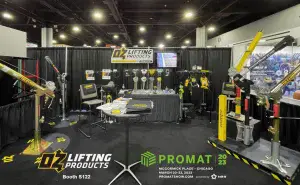
OZ Lifting unveils ProMat 2023 showcase
OZ Lifting will show a variety of davit cranes, hoists, and lifting components at ProMat 2023, which takes place March
OZ Lifting will show a variety of davit cranes, hoists, and lifting components at ProMat 2023, which takes place March
Builds on Successful 12-Year Partnership with JLG; Broadens Product Portfolio Oshkosh Corporation, an innovator of mission-critical vehicles and essential equipment,
Oshkosh Corporation companies JLG Industries, Inc. and Jerr-Dan Corporation, LLC have hired Sara Vincent as the new Director of Marketing for
Raimondi Cranes presented three new products at Bauma 2022, and welcomed thousands of guests over the course of the event. The
Sales of $1.1 billion increased 13% year-over-year, 21% on FX neutral basis Total backlog grew 33% year-over-year to $3.9 billion
H&E Equipment Services, Inc. just announced results for the third quarter that ended September 30, 2022, citing record results for
SAIA recognizes achievements for innovative access technologies, including the world’s tallest hoist tower The Scaffold & Access Industry Association (SAIA),
With an industry-leading elevated height of 456 inches, the new Raymond® High-Capacity Orderpicker boosts storage capacity as e-commerce demands increase
The British firm with the world’s most sophisticated scaffolding system has won more than £6m in orders from e-commerce giant
TAWI, the inventor of the vacuum lift (also known as a vacuum tube lifter) has launched a new, portable vacuum
WIKA Mobile Control has introduced the qSCALE I2 TH rated capacity indicator (RCI). The qSCALE I2 TH RCI system was
Qimarox introduces a vertical conveyor for AMRs Qimarox, a manufacturer of components for material handling systems, introduces a vertical conveyor
Casper, Phillips & Associates Inc. (CP&A) has completed a structural design review on a mega 3,500-tonne capacity double boom offshore
OZ Lifting Products LLC has added a 0.25-ton capacity manual chain hoist and trolley to its ever-growing stainless steel range.
Rockford, Illinois-based The Caldwell Group Inc. will lead a series of initiatives this fall to raise money for breast cancer
Enhances job site safety through alarms and limited machine functionality JLG Industries, Inc., an Oshkosh Corporation company and a global
SC1000 Relevation™ is the first and only battery-powered traction hoist on the market Spider, part of BrandSafway’s Motorized Manufacturing Group,
Effective September 21, 2022, H&E Equipment Services Inc. (H&E) announces the opening of its Hollywood rental branch, its 10th in
The Marine Travelift/Shuttlelift/ExacTech, Inc. family of companies has announced the promotion of Kurt Minten to Executive Vice President of Marine
Elevating Worker Platform Lifts from Presto ECOA are the perfect solution for assembly, repair, or maintenance of large or tall