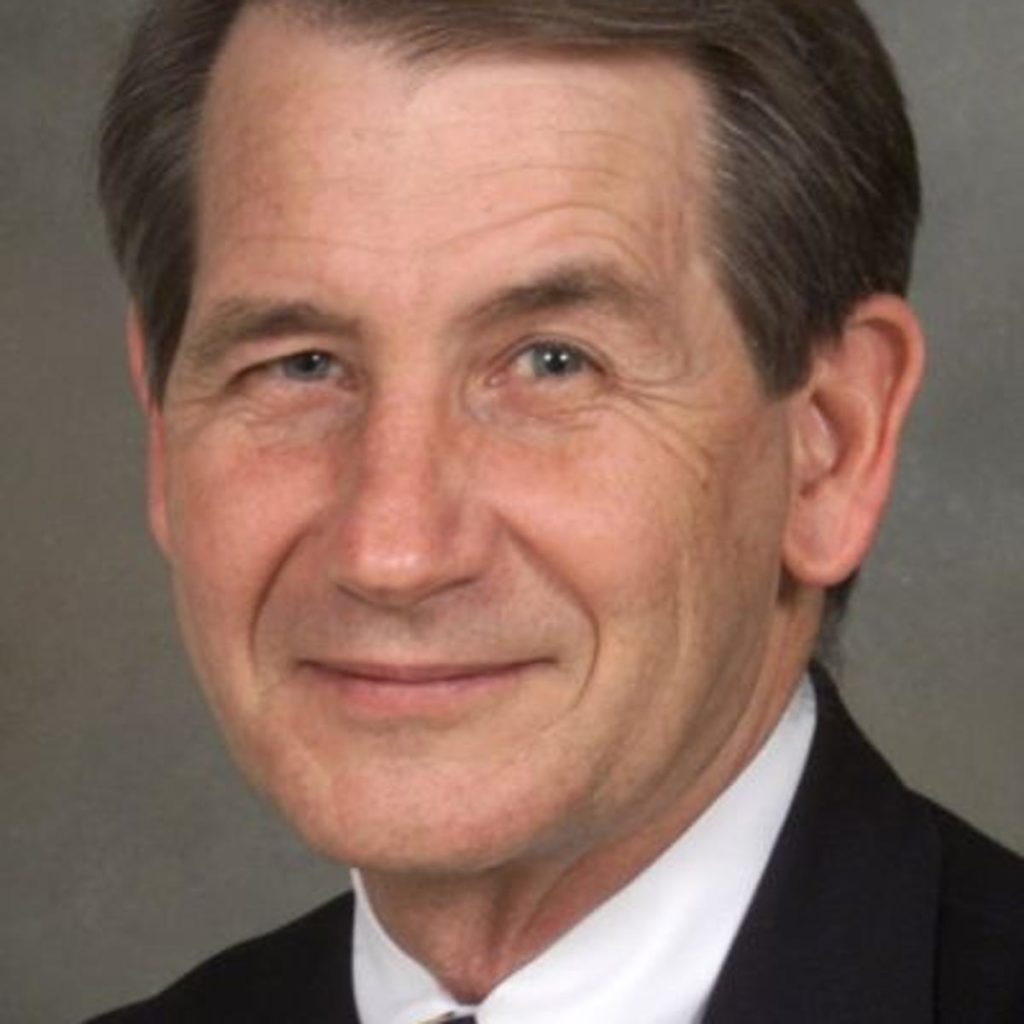
Nucor Corporation announced that its Board of Directors has elected Joseph D. Rupp as a director effective immediately. Mr. Rupp, 69, most recently served as Chairman of the board of directors of Olin Corporation, a leading vertically integrated global manufacturer and distributor of chemical products and a leading U.S. manufacturer of ammunition, from May 2016 until his retirement in April 2017. Prior to that, Mr. Rupp served as Chairman and Chief Executive Officer of Olin from May 2014 to May 2016, Chairman, President and Chief Executive Officer of Olin from June 2005 to May 2014 and President and Chief Executive Officer of Olin from January 2002 to June 2005. Prior to 2002, Mr. Rupp served in various positions of increasing responsibility with Olin, which he originally joined in 1972. Mr. Rupp currently serves on the boards of directors of Cass Information Systems, Inc., O-I Glass, Inc. (formerly Owens-Illinois, Inc.), Quanex Building Products Corporation and Dot Foods, Inc. (non-public), and is on the Board of Trustees of the Missouri University of Science and Technology. Mr. Rupp served as a director of Olin from 2002 to 2017. Mr. Rupp holds a Bachelor of Science degree in metallurgical engineering from the Missouri University of Science and Technology. “Joe brings extensive experience in the metal-related manufacturing industry as well as strong executive leadership and strategic management skills and significant public company board experience,” said Leon J. Topalian, president and Chief Executive Officer of Nucor. “We are fortunate to have Joe join the Nucor Board and we look forward to benefiting from his service and insight,” said John H. Walker, Non-Executive Chairman of the Board of Nucor.
