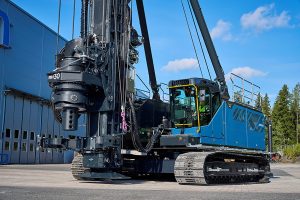
Junttan selects Volvo Penta as engine partner in next-generation equipment
Junttan has partnered with Volvo Penta to power its next-generation machines, starting with the new DR5 drilling rig uniting shared
Junttan has partnered with Volvo Penta to power its next-generation machines, starting with the new DR5 drilling rig uniting shared
Kollmorgen’s new SFD-M (Smart Feedback Device, Multi-Turn) provides machine builders with high-resolution multi-turn feedback and absolute positioning information at system
Aegis Sortation becomes exclusive technology distributor for Johnson Electric in the North American market Johnson Electric has announced an exclusive
Maintenance-Free. Compact. Efficient. Bodine Electric Company introduced 12 new brushless DC hollow shaft gearmotors with hypoid gearing. These type 42B-25H2 and
NORD’s drive solutions provide intralogistics systems with reliable operation, dynamic control, and long service life to effectively operate with greater
The Power Transmission Distributors Association (PTDA), an association for the industrial power transmission/motion control (PT/MC) distribution channel, welcomes three new
Oklahoma resident brings nearly three decades of experience to his role Governors America Corp. (GAC) recently welcomed Jeff Little as
NORD’s drive solutions focus on efficient technology to reduce system variants, lower total cost of ownership (TCO), and reduce energy
Bison Gear & Engineering Corp., a provider in the power transmission industry, announces the Bison Pull-Tight™ gear motor enclosure for
Sulzer has begun the construction of an all-new 7,200 sq. ft. expansion to its Baton Rouge Service Center in Louisiana.
Kollmorgen, a global provider in motion control systems, has announced the new TBM2G series of frameless servo motors, introducing features
Demand for industrial products has risen considerably over the past two decades — and with that, we’ve seen an increase
Compact, energy-efficient drive systems from NORD are designed to be precisely positioned, reduce variants and maintenance, and lower the Total
Piezo Motion’s new partnership with iMotion will expand Piezo’s precision motor technologies and motion control offerings to the Rocky Mountain
New models can test a wide range of motor sizes on a single system SAKOR Technologies Inc., a recognized provider
The new company brings an expanded range of product and digital solutions aimed at helping increase customers’ efficiency and productivity
New Eaton PowerXL™ DM1 micro variable frequency drives help customers increase space savings in multiple environments Offers proven performance efficiency
STXI Motion, a global motion control, and servo solution company, introduces the PRHD2 high-performance permanent magnet synchronous servo motors from
The award-winning products designed to fill the gap between induction and servo motors Bison Gear & Engineering Corp., a provider in the
The company provides immediate access to the most complete NEW heavy-duty offering WAI continues to relentlessly meet the ever-changing needs