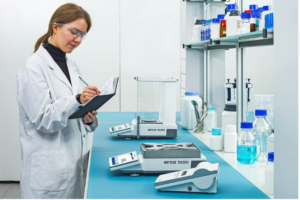
METTLER TOLEDO launches new generation of laboratory balances
METTLER TOLEDO positions itself at the forefront of laboratory weighing when it comes to simplicity, performance, and robustness. With the
METTLER TOLEDO positions itself at the forefront of laboratory weighing when it comes to simplicity, performance, and robustness. With the
Confidential and complimentary, new GHS L.A.B.E.L. Profile helps companies labeling hazardous chemicals follow compliance best practices. Reliance Label Solutions, which
Company also will emphasize its recently launched DIAMIND ecosystem, a portfolio of interconnected software and hardware systems for comprehensive traceability.
The recently-elected 2024 Board of Directors and Manufacturer Council of the Power Transmission Distributors Association (PTDA) begin their leadership terms.
CHEP, a supply chain solutions, announced the appointment of Xavier Garijo as the CEO of Americas effective Jan. 1, 2024,
Seaga Manufacturing, Inc. (“Seaga”), a platform for innovative Automatic Retail Dispensing and Modular Intelligent Inventory Control Solutions, serving the Food
In this episode I was joined by Theresa Lee who is a product manager at Toshiba. Theresa is involved in