U.S. Cutting Tool Orders down 1% in November Year to Date
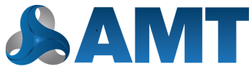
November 2019 U.S. cutting tool consumption totaled $189.1 million, according to the U.S. Cutting Tool Institute (USCTI) and AMT – The Association For Manufacturing Technology. This total, as reported by companies participating in the Cutting Tool Market Report collaboration, was down 12.6 percent from October’s $216.4 million and down 9.7 percent when compared with the $209.4 million reported for November 2018. With a year-to-date total of $2.3 billion, 2019 is down 1.1 percent when compared with 2018. Please note revisions to September 2019 through October 2019 data. These numbers and all data in this report are based on the totals reported by the companies participating in the CTMR program. The totals here represent the majority of the U.S. market for cutting tools. According to Brad Lawton, Chairman of AMT’s Cutting Tool Product Group, “The Cutting Tool Industry has been managing through declining sales volumes for 2019. The economic forecasts indicate that this trend will continue into 2020. However, the recent progress that has been accomplished with Trade Agreements could improve economic activity.” “The CTMR did not drop off as significantly as machine tool orders in 2019 but was on a downward trend for most of the year and remained in negative territory. We should see an upturn in December compared to the previous month as year-end budgets are expended. I’m actually surprised orders are as close to 2018 levels as they are, and that may be due to relatively high capacity utilization rates in many industries,” said Chris Kaiser, CEO of Big Kaiser. The Cutting Tool Market Report is jointly compiled by AMT and USCTI, two trade associations representing the development, production, and distribution of cutting tool technology and products. It provides a monthly statement on U.S. manufacturers’ consumption of the primary consumable in the manufacturing process – the cutting tool. Analysis of cutting tool consumption is a leading indicator of both upturns and downturns in U.S. manufacturing activity, as it is a true measure of actual production levels. Historical data for the Cutting Tool Market Report is available dating back to January 2012. This collaboration of AMT and USCTI is the first step in the two associations working together to promote and support U.S.-based manufacturers of cutting tool technology. The graph below includes the 12-month moving average for the durable goods shipments and cutting tool orders. These values are calculated by taking the average of the most recent 12 months and plotting them over time.
Jescraft announces opening of new manufacturing facility in Connecticut
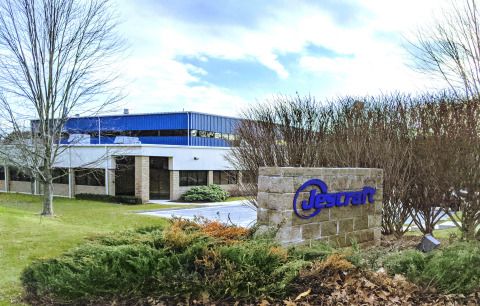
New facility in Oxford, CT signals strong growth Jesco Iron Craft, Inc. d/b/a Jescraft announced on Friday that it will open a new manufacturing facility in Oxford, Connecticut with anticipated opening date of March 2020. This newest expansion comes on the heels of strong growth for the company and is one of several new investments Jescraft has made in recent months. New equipment expenditures, a revamped online presence, and the implementation of new technologies at the corporate level signal strong business growth for the material handling equipment manufacturer. The new facility is comprised of 28,000 square feet of plant and office space, with loading dock capabilities, oversized high-bay doors, 30’ clear height warehouse, expanded coating system capabilities, along with several acres for future expansion. The facility is located at 116 Willenbrock Road in the Willenbrock Industrial Park, an established office and industrial park, which is approximately one mile from the Waterbury/Oxford Airport. It is easily accessible for commercial truck transportation, centrally located between New Haven, Danbury, Bridgeport and Waterbury, CT and is located less than one (1) mile from I-84 and I-95 corridors, with easy access to Routes 67, 188, 42 and 34. While the new Oxford plant will be initially set up for assembly, it will eventually serve as a full-scale manufacturing and warehousing location. “This new location allows us to better align our production with our customers’ demands in a rapidly changing e-commerce landscape,” says Brown. “Through recent key investment and expansion projects, Jescraft can lead our segment in responsiveness, production and delivery by increasing stocked items and shortening lead times for non-stock items for our rapidly increasing customer base.”
