PT/MC Industry supports PT WORK Force® Employee Recruitment and Retention Efforts with nearly $280,000 in contributions in 2019
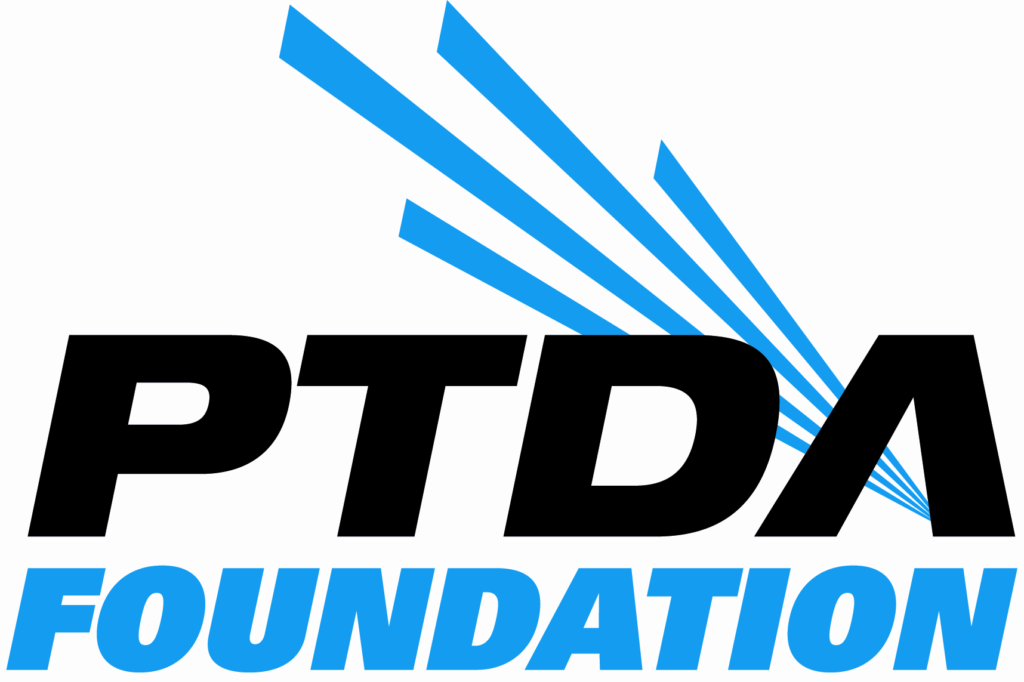
More than 40 percent of power transmission/motion control (PT/MC) employers have no dedicated human resources staff according to a survey completed by PT WORK® Force in early 2019. For these companies, the recruitment and retention activities—essential for growth—are handled by someone for whom HR is not their primary skill set. This challenge is being faced head on by the PTDA Foundation’s PT WORK Force® initiative. And those in the industry are supporting the development of tools and resources with nearly $280,000 in voluntary contributions in 2019. In a video recently release by PT WORK Force®, Keith Nowak, 2019 PTDA Foundation Vice President, MPT Drives, Inc. (Madison Heights, Mich.) captures the immediacy of the recruitment issue. “It is important that we bring in people now to cover for us when we leave. Hiring and retention is crucial and it’s hard. PT WORK Force® can help a company like mine. I don’t have an HR department and I don’t have an HR degree. I need help,” says Nowak. Through its generous support of the PT WORK Force® program and collaboration on research, knowledge and resources, industry employers can compete when it comes to selling our companies and our industry as fantastic places to work with incredibly rewarding career opportunities. A variety of resources have already been developed to help employers in the PT/MC industry hire and retain talent. Watch the video and learn more about these tools at PTWORKForce.org. The PTDA Foundation, whose work is funded solely by donations, was founded in 1982 to enhance knowledge, education, professionalism and productivity within the power transmission/motion control (PT/MC) industry. The Foundation is a not-for-profit, tax-exempt 501(c)(3) corporation; contributions are tax deductible to the full amount allowed by law. For more information, visit ptda.org/Foundation.
