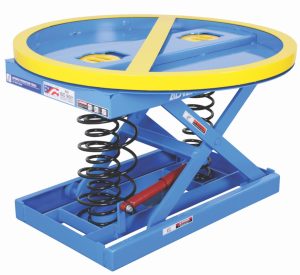
Advance Lifts highlights Palletizer & Self Leveling Lifts
Advance Lifts, a North American manufacturer of industrial scissor lift tables and dock lifts, highlights its comprehensive range of palletizer
Advance Lifts, a North American manufacturer of industrial scissor lift tables and dock lifts, highlights its comprehensive range of palletizer
Latest expansion will further accelerate growth Chamberlain Group (CG), has announced the acquisition of Multi-Fab Products and (MFP-Nova), a global manufacturer,
A U.S. Department of Labor workplace safety investigation has found a Woodbury plastic and resin manufacturer could have prevented a
Italy-based Zallys®, a manufacturer of electric material handling solutions since 1996, has partnered with the new eTug PRO Division of
PAC Machinery, a provider of packaging for more than 60 years, has introduced new bagger accessories and resources that make
Casper, Phillips & Associates Inc. (CP&A) has delivered a presentation to port authorities titled, ‘Peer Review of Container Cranes’, to
Advance Lifts, a North American lift manufacturer of industrial scissor lift tables, is celebrating its 50th anniversary. They are also
Acquisition Expands Miner’s Service Presence Across Central North Carolina Miner Ltd., the dock and door division of OnPoint Group, has announced
Booth highlights will include exclusive demonstrations of the future of elevated structural platforms and SST™ material handling chutes, with individual
Hydraulic Dock Lifts have two advantages over other means of unloading trucks: Level unloading from the bed of a truck
Mezzanine Safeti-Gates, Inc. is expanding its custom engineering design services to meet the growing demand for development. The company has
Orbital wrapper manufacturer TAB Industries, LLC, Reading, Pa., has introduced a Semi-Automatic Upgrade Bundle. Available as an option on the
TAWI, the inventor of the vacuum lift (also known as a vacuum tube lifter) has launched a new, portable vacuum
Orbital wrapper manufacturer TAB Industries, LLC, Reading, Pa., has introduced a Hot Wire Cutting System for its TAB Wrapper Tornado
In this episode of the New Warehouse podcast, we sit down with Nick Rakovsky, the founder of Data Docks, a
Brenton demonstrates the new XCP Series continuous motion, direct load case packer, and its robotic expertise with an integrated line
Continuing to illustrate that no one delivers more, Hyundai Material Handling recently introduced a series of new and innovative products
Orbital wrapper manufacturer TAB Industries, LLC, Reading, Pa has earned another patent for an advance in stretch wrapping. Following a
From January 1, 2024 Interthor will officially go by the name Logitrans A/S, and move even closer to its parent
Orion Packaging Systems is displaying its vast array of stretch and pallet wrapping solutions, including a redesigned MA Series fully