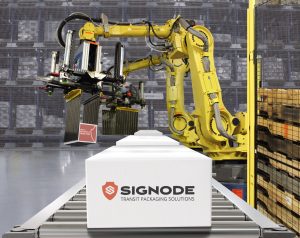
Signode to Feature New Innovations and Complete Packaging Solutions at PACK EXPO 2025
Signode is highlighting its integrated solutions and new packaging innovations at PACK EXPO 2025. Held at the Las Vegas Convention
Signode is highlighting its integrated solutions and new packaging innovations at PACK EXPO 2025. Held at the Las Vegas Convention
Plastics Industry Association (PLASTICS) Chief Economist, Dr. Perc Pineda, has released a new U.S. economic analysis, highlighting steady consumer demand
Delivering unmatched quality, service, and reliability across industries Amerikooler is offering the best products and services in the industry, redefining
The Plastics Industry Association (PLASTICS) applauds Chairman Jason Smith (R-MO) and the House Ways and Means Committee for advancing tax
Increases plant efficiency with rebuilds & upgrades HAVER & BOECKER offers customers increased packing equipment longevity and return on investment
Datalogic has announced the launch of the PowerScan 9600 RFID, a revolutionary addition to its best-selling range of handheld industrial
A new report from AMERIPEN, prepared by Circular Matters and funded by PLASTICS’ Recycling is Real initiative, highlights significant progress by consumer packaged goods (CPG) companies toward recycled
A&R Bulk-Pak’s Moncks Corner, SC location is one of the first OCS Logistics Verified Facility in the U.S. and the
The Plastics Industry Association (PLASTICS) announced the winners of its 2025 Plastic Sustainability Innovation Awards, recognizing outstanding innovations in plastics manufacturing
The ‘Golden Rule’ college scholarship program is offered by the Nelson-Jameson Foundation Nelson-Jameson has announced Sophie Kempe as the winner of
As industries across the globe increasingly focus on reducing packaging materials, Columbia Machine continues to innovate with solutions that balance
Optimizes valve bag packing Packing operations across the globe in the cement, building materials and food industries experience significant flexibility
Food processing distributor’s new Fairview, Pa., facility enhances capabilities and customer service in the Northeast Region Nelson-Jameson has announced a
Welcome to another episode of The New Warehouse Podcast, recorded live at Manifest 2025. In this episode, Kevin speaks with Shelly
SeaCube Containers has introduced the SeaCube cold solution, a portable cold storage option designed to meet the food industry’s storage
stow Group has announced the upcoming opening of a new production facility in the United States. This strategic expansion reflects stow
PLASTICS President and CEO Matt Seaholm issued the following statement regarding California Governor Gavin Newsom’s directive to CalRecycle to restart
Reusable delivery solution will reduce environmental impact Nelson-Jameson, a food processing distribution industry, has announced that it will utilize new
With her recent retirement in February 2025, SUN Automation Group® honors and extends its heartfelt gratitude to Pamila Lin, General
Permanent lubrication system reduces maintenance costs A large beverage producer in Mexico invested in an automated system for packing and