Brian Davis (B & D Industrial) and Jos Sueters (Tsubaki of Canada) to lead PTDA in 2020
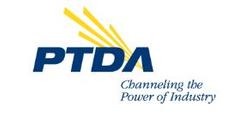
At its annual business meeting during the recent PTDA Industry Summit in Austin, Texas, the Power Transmission Distributors Association (PTDA) elected its 2020 Board of Directors and Manufacturer Council to lead the Association during its 60th anniversary year. Brian Davis, executive vice president/COO, B & D Industrial (Norcross, Ga.), will become PTDA’s president in 2020. Davis has been active in PTDA since 2010 when he joined the Research & Innovation Committee and subsequently served as its chair. Davis has served on the PTDA Board of Directors since 2015. Following his election, Davis said, “It’s a great honor and a little bit humbling to serve as president in 2020. Over PTDA’s 60-year history, the Association has elevated the value the power transmission/motion control distribution channel brings to our end customers. I’m looking forward to working together as a board to continue to achieve our strategic goals on behalf of the industry.” Joining Davis on the 2020 PTDA Board of Directors will be: First Vice President JP Bouchard, vice president, General Bearing Service Inc. (Ottawa, Ontario, Canada) Second Vice President Mike McLain, vice president, Allied Bearing & Supply, Inc. (Harahan, La.) Treasurer Jim Williams, vice president product, Motion Industries Inc. (Birmingham, Ala.) Immediate Past President Jim Halverson, manager power products, Van Meter, Inc. (Cedar Rapids, Iowa) Manufacturer Council Chair Jos Sueters, vice president, Tsubaki of Canada Limited (Mississauga, Ontario, Canada) Manufacturer Council Vice Chair Chester Collier, senior vice president global distribution, Walter Service Technologies (Pointe Claire, Quebec, Canada) PTDA Foundation President Keith Nowak, president, MPT Drives (Madison Heights, Mich.) EPTDA President Zoltan Arkovics, managing director, BDI Europe LTD (Budapest, Hungary) Directors: Michael Cinquemani, president and CEO, Master Power Transmission, Inc. (Greenville, S.C.) Jeff Cloud, president, IBT Industrial Solutions (Merriam, Kan.) Cameron DeBorde, business development, Bearing Distributors, Inc. (Columbia, S.C.) Jim Jeffiers, vice president, Applied Industrial Technologies and Applied U.S. Energy (Cleveland, Ohio) Brian Nowak, president & CEO, Kurz Industrial Solutions (Neenah, Wisc.) Bill Shepard, vice president, BDI (Cleveland, Ohio) Jos Sueters, vice president, Tsubaki of Canada Limited (Mississauga, Ontario, Canada), assumes the duties of the PTDA Manufacturer Council chair in 2020. Sueters has been active in PTDA governance since 2008 when he joined the Canadian Conference Advisory Group. Sueters also served as the chair of the Programs & Products Committee in 2014 prior to joining the Manufacturer Council in 2017. “Since its founding in 1960, PTDA has always focused on bringing distributors and manufacturers together to collectively develop tools that drive more value to our mutual end customers. The Manufacturer Council will continue to work with and support the PTDA Board of Directors as we empower our member companies to be more successful, profitable and competitive,” Sueters said. Joining Sueters on the Manufacturer Council for 2020 will be: Manufacturer Council Vice Chair Chester Collier, senior vice president global distribution, Walter Service Technologies (Pointe Claire, Quebec, Canada) Immediate Past Chair Jeffrey W. Moore, senior vice president, ABB Motors and Mechanical Inc. (Greenville, S.C.) Council Members: Tammy Balogh, vice president human resources, Flexco (Downers Grove, Ill.) Andrew A.O. Brown, vice president, Whittet-Higgins Company (Providence, R.I.) Randy Disharoon, national accounts director, Rexnord Industries, LLC (Milwaukee, Wis.) Maxine Gomez, sales & distribution manager, Belden Universal (Hillside, Ill.) Kristin Jennings, director marketing & industrial distribution, Climax Metal Products Company (Mentor, Ohio) Michael Nisenbaum, director business development, Gates Corporation (Denver, Colo.) Mike Power, national accounts manager, Altra Industrial Motion (Braintree, Mass.)
