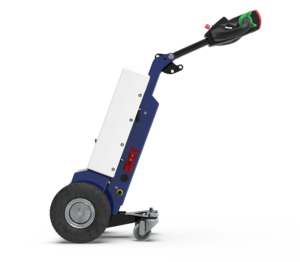
Zallys® Electric Material Handling partners with eTug PRO for North America launch
Italy-based Zallys®, a manufacturer of electric material handling solutions since 1996, has partnered with the new eTug PRO Division of
Italy-based Zallys®, a manufacturer of electric material handling solutions since 1996, has partnered with the new eTug PRO Division of
Lift’n Buddy LNB-2 two-wheel hand trucks from Presto ECOA take mobility to a new level. They combine the convenience, versatility,
From January 1, 2024 Interthor will officially go by the name Logitrans A/S, and move even closer to its parent
Autoquip Corporation is celebrating its 75th anniversary of providing innovative lifting solutions to the material handling industry. The company was originally
Manual push stackers from Presto Lifts are ideal for a wide variety of light industrial, warehousing, and retail back-room applications.
ZLS Series Floor Height Lift Tables from Southworth Products have a pan-style platform that, when lowered, sits essentially flush to
FlexQube announces it has received a $520,000 order for additional material handling carts from Siemens Mobility in the U.S. Siemens
The Danish owner-managed company, Interthor Inc./Logitrans A/S, which for many decades has excelled in the global market for material handling
Creform Corporation has designed and built a compact AGV with the fabricated cart that provides a manufacturer with the ability
Creform Corporation, a manufacturer of unique products for the design and building of material handling structures and AGVs will showcase
The warehousing industry is ready for incoming deliveries from abroad, but nothing is coming due to post-Brexit customs delays, says
Creform Corporation, a manufacturer of unique products for material handling and commercial structures has designed and built a kitting cart
The Raymond Corporation and K.Hartwall, a global provider of logistics solutions located in Finland, announce an exclusive partnership in the
¾ XZ Series Lift Tables from Presto ECOA feature Zero-Height platforms that sit just 3/8” above the floor. This extreme
The PalletPal Walkie from Southworth Products is an automatic pallet load leveler that mounts on to any standard electric walkie
Magline, Inc., manufacturer of innovative material handling equipment, has added the Powered Lifting Hand Truck to the family of powered products.
New economical cart designed for mobile computing or light barcode printing provides ROI in about three months Newcastle Systems, a
Canadian company Bombardier Recreational Products Inc. (BRP) with brands like Ski-Doo (snowmobiles), Lynx (snowmobile), and Sea-Doo (personal watercraft) has placed
FlexQube Inc. hires, starting January 4, 2021 Michael Gore as Sales Manager for North America. Michael Gore has 35 years
New features improve performance, safety, maintenance, standardization, and energy efficiency while lowering the total cost of ownership Stoecklin Logistics, a