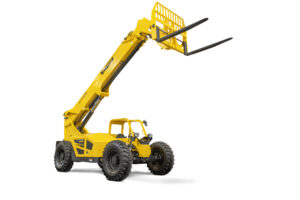
Pettibone hits 15,000-pound-capacity benchmark with new Extendo 1544X Telehandler
Pettibone brings its X-Series telehandler lineup to the 15,000-pound lifting class for the first time with the introduction of the
Pettibone brings its X-Series telehandler lineup to the 15,000-pound lifting class for the first time with the introduction of the
Barcelona, Spain-based Elebia Autohooks has launched eLINK, a central control system for its range of automatic hooks and rigging products
Winona, Minnesota-based OZ Lifting Products LLC has launched the Aluma-Lite series of ultra-portable davit cranes, available in 500 lbs. and
Two market leaders have joined forces to broaden JLG’s product portfolio JLG Industries, Inc., an Oshkosh Corporation company and a
The Crosby Group, a provider of lifting and rigging solutions, and KITO CORPORATION, a manufacturer of material handling equipment with
Lifting industry PR company Bridger Howes Limited (BH) has named Jenny Eagle PR and communications manager Eagle, formerly editor of
The fourth Global Lifting Awareness Day—#GLAD2023—will take place on Thursday. July 13th. Powered by the Lifting Equipment Engineers Association (LEEA)
The ALL Family of Companies is once again an authorized dealer for Maeda mini cranes. ALL is also adding 13
Emissions-free lithium-ion battery with a dependable diesel engine to work anywhere JLG Industries, Inc., an Oshkosh Corporation company and a
GM Equipment Rentals, an aerial and material handling company based in North Central Pennsylvania, has completed its acquisition of Magnum
VRCs help maximize existing space, while also costing less than dealership expansion It’s no surprise that constructing a new dealership
Combined, the companies accumulated 16 awards and honors this past year JLG Industries, Inc., an Oshkosh Corporation company and a
The Crosby Group, a manufacturer of rigging, lifting, and material handling hardware and equipment, has concluded its 2022 Rigging for
Terex Corporation has announced that Stacey Babson Kaplan has been promoted to Senior Vice President, Chief Sustainability and Compliance Officer
Associated Wire Rope Fabricators (AWRF) has named The Caldwell Group Inc.’s Director of Business Development Jeff Ferchen to the board
The Caldwell Group Inc. has unveiled a new online tool, where channel partners can access pricing and availability information online.
Hoist & Winch Ltd has recently completed a challenging project for one of the UK’s biggest construction companies involved in
US Service Group LLC, a New York-based industrial services company, has acquired the assets and operations of Dalton Rigging and
JLG Industries, Inc., an Oshkosh Corporation company and a global manufacturer of mobile elevating work platforms (MEWPs) and telehandlers, introduces an
Overhead cranes from R&M Materials Handling, Inc. have provided a cost-effective and more reliable solution for a producer of stainless