Rapid reverse engineering
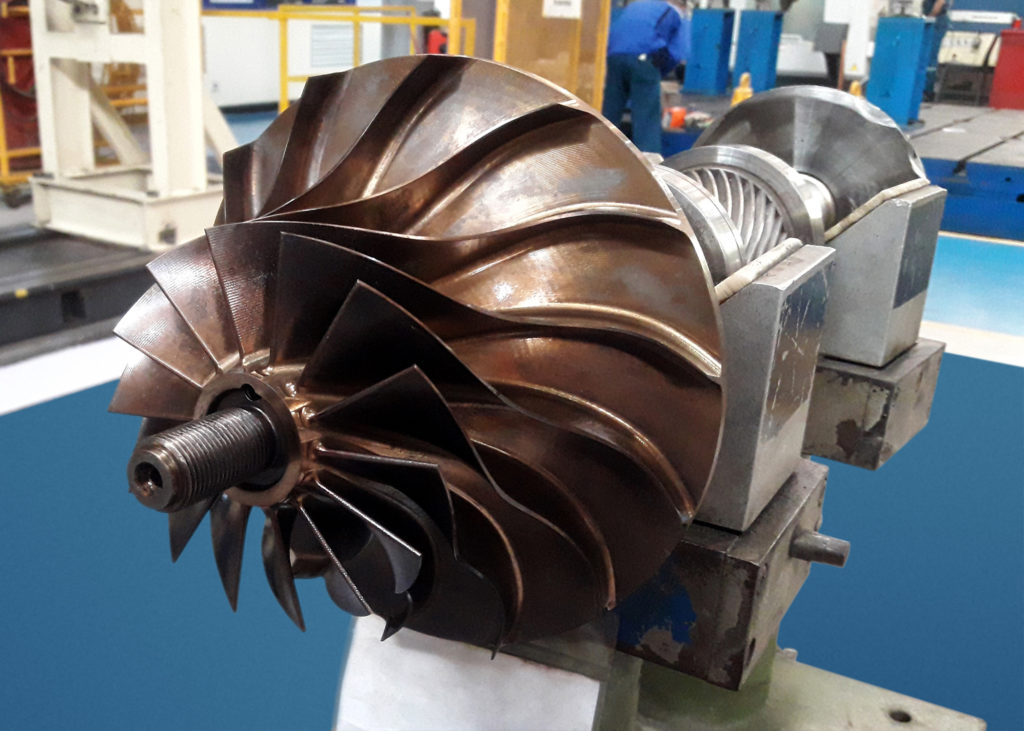
Sulzer reverse-engineers compressor component with 40% cost saving Many industrial processes rely on compressors for a host of essential tasks, from powering machinery to squeezing industrial gases for storage and transportation. When one of its main compressors failed, a company in the Philippines faced high costs and the prospect of a long wait for a critical replacement part. That’s when it turned to Sulzer for help. Modern centrifugal compressors are high-performance machines. Used in the most demanding industrial applications, their job is to deliver air or other gases at high volumes and high pressures into storage, transportation pipework or to downstream machinery. The machines themselves can be very large indeed, consuming hundreds of kW of power, but the critical component at their heart is a precision-engineered high-speed impeller, which can be just a few cm in diameter. For one company in the Philippines, damage to this vital part was to be the cause of a prolonged period of expensive disruption. When a large compressor failed, investigations showed that the machine had been operating out of balance for some time. The resulting vibrations had caused such extensive damage to the machine’s 7.4-inch (188 mm) diameter impeller that the part was beyond repair. With the original manufacturer of the compressor unable to offer a timely or cost-effective replacement, the company approached rotating equipment specialists at Sulzer for a solution. Digital modelling and measurement The damaged impeller and shaft were removed from the casing and shipped to Sulzer’s facility in Indonesia. Once there, the local engineering team set about collecting all the data needed to recreate the part. Using a combination of laser scanning technology and conventional measurements, the team collected digital and dimensional inspection data to build a complete 3D representation of the impeller. The data was then used by Sulzer experts to build a 3D solid model of the replacement component. The damage to the impeller was extensive, so the Sulzer team had few complete surfaces they could use as a basis for their model. By applying engineering analysis to the geometry of the broken part however, they were able to “undo” the damage digitally and determine the precise geometry of the original component. While the experts were working on the geometry, their colleagues were continuing their own work to reverse-engineer the component. They used x-ray fluorescence (XRF) analysis to establish the exact chemical composition of the impeller. That allowed Sulzer to source the same alloy in order to manufacture the replacement. Finally, the team used zebra analysis to determine the surface continuity quality in the 3D model that would affect the surface finish required for the new part during the machining process. Machining expertise