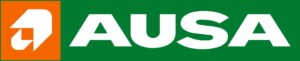
AUSA acquisition complete and is now part of JLG
JLG Industries, Inc., an Oshkosh Corporation business and a global manufacturer of mobile elevating work platforms (MEWPs) and telehandlers, announces that
JLG Industries, Inc., an Oshkosh Corporation business and a global manufacturer of mobile elevating work platforms (MEWPs) and telehandlers, announces that
Rope and Sling Specialists Ltd. (RSS) will return as a lead sponsor and take a new exhibit to LiftEx 2024,
The Caldwell Group Inc. has hired Steve Mueller as regional sales manager. It is the second time the below-the-hook and
Innovative light, flexible, and ergonomic crane systems for safer and more productive workplaces, further expanding and enhancing Kito Crosby’s installed
The world’s largest producer of spirits is now benefiting from a turnkey package of three Italkrane ATEX-rated electric chain hoists
Tele Radio has reminded the industry of the benefits of two handheld radio remote controls specifically for the demands of
Today, the Manitowoc Company, Inc. reported a second-quarter net income of $1.6 million, or $0.04 per diluted share. Second-quarter adjusted
The hoist clamp presents a quick, easy, and safe way to hang any of the company’s electric chain or manual
The Caldwell Group Inc. has named Sarah Stitt product manager of the Rockford, Illinois-based company’s RUD range. The below-the-hook and
Wolter Inc.‘s first acquisition of a manufacturing company was Cincinnati Crane & Hoist (CC&H), a crane and hoist manufacturer based
Dynamic Load Monitoring (UK) Ltd. (DLM), of Southampton, has revealed its plans for a ” bigger and better” Global Lifting
On Monday, July 8, 2024, Beryl made landfall in Texas as a category one hurricane, bringing heavy winds, flash flooding,
The Lifting Equipment Engineers Association (LEEA) has revealed more plans for Global Lifting Awareness Day (GLAD) on July 18th. A
OZ Lifting Products LLC is offering wireless options for its electric chain hoist and builder’s (wire rope) hoist. The hoists
Recognized as a top-ranked company in the Washington D.C. area for its unique Workplace Culture JLG Industries, Inc., a global
Innovative updates inspired by customer requests JLG® Industries, Inc. has introduced the all-new SkyTrak® 8042 telehandler, remastered to maintain the
Unirope Ltd. president Justin Brown has been nominated to the board of the International Organization for the Study of Ropes
The Lifting Equipment Engineers Association (LEEA) has moved products, inspection, and training to the front of its Global Lifting Awareness
Casper, Phillips & Associates Inc. (CP&A) has delivered a presentation to port authorities titled, ‘Peer Review of Container Cranes’, to
OZ Lifting Products LLC has launched North America’s first stainless steel lever hoist, in 0.25- to 3-ton capacities. The hoist is