Nucor Steel Arkansas to add Coil Paint Line

Nucor Corporation’s Board of Directors has approved an expansion project which will add a coil paint line at the company’s sheet mill in Mississippi County, Arkansas. The new coil paint line will have a capacity of 250,000 tons per year and is expected to start up in the first half of 2022. “The new coil paint line will diversify our product and market mix by adding additional processing capability and will allow us to expand the value-added products we offer. We will be able to compete in new markets, such as roofing and siding, light fixtures and appliances, as well as strengthen our existing market position in HVAC, garage doors and service centers,” said Jay Henderson, Vice President & General Manager of Nucor Steel Arkansas. “This new line will also improve the quality and service we can provide to our pre-paint customers.” Nucor Steel Arkansas opened in 1992 and produces approximately 2,600,000 tons of hot-rolled sheet steel for automotive, appliance, construction, pipe and tube and many other applications. This capital investment will allow the mill to build a high-quality continuous coil coating line that will have a thickness range of 0.010 to 0.065 inches and widths of 35 to 72 inches. Nucor Steel Arkansas recently completed construction of a new speciality cold mill complex and is currently building a new galvanizing line which will begin operating in 2021. “This latest Nucor expansion in Mississippi County adds to their lines of quality products that are in demand across the country and the globe. Arkansas is proud to have Nucor recognized as a leading steel products producer, and we’re proud of how the Arkansas workforce contributes to that distinction,” said. Nucor and its affiliates are manufacturers of steel and steel products, with operating facilities in the U.S., Canada and Mexico. Products produced include: carbon and alloy steel — in bars, beams, sheet and plate; hollow structural section tubing; electrical conduit; steel piling; steel joists and joist girders; steel deck; fabricated concrete reinforcing steel; cold finished steel; precision castings; steel fasteners; metal building systems; steel grating; and wire and wire mesh. Nucor, through The David J. Joseph Company, also brokers ferrous and nonferrous metals, pig iron and hot briquetted iron / direct reduced iron; supplies ferro-alloys; and processes ferrous and nonferrous scrap. Nucor is North America’s largest recycler.