With the model, material and relevant manufacturing information now available, it was time for Sulzer’s CNC machining specialists to step in. A manufacturing team in Houston produced the replacement part, which was machined from a single block using five-axis milling techniques. After surface finishing, the part was spin tested at high speed in Houston to check for any imbalance before shipment to Indonesia. The Indonesian team assembled and balanced the new impeller on the original shaft before returning it to the customer for installation in the machine. “This project shows Sulzer’s global capabilities at their best,” says Hepy Hanipa, Head of Turbo Services South East Asia. “This was a relatively small, but highly complex component and its performance was critical to our customer’s operations. Close cooperation between Sulzer teams working on opposite sides of the world allowed us to deliver a high-quality solution on a timescale that met the customer’s needs whilst delivering a 40% cost saving.”
Sakor will exhibit engine, hybrid and electric vehicle and battery testing technologies
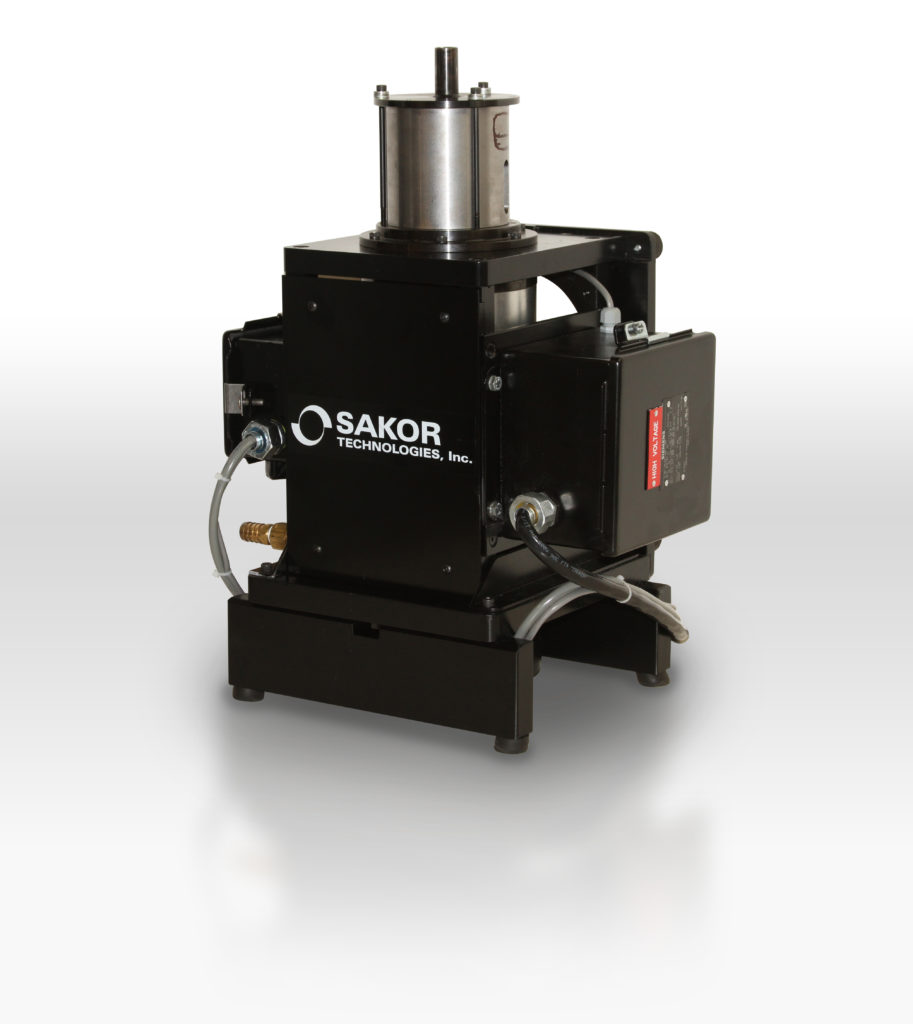
Sakor Technologies Inc., a recognized leader in the area of high-performance dynamometer systems, announces that it will be exhibiting at the Automotive Testing Expo North America 2019, October 22-24, 2019 at the Suburban Collection Showplace in Novi, Michigan. SAKOR will be highlighting many of their innovative technologies at Booth #10009, including hybrid and electric vehicle testing, high voltage battery testing and simulation, and the smallest AC regenerative engine dynamometer available in the industry. SAKOR technical experts will be on hand at the booth to offer expertise and answer questions about their products. An industry leader in developing testing technology for hybrid and electric vehicles, SAKOR has extensive experience in electric motor and generator testing, as well as engine and powertrain testing. The DynoLAB™ Test Cell Control System being highlighted can perform a wide variety of road load profiles and simulations, and is designed for testing to all international standards, including existing and proposed EPA, CARB, and Euro standards. The High Voltage Battery Simulator/Testing System is ideal for customers conducting research and development, performance evaluation, and durability testing of high voltage DC power systems. It can be used for testing high voltage batteries as well as simulating high voltage batteries while testing hybrid and electric vehicle drive lines and inverter systems. The High Voltage Battery Test System is fully line regenerative, resulting in a very power efficient unit, minimizing electricity usage, lowering operating costs, and providing an extremely environmentally friendly “green” profile. The Small Engine AC Motoring Dynamometer on display is the smallest available on the market today. Featuring