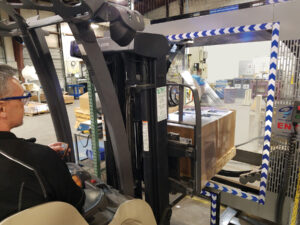
Orbital Wrapper Manufacturer reports 45% increase in smart controls automated wrapping systems
Option on TAB Wrapper Tornado Meets Increasing Demand for Entry-Level Automation Packaging machinery manufacturer TAB Industries, LLC, Reading, Pa., has
Option on TAB Wrapper Tornado Meets Increasing Demand for Entry-Level Automation Packaging machinery manufacturer TAB Industries, LLC, Reading, Pa., has
At ProMat 2023, Ideal Warehouse Innovations will introduce its new line of Air Quality Control (AQC) products, featuring the AtomikAir
The scale servicer, manufacturer, and provider of industrial and commercial-grade weighing scales made the announcement Wednesday Southwestern Scale Company Inc.
TAB Wrapper Tornado allows Penn sheet metal to wrap long pallet loads fast Metal fabrication company Penn Sheet Metal, Allentown,
Rice Lake presents the iDimension Plus XL static dimensioning system, the standard for weighing and measurement solutions for efficiency in
The acquisition brings Miner’s expertise in commercial docks and doors to the Northwest US Miner Ltd., the dock and door
TerraSource Global, a manufacturer of high-quality material sizing equipment based on the Gundlach, Jeffrey Rader, and Pennsylvania Crusher brands, and
Packaging machinery manufacturer TAB Industries, LLC has introduced a dual dispensing system on its TAB Wrapper Tornado orbital wrappers that
APS Resource announces the introduction of its newest innovation, the Vertical Aerial Safety Light which provides an extra layer of
Wolter, Inc. announced the acquisition of Ohio-based dock and door equipment and service provider, Ohio Valley Maintenance LLC, further growing
Orbital wrapping machines in the TAB Wrapper Tornado line from TAB Industries, LLC, Reading, Pa., enable packaging and material handling
Blue Giant Equipment Corporation (Blue Giant) has announced Gerard Biasutto as its Director of Product Management. Gerard began working for
Cherry’s Industrial Equipment has announced the addition of Yarine Velez, an Inside Sales Representative, to its growing Cherry’s Sales team!
Orbital wrapping machine manufacturer TAB Industries, LLC, Reading, Pa.has increased the amount of component parts that are “Made in USA”
Total Control Access design prevents one gate from opening until the opposite gate is closed completely Mezzanine Safeti-Gates, Inc., an
Rice Lake Weighing Systems has launched a new pallet dimensioning system specifically designed for over-length freight. The iDimension LTL XL
Orbital wrapper manufacturer TAB Industries, LLC, Reading, Pa., has unveiled anti-vibration levelers on its TAB Wrapper Tornado line of orbital
Women keeping a handle on the family material handling business Keeping it in the family, Interthor’s Danish parent company, Logitrans,
Innovations in material handling: Working smarter, not harder Manufacturing facilities and distribution centers traditionally had to choose between keeping their
Orbital wrapping machine manufacturer TAB Industries, LLC, Reading, Pa., has updated its online Economic Justification Tool to reflect surging inflation