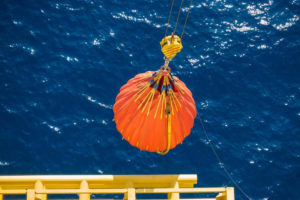
Bally Ribbon Mills offers custom-designed woven materials for critical rigging and tie down applications
Lightweight two- and three-dimensional reclaimable materials offer strength and resistance Bally Ribbon Mills (BRM), an industry provider in the design,