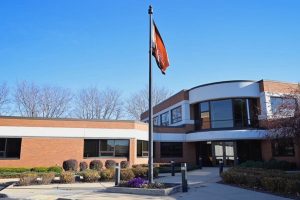
Caldwell purchases Beloit office building
The 53,000-square-foot building becomes the material handling and lifting equipment manufacturer’s third facility, with two existing sites in nearby Rockford,
The 53,000-square-foot building becomes the material handling and lifting equipment manufacturer’s third facility, with two existing sites in nearby Rockford,
R&M Materials Handling distributor, Specht Industries, has installed bridge cranes and hoists at a manufacturer of customized autoclave systems in
Kito Crosby has announced Jason Bulan has been promoted to Vice President of Business Development & Product Strategy, for its
The manufacturer of davit cranes and industrial lifting equipment is further supporting the initiative by allowing a dog trainer to
The manufacturer of davit cranes and industrial lifting equipment was inaugurated on December 4, 2004, with two staff; today, it
The Manitowoc Company, Inc. has announced that it was recognized as one of the 2024 “Best for Vets” Employers by
All-Electric Lift offers seamless integration with linear speeds, unlimited number of stops, and zero obstructions under the platform Advance Lifts
Kito Crosby introduces the addition of Harrington brand hazardous location electric chain hoists to their three-phase electric chain hoist line.
JLG Industries, Inc., a manufacturer of mobile elevating work platforms (MEWPs) and telehandlers, named Rogerio dos Santos Vice President EMEAI Region
The Ocean Cleanup, a global nonprofit, and Kito Crosby, an international manufacturer in the lifting and securement industry, just announced
All Material Handling (AMH) is expanding its product offering with a new range of stainless-steel lifting chains and fittings. The
Forklift-International.com, the online marketplace for material handling equipment, has announced a major milestone for its U.S. operations. The platform currently
Hy-Brid Lifts announced that Charlie Haskin will be the director of sales covering the western United States. Haskin’s responsibilities include
Zero fuel and zero emissions for work in quieter, more sensitive environments JLG Industries, Inc., an Oshkosh Corporation business and
A new transatlantic partnership is bringing the benefits of superior safety hoists to the US market Atlas Lifting & Rigging
OZ Lifting Products LLC will exhibit at the Water Environment Federation’s Technical Exhibition & Conference (WEFTEC) on October 5-9, 2024,
Optimize workflow efficiency with versatile and reliable container dumping solutions Advance Lifts continues to offer cutting-edge solutions with its comprehensive Container
Kito Crosby introduces the newly engineered Crosby G-2160 Wide Body Shackle. From the manufacturer that introduced the original wide body
Kito Crosby announces the launch of the Crosby Straightpoint Self-Indicating Dynamometer (SID) – designed to replace outdated mechanical products. The
Kito Crosby has announced its Lifting for the Troops campaign for 2024, supporting the Children of Fallen Patriots Foundation. Fallen Patriots provides