ultra-low inertia properties, the unit can convert easily between horizontal and vertical orientations, accommodating either shaft orientation. It was developed specifically to meet the needs of small engine manufacturers who must comply with engine testing procedures required by 40 CFR Part 1065 emission standards. This innovative machine can test both steady state and transient emissions cycles, and allows users to avoid the issues associated with larger dynamometers, such as breaking of drive-shafts or couplings.
Cummins invests in fuel cell technology firm Loop Energy
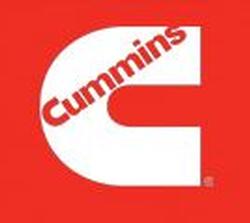
Loop Energy, a provider of fuel cell electric range extenders for medium- and heavy-duty transport applications, announced that it received a cash investment from Cummins Inc. Loop Energy, a provider of fuel cell electric range extenders for medium- and heavy-duty transport applications, announced that it received a cash investment from Cummins Inc. Hydrogen fuel cells are gaining interest from transportation industry leaders as they facilitate the transition from vehicles running on fossil fuels to sustainable electric solutions. In commercial transport applications, fuel cell range extended vehicles emit no greenhouse gas or pollutant emissions and there is no impact to vehicle payload weight, power demands or refueling time compared to battery-only systems. The quantity of the investment was not disclosed. Earlier this month, Cummins completed a $290 million acquisition of Mississauga, Ontario, Canada-based fuel-cell and hydrogen-production technology company Hydrogenics Corp. Cummins acquired an 81-percent share in Hydrgenics. Also a Canadian company, Loop Energy is based in Burnaby, B.C. “Cummins investment in Loop Energy affirms the positioning of our company and technologies to meet the demand for a cost-effective alternative to the internal combustion engine in commercial trucking,” said Ben Nyland, president and CEO of Loop Energy. “This new investment by Cummins is solid evidence of the traction we are gaining in the market through investments, customer orders, and vehicle demonstration programs.” Loop Energy will also supply Cummins with range extender systems for incorporation into demonstration trucks. Loop’s n-compromise module provides a breakthrough in terms of cost and power density, allowing truck operators to transition to zero emissions without an impact to cost of ownership. “Cummins is investing in a broad portfolio of power solutions, including advancements in hydrogen fuel cell technologies and the electrification of commercial applications,” said Thad Ewald, vice president of corporate strategy, Cummins. “This investment is continued evidence of our commitment to next-generation trucking technologies, and we look forward to working with Loop Energy to further validate the provision of zero-emissions fuel cell rage extenders for customers.”