U.S. Cutting Tool orders up 10.2% in October from September
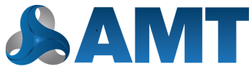
October 2019 U.S. cutting tool consumption totaled $216.1 million, according to the U.S. Cutting Tool Institute (USCTI) and AMT – The Association For Manufacturing Technology. This total, as reported by companies participating in the Cutting Tool Market Report collaboration, was up 10.2 percent from September’s $196 million and down 3.3 percent when compared with the $223.5 million reported for October 2018. With a year-to-date total of $2.1 billion, 2019 is down 0.1 percent when compared with 2018. Please note there were revisions to September 2019. These numbers and all data in this report are based on the totals reported by the companies participating in the CTMR program. The totals here represent the majority of the U.S. market for cutting tools. According to Bret Tayne, President of USCTI, “The modest decline in the cutting tool market that was forecast by IHS and others seems to have come to fruition. However, it is heartening to see that October improved over the prior month. We are also seeing improvement in some other recent indicators, such as the recent manufacturing employment increase in November and some of the Federal Reserve Bank Regional Updates, as well as some anecdotal evidence of a stronger finish to 2019.” “October’s cutting tool data was an increase over September’s result, but this largely reflects seasonality. October performance has only fallen below September once since 2012 (in 2016). Rather, October was the sixth consecutive month with a year-over-year decline, undoing a strong start to the year and bringing 2019 below 2018 on a cumulative year-to-date basis. This is consistent with PMI results which indicate weakness in manufacturing in general, and with slowing car sales and continuing issues with the Boeing 737. Automotive and aerospace are the two largest demanders of cutting tool products. It is encouraging that October’s decline was the smallest of the past three months, and may indicate that a trough is nearing. Trade frictions appear to be easing, and Boeing is expected to increase production in the first quarter of 2020. It is premature to expect a resumption of growth, but 2020 looks to offer some improvement.,” said Scott Hazelton, Managing Director of Economics & Country Risk at IHS Markit. The Cutting Tool Market Report is jointly compiled by AMT and USCTI, two trade associations representing the development, production, and distribution of cutting tool technology and products. It provides a monthly statement on U.S. manufacturers’ consumption of the primary consumable in the manufacturing process – the cutting tool. Analysis of cutting tool consumption is a leading indicator of both upturns and downturns in U.S. manufacturing activity, as it is a true measure of actual production levels. Historical data for the Cutting Tool Market Report is available dating back to January 2012. This collaboration of AMT and USCTI is the first step in the two associations working together to promote and support U.S.-based manufacturers of cutting tool technology. The graph below includes the 12-month moving average for the durable goods shipments and cutting tool orders. These values are calculated by taking the average of the most recent 12 months and plotting them over time.
Nucor announces new Board members

Nucor Corporation announced that its Board of Directors has elected Leon J. Topalian as a director and John H. Walker to serve as Non-Executive Chairman of the Board of Directors, both effective January 1, 2020. Mr. Topalian is the President and Chief Operating Officer of Nucor and will become the Chief Executive Officer of Nucor on January 1, 2020. Mr. Walker, who has more than 35 years of experience in metal-related manufacturing and fabricating industries, has served as a member of Nucor’s Board of Directors since 2008 and as Lead Director of Nucor since 2017. Mr. Topalian served as an Executive Vice President of Nucor from 2017 to 2019 and as a Vice President of Nucor from 2013 to 2017. He has been employed by Nucor in various capacities since 1996, including serving as general manager at two of Nucor’s facilities, in Arkansas and Illinois, as well as a Melting and Casting Manager, an Operations Manager, a cold mill production supervisor and a project engineer. Mr. Walker served as Non-Executive Chairman of Global Brass and Copper Holdings, Inc. from 2014 to 2019, was Executive Chairman of Global Brass and Copper from 2013 to 2014 and was Chief Executive Officer of Global Brass and Copper from 2007 to 2014. Prior to joining Global Brass and Copper, Mr. Walker was President and Chief Executive Officer of The Boler Company, Chief Executive Officer, President and Chief Operating Officer of Weirton Steel Corporation and President of flat rolled products for Kaiser Aluminum Corporation. Mr. Walker is also a director of Owens-Illinois, Inc. and will serve as a director of Otis Elevator Company after its planned separation from United Technologies Corporation in 2020. “Leon and John have made outstanding contributions over their many years of service to Nucor,” said John J. Ferriola, Chairman and Chief Executive Officer of Nucor. “This is the culmination of many years of thoughtful succession planning, and I have full confidence in their leadership.” “It is incredibly humbling to be asked to join the Board of Directors, and I look forward to working with John Walker and the rest of the Board to lead Nucor,” said Mr. Topalian. “Our tremendous culture has produced solid results in 2019 and I look forward to building on those successes in coming years.” “I am honored to have been chosen by my fellow directors to serve as Non-Executive Chairman and enthusiastically welcome Leon to the Board,” Mr. Walker said. “I look forward to continuing to work with him, the rest of the Board and all of our teammates at Nucor in this new role.”
