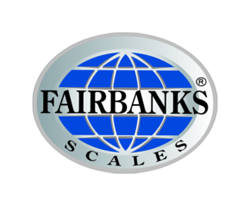
Fairbanks Scales to showcase weighing innovations at Farm Progress Show 2022
Fairbanks Scales Inc., the oldest scale company in the U.S. and the world’s leader in weighing equipment, announces it will
Fairbanks Scales Inc., the oldest scale company in the U.S. and the world’s leader in weighing equipment, announces it will
Orion Packaging Systems, a ProMach brand, is displaying its vast array of stretch and pallet wrapping solutions, including its S-Carriage
Concentric, LLC, the national provider in DC power management and maintenance for the material handling and critical power industries, announced
Miner, the dock and door division of OnPoint Group, has acquired New Jersey Door Works (NJDW), a commercial dock and door company in
Packaging machinery manufacturer TAB Industries, LLC has reported that 90 percent of the TAB Wrapper Tornado orbital wrapping systems purchased
Loading dock doors and all related equipment are part of the backbone of our country’s supply chain. It’s easy to
When it comes to warehouse safety, training is a key piece in building the foundation. That line of thinking was
Fairbanks Scales Inc., the oldest scale company in the U.S. and provider of weighing equipment, has announced they will be
ZLS Series Floor Height Lift Tables from Southworth Products have a pan-style platform that, when lowered, sits essentially flush to
Orbital wrapper manufacturer TAB Industries, LLC, Reading, Pa., has introduced the TWT-20120 Ribbed Stretch Wrap. The strongest grade in the
Ideal Warehouse Innovations launches its new, No Boots on the Ground™ trailer support system for busy loading docks The product innovation
For many years throughout North America, companies have relied on the strength and durability of loading dock equipment from brands
FlexQube announces it has received a $520,000 order for additional material handling carts from Siemens Mobility in the U.S. Siemens
Diamond introduces the EZ35, the industry’s first Installation-Ready Aluminum Shutter Door Diamond Roll Up Doors, a leading designer and manufacturer
On this episode, I was joined by Emily Smith of Kirk Key Interlock Company. Emily is the Segment Marketing Manager
Orbital wrapper manufacturer TAB Industries, LLC has introduced a choice of colored stretch films. Offered as part of its TAB
Uni-Craft Corp. combines the unlimited versatility of Scissor Lifts with the ability to effortlessly rotate and access heavy products for
Vestil Manufacturing Corporation is an industry provider in the production and distribution of material handling equipment featuring over 1,000 different
For assembly or maintenance of large, tall, and/or oddly shaped structures, or anything that requires workers to perform tasks while
Milwaukee-based Arbon Equipment Corporation, a wholly-owned subsidiary of Rite-Hite, has acquired Pugleasa Company, Inc., a loading dock and industrial door