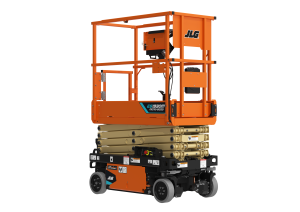
New ES1930M micro-sized scissor lift by JLG
Compact, lightweight, maneuverable, and built for productivity JLG Industries, Inc. has announced its entry into the fast-growing micro-sized scissor lift
Compact, lightweight, maneuverable, and built for productivity JLG Industries, Inc. has announced its entry into the fast-growing micro-sized scissor lift
Streamlining aftermarket support for North American customers JLG Industries, Inc., an Oshkosh Corporation business and a global manufacturer of mobile
Efficient, air-powered lifting solutions for diverse industrial applications Advance Lifts, a North American manufacturer of industrial scissor lift tables and
Durable and adjustable lifting solutions for elevated work applications Advance Lifts highlights its Work Access Platform Lifts, engineered to deliver
Durable and adjustable lifting solutions for elevated work applications Advance Lifts highlights its Work Access Platform Lifts, engineered to deliver robust,
All-Electric Lift offers seamless integration with linear speeds, unlimited number of stops, and zero obstructions under the platform Advance Lifts
Optimize workflow efficiency with versatile and reliable container dumping solutions Advance Lifts continues to offer cutting-edge solutions with its comprehensive Container
The performance requirements of lift tables in a production process are far greater than those of stand-alone lifts. To ensure
Motorized turntables allow products to be rotated safely and more accurately Advance Lifts, a North American manufacturer of industrial scissor
An extension of the popular ZLS line of floor height lifts, the new ZLS-T from Southworth is a combination lifter
Durable Lift for travel food processing applications with limited available platform length Advance Lifts, a North American manufacturer of industrial
How to get personnel and material from ground level to mezzanine level quickly, safely, and efficiently Scissors lifts have been
Southworth Products Corp has announced a new program to provide fast delivery of several models of lift tables and other
For applications that require frequent cycling (lifting and lowering) of lift tables, Southworth offers high-duty cycle packages that increase recommended
The new LiftMaster 7000 from LiftWise allows users to lift or lower a variety of parts into position for maintenance
ZLS Series Floor Height Lift Tables from Southworth Products have a pan-style platform that, when lowered, sits essentially flush to
Blue Giant Equipment Corporation has just announced that Ron Mack has been appointed as Sales Manager for Lift Tables. Ron
Orion Packaging Systems, a ProMach brand, is exhibiting updated features on its Flex LPA Automatic Turntable Pallet Wrapping System in
Gravity flow solutions manufacturer connects the Gravity Conveyor Dots to improve warehouse flow and workplace safety — Rotate, Transfer, and
A key issue in the mold manufacturing industry is handling. Having to move, lift and position such large, heavy, and