U.S. cutting tool orders up 0.2% in September 2019 YTD/YTD
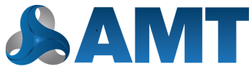
September 2019 U.S. cutting tool consumption totaled $195.9 million, according to the U.S. Cutting Tool Institute (USCTI) and AMT – The Association For Manufacturing Technology. This total, as reported by companies participating in the Cutting Tool Market Report collaboration, was down 4.3 percent from August’s $204.7 million and down 7 percent when compared with the $210.6 million reported for September 2018. With a year-to-date total of $1.8 billion, 2019 is up 0.2 percent when compared with 2018. Please note there were revisions to August 2019.These numbers and all data in this report are based on the totals reported by the companies participating in the CTMR program. The totals here represent the majority of the U.S. market for cutting tools. According to Brad Lawton, Chairman of AMT’s Cutting Tool Product Group, “The September numbers focus on the one word that describes our everyday attitudes ‘uncertainty,’ and not having a clue of what to expect from our domestic economy and the global economy. So the further understanding of this issue is ever-present from the media, political wars in Washington, the global trade wars, and the overall effects of these issues on the global economies. The changes are not recessionary, but the changes are concerning.” “It’s no surprise that U.S. cutting tool consumption continues to slow on a year-over-year basis as machine tool sales weaken and the manufacturing sector enters a recession — primarily because of the U.S.-China trade. Though cutting tool consumption year-to-date remains slightly ahead of 2018, the cutting tool market will likely continue to soften for the remainder of the year and into 2020 as sales are typically at their low points from November through February — even in years when manufacturing output is rising,” said Alan Richter, Editor of Cutting Tool Engineering Magazine. Alan added, “Another element to consider is that cutting tool manufacturers keep developing and introducing new tool grades that last longer than previous grades enabling part manufacturers to increase throughput. Although the new tools might cost more initially, end-users who set their sights on long-term rather than short-term cost savings are able to reduce their overall production costs by boosting productivity. Toolmakers may sell less product, but their customers increase their competitiveness and are able to survive and, hopefully, thrive as a result of purchasing higher-performing cutting tools.” The Cutting Tool Market Report is jointly compiled by AMT and USCTI, two trade associations representing the development, production, and distribution of cutting tool technology and products. It provides a monthly statement on U.S. manufacturers’ consumption of the primary consumable in the manufacturing process – the cutting tool. Analysis of cutting tool consumption is a leading indicator of both upturns and downturns in U.S. manufacturing activity, as it is a true measure of actual production levels. Historical data for the Cutting Tool Market Report is available dating back to January 2012. This collaboration of AMT and USCTI is the first step in the two associations working together to promote and support U.S.-based manufacturers of cutting tool technology. The graph below includes the 12-month moving average for the durable goods shipments and cutting tool orders. These values are calculated by taking the average of the most recent 12 months and plotting them over time.
Multi-Conveyor LLC constructs wire mesh cooling conveyor to transport bakery dough
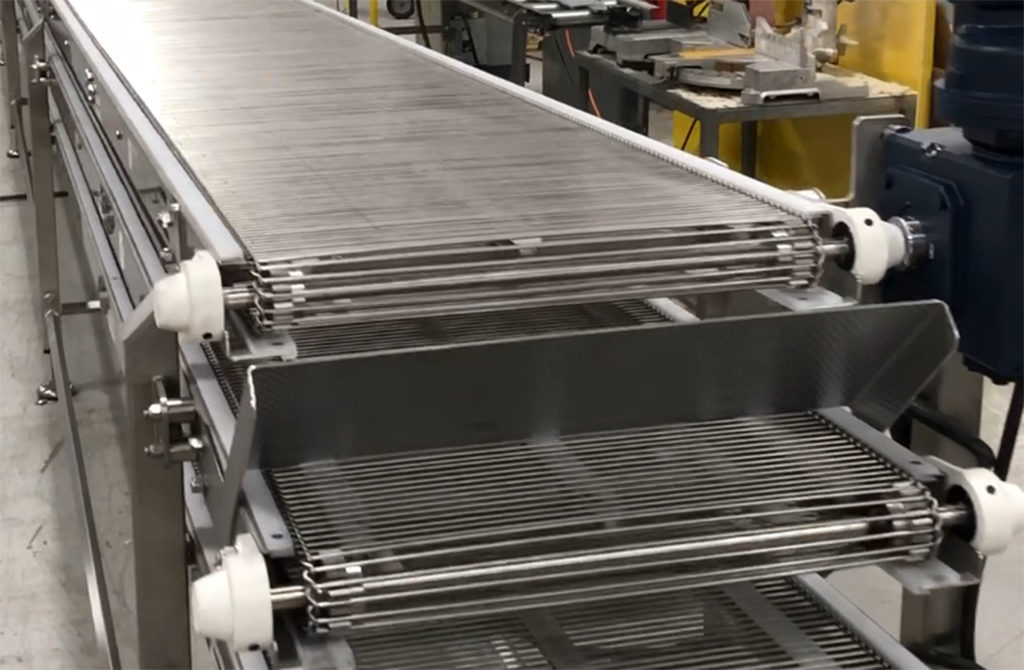
