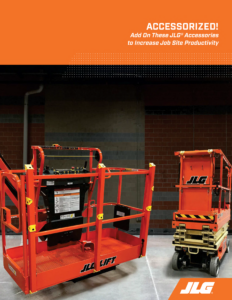
JLG publishes new Accessories Resource Guide on #DirectAccess
JLG Industries, Inc., a global manufacturer of mobile elevating work platforms (MEWPs) and telehandlers, has released its new resource guide Accessorized
JLG Industries, Inc., a global manufacturer of mobile elevating work platforms (MEWPs) and telehandlers, has released its new resource guide Accessorized
Skyjack division announce the retirement of Skyjack President Ken McDougall, and subsequent appointment of Charlie Patterson as President, effective January
Magni Telescopic Handlers announced Altorfer Rents is now part of the Magni dealer network. Altorfer’s addition will bring Magni’s full
Big Joe’s new CB30/CB35 Walkie Stackers offer a next-gen alternative to sit-down forklifts Big Joe Forklifts has officially introduced the
JW Winco has expanded its product range with two compact and robust angular gear boxes that translate rotational movements by
DT Engineering is a specialist manufacturer of overhead cranes and hoists. The DT Digital Trident System is a state-of-the-art product,
This year’s Global Lifting Awareness Day, which takes place on July 13th, will kick-off with an event at UK Parliament
The new straight-boom compact crawler lift model is now available JLG Industries, Inc. introduced its first straight-jib (SJ) compact crawler
Effective June 5, 2023, H&E Equipment Services Inc. (H&E) announces the opening of its Houston South branch, its 22nd rental
The Crosby Group announces the launch of the Crosby Straightpoint LoadConnect cloud-based software, which can monitor loads from any distance
The Caldwell Group Inc. has expanded its series of RUD ACP-Turnado lifting points, with Max and Supermax versions. Caldwell partners
Techlift International has acquired Chariots élévateurs GCS, thus becoming its fourth branch. With branches in Drummondville, Victoriaville, Sherbrooke and now Montreal,
Casper, Phillips & Associates (CP&A), based in Tacoma, USA, has seen a rise in demand for its engineering design services,
First-Quarter 2023 Highlights Net sales of $508.3 million, up 10.7% year-over-year Diluted net income per share of $0.46, up $0.37
Company’s new two-way fleet management and communications platform coming soon JLG Industries, Inc. has offered a first look at the
Dialight announced the availability of its newest fixture, the DC Crane Vigilant High Bay, designed to specifically meet the needs
Global Lifting Awareness Day—#GLAD2023—has arrived at the point of use, as July 13th draws nearer. Driven by the Lifting Equipment
When K2 Marine was searching for a lifting device to solve the issue of flipping their boat parts once they
Fast charging capability maximizes uptime and productivity; Available for order online at the MyToyota Store Toyota Material Handling has recently
TNT Crane & Rigging LLC (TNT), the largest open-shop crane services platform in North America, has announced that its Board of