J W Winco offers Oil and Water Repellent Membrane
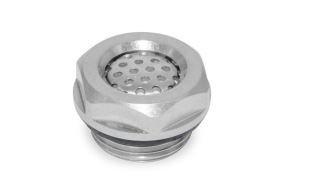
With a pore size of 1.2 µm, oleophobic and hydrophobic membranes GN 7404 provide reliable aeration and ventilation, allowing no dirt particles or droplets of oil or water to pass through the membrane In order to compensate for pressure differences in both directions, JW Winco already offers various aeration and ventilation elements with integrated filters and sieves. As a new change to its product line-up, JW Winco now also offers elements equipped with membranes alongside these standard parts. This makes it possible to prevent even smaller particles and, above all, oil and water droplets from passing through the ventilation openings. Dirt and moisture are kept away from the inside of the housing, and lubricants such as oils cannot escape. While the previous filter and sieve elements have a minimum mesh size of 100 µm, the standard membrane pores are only 1.2 µm in size. Externally, the robust membrane is additionally protected against mechanical stress by a protective sieve made of stainless steel. Ideally, the standard part GN 7404 should be installed in vertical surfaces so that no liquids can collect on the membrane, which could impair the pressure balance. At a nominal differential pressure P1 to P2 of 1 bar, the maximum air flow – depending on the diameter – is up to 34 l/min. The membrane even retains its function up to an external pressure differential of 2 bar or an internal pressure differential of up to 10 bar. The maximum operating temperature is 100 °C. The membranes themselves are made of a nylon fleece impregnated with an acrylic copolymer, and although the fibers are wetted, the porosity remains unchanged and can range between 0.2 and 10 µm if desired. Using a special process, the membrane is robustly bonded to a plastic ring socket by injection molding so that it can be firmly inserted into the stainless steel or aluminum screw fittings, sealed by an O-ring.
KASTO: Success runs in the family
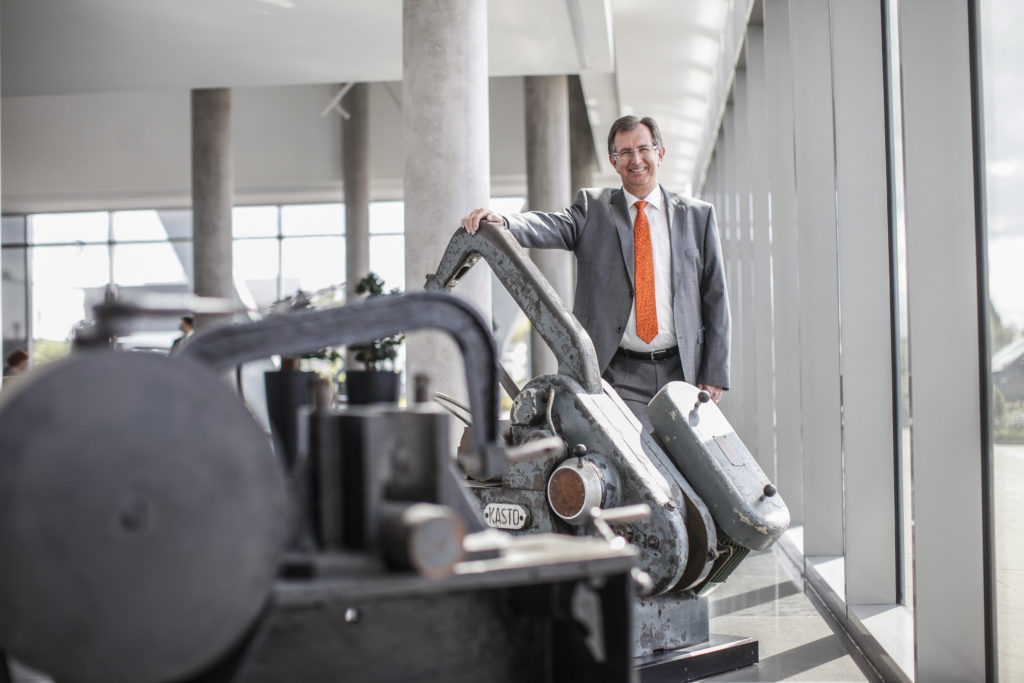
KASTO has been around for 175 years – making the sawing and storage technology specialist one of the oldest family-owned businesses in the whole of Europe. The company’s history is closely bound up with that of its founders, the Stolzer family, which is still responsible today for ensuring that KASTO remains faithful to its traditions while keeping its eyes fixed firmly on the future. Despite all his clarity of vision, when carpenter Karl Stolzer set up his own workshop in the town of Achern in Baden-Wuerttemberg in 1844, he could hardly have imagined that it would one day become the world’s leading supplier of metal sawing machines and automatic storage systems. And he would probably also have been astonished to think that today, 175 years later, his great-great-grandson would be guiding the company’s fortunes. However, this success is no accident. Instead, it is the result of entrepreneurial vision and a keen understanding of the market’s needs. Both these qualities characterise the entire history of KASTO and the Stolzer family. The carpentry shop soon developed into a manufacturer of machines that were driven by the water power of the streams of the Black Forest. By building water-powered and then subsequently industrial sawmills, Karl Stolzer laid the foundations for the company’s continued success. After his death in 1891, his son Carl took over at the head of the company. Carl Stolzer attended the first years of study at the recently founded Esslingen mechanical engineering college and manufactured roller gang