Multi-Conveyor LLC has recently built a stainless steel, three-tiered wire mesh belt cooling conveyor to transport bakery dough over 94′ feet. An existing fryer feeds the 195° degree product onto this bolted-construction conveyor. It then moves through three tiers of 34′ by 20″ cooling wire mesh before discharging onto an existing icing machine. A pitched “chute” guides the product as it gently rotates on its back side. The product then moves through another 34′ through the second tier then uses the same angled chute approach on the opposite end, dropping onto the third tier. The system only runs about five feet per minute, during the entire 94′ of conveyor belt, allowing time for product to reach the required cooled temperature. Conveyor discharge ends feature minimum diameter nose-bar or minimum diameter sprockets for ease of product transfer. Learn more about wire mesh belt conveyors. Then, choose from over 90 videos of all conveyor technologies that may be used for snack food and bakery products by visiting https://www.multi-conveyor.com/multi-media-center/videos
U.S. Cutting Tool orders up 3.3% in August from July
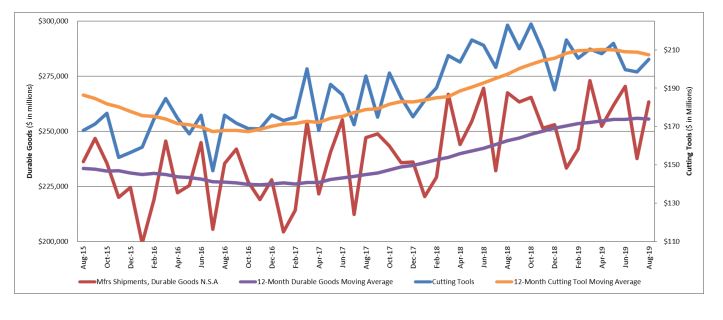
August 2019 U.S. cutting tool consumption totaled $205.1 million according to the U.S. Cutting Tool Institute (USCTI) and AMT – The Association For Manufacturing Technology. This total, as reported by companies participating in the Cutting Tool Market Report collaboration, was up 3.3 percent from July’s $198.5 million and down 8 percent when compared with the $222.8 million reported for August 2018. With a year-to-date total of $1.7 billion, 2019 is up 1.2 percent when compared with 2018. These numbers and all data in this report are based on the totals reported by the companies participating in the CTMR program. The totals here represent the majority of the U.S. market for cutting tools. According to Phil Kurtz, President of USCTI, “August numbers reflected an increase from July but an 8% decrease from August 2018. While 2019 year-to-date market remains positive, the gain is deteriorating and may turn negative before year end as there are a number of reports now showing an overall manufacturing slow down.” “Cutting tool consumption continues to decelerate in-line with the slowing U.S. industrial sector. Robust U.S. manufacturing activity of 2018 has slowed, impacted by uncertain economic growth both here and abroad as well as ongoing trade issues. The weakening economic outlook drives softening industrial production, manufacturing output and business spending. This means that the U.S. benefit from rising inventories is over and inventory liquidation has begun. With industrial production likely to continue to be sluggish for the foreseeable future, most manufacturing has begun an inventory liquidation of short-cycle components. The cutting tool sector is not immune. Cutting tool demand M/M has been volatile for the eight months of 2019; but 2019 YTD gains peaked in January and have continued to soften as the year progressed. August YTD data shows down 8% and we expect cutting tool activity to continue to decelerate – if not contract – for the remainder of 2019 and likely into next year,” said Eli Lustgarten, President of ESL Consultants. The Cutting Tool Market Report is jointly compiled by AMT and USCTI, two trade associations representing the development, production and distribution of cutting tool technology and products. It provides a monthly statement on U.S. manufacturers’ consumption of the primary consumable in the manufacturing process – the cutting tool. Analysis of cutting tool consumption is a leading indicator of both upturns and downturns in U.S. manufacturing activity, as it is a true measure of actual production levels. Historical data for the Cutting Tool Market Report is available dating back to January 2012. This collaboration of AMT and USCTI is the first step in the two associations working together to promote and support U.S.-based manufacturers of cutting tool technology. The graph below includes the 12-month moving average for the durable goods shipments and cutting tool orders. These values are calculated by taking the average of the most recent 12 months and plotting them over time.
Metal Cutting Sector sees Robust Growth in S.E. and N.E., while overall U.S. Manufacturing Technology Orders decrease in August
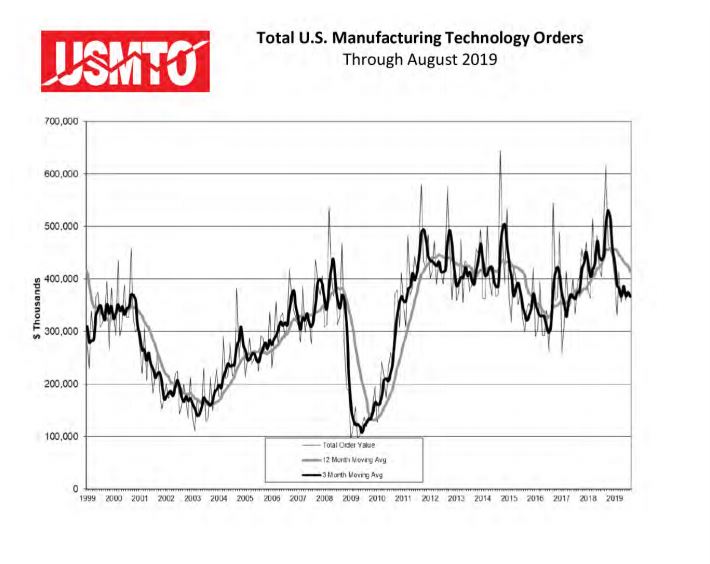
U.S. manufacturing technology orders fell 3.2 percent from the previous month to a total of $365.6 million in August 2019, according to the latest U.S. Manufacturing Technology Orders Report published by AMT – The Association For Manufacturing Technology. Orders decreased 27.6 percent from August 2018, which was the best August on record at $505 million. Orders for 2019 totaled just under $3 billion, a decline of 14.4 percent from the 2018 total to date. Despite the decline over 2018, the total value of manufacturing technology orders in 2019 are the second highest annual total through August since 2014. The Southeast region experienced robust growth driven primarily by orders in the metal cutting category. The Northeast was the only other region to have positive order growth from July to August. The North Central – East had the largest month over month decline, decreasing orders by over a quarter from July. The West and South-Central posted losses while the North-Central-West region was near-flat from over the previous month. “The consensus of analysts at MTForecast is that markets should pick up in the U.S. as early as next summer, and will pick up in Europe several months earlier, taking the pressure off the U.S.,” said Douglas K. Woods, president of The Association For Manufacturing Technology. “This was reflected at EMO Hannover where we saw a great deal of interest on the floor, particularly in the Industry 4.0/IIoT pavilion, but not a high level of capital commitment, reflecting uncertainty and challenges in the European market.” “Looking at Asia, it is likely the Free Trade Agreement with Japan will substantially reduce tariffs on U.S. machine tools imports from Japan, which will require some adjustments. Overall, it should have a positive impact on trade and improve the profitability and opportunities of U.S. agricultural, automotive and aerospace sectors, which could well offset any negative effects of tariffs falling on manufacturing technology imports.” Orders from machine shops were near-flat, yet showed a slight increase over July. Construction machinery manufacturing vastly expanded orders over July. Aerospace orders increased by nearly a third. The automotive sector decreased orders overall despite modest increases from the transmission and powertrain manufacturing sector.