saws for sawing wood in his company. He was succeeded by his son, Friedrich Stolzer, who further developed the production of roller gang saws and sawmill equipment and was awarded a patent for his innovations. The step to becoming a modern machine manufacturer Friedrich Stolzer died in 1941, after which his wife Anna took over the running of the company until the couple’s two sons, Friedrich and Paul, had completed their training. The entry of the two brothers into the company brought about a gradual shift towards the metal-sawing business. The invention of the hack sawing machine by Paul Stolzer in 1947 was a decisive step in the company’s transition into a modern machine tool manufacturer. The following years ushered in numerous new developments such as circular saws and bandsaws, as well as cassette and cantilever arm stores for long goods whose underlying principles are still used today. The current Managing Partner, Armin Stolzer, joined the company in 1984. Even as a young man, he gathered experience of extensive large-scale projects, drove the further development of technologies and, among other things, was responsible for introducing the first CAD system at KASTO in 1986. He also worked hands-on in the machine design sector and maintained customer contact at customer sites and during service operations. During the two major economic crises at the start of the 1990s and end of the 2000s, Armin Stolzer showed himself to be a reliable helmsman who steered the company successfully even in the troubled waters of the times. He is now actively supported in this task by his wife Ruth Stolzer. She is a fully qualified lawyer who previously acted as a judge and is now responsible for the Legal and Human Resources departments, a range of administrative tasks as well as for a number of foreign branches. Together, they founded the Armin and Ruth Stolzer Foundation, which is committed to social projects, pre-school and school education, as well as technical further developments. The next generation on the Management Board And the next generation has already been helping to guide the company’s fortunes for several years as members of the KASTO management board: Nicole Krebber-Stolzer and her husband Sönke Krebber both trained as engineers at Darmstadt Technical University and share responsibility for technical areas such as purchasing, production, assembly, research and development, logistics and factory maintenance. Stephanie Riegel-Stolzer joined the company in 2011 and, like her husband Jonathan Riegel, graduated with a master’s degree in business studies at the University of St. Gallen. They are responsible for service, marketing, finance, controlling and internal IT and also share responsibility for sales and the foreign branches with Ruth and Armin Stolzer. As a result, even 175 years after it was founded, KASTO is still secure in the hands of the same family. This fact is clearly reflected in the company’s philosophy, which is characterised by flat hierarchies and open doors. For KASTO, a high level of social responsibility towards the company’s employees and their family members is self-evident. The company works hard to promote occupational training and offers attractive development opportunities to its many young employees. The KASTO Management Board also actively strives to bring women into technical positions. Regular celebrations and events for employees improve the community spirit in the company and bring about a feeling of togetherness – an important factor in ensuring that the family-owned company KASTO continues to be successful in the future.