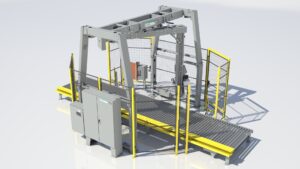
Newly redesigned MA Series provides high throughput Stretch Wrapping capabilities to EOL applications
Orion Packaging Systems is displaying its vast array of stretch and pallet wrapping solutions, including a redesigned MA Series fully
Orion Packaging Systems is displaying its vast array of stretch and pallet wrapping solutions, including a redesigned MA Series fully
Brandon Hall has been the new Director Consumer at Optima subsidiary Optima Machinery Corporation in Green Bay, WI since mid-June.
Columbia/Okura LLC announces that after more than 17 years leading the company, Brian Hutton, President, has decided to retire effective
SUN Automation Group (SUN), a global provider of innovative solutions to the global corrugated industry, has announced that Bryan Fitch
Nick Szczechowski has been appointed as Regional Sales Manager covering the Midwest for Brenton. In his role, Szczechowski will be
The Plastics Industry Association (PLASTICS) has released an analysis on plastics materials for recycling, authored by PLASTICS Chief Economist Dr.
PAC Machinery Bags and Materials announces a new polyethylene bag formulation made from 100% recycled resin. Designed for automatic bagging
The Plastics Industry Association (PLASTICS) released the Committee on Equipment Statistics (CES) report for the first quarter of 2023, authored
Millwood, Inc., a provider of industrial packaging solutions and services, added a 38th location just outside of Huntsville, AL. The
The Plastics Industry Association (PLASTICS) announced today that exhibit space at NPE2024: The Plastics Show, the global platform for innovation in plastics, has
The Plastics Industry Association (PLASTICS) has released the following statement on Oregon’s new single-use plastics law, which bans restaurants and
ProMach, a worldwide provider of processing and packaging machinery solutions, today announced that funds managed by BDT Capital Partners, LLC
The Plastics Industry Association (PLASTICS) has announced the winners of its 2023 Re|focus Sustainability Innovation Awards that recognize outstanding innovations
Barcoding, Inc., a provider of supply chain efficiency, accuracy, and connectivity, has announced its acquisition of Procensis, Inc., a mobility
Signode will present a wide array of transit packaging advancements at Interpack 2023 in Düsseldorf, Germany from May 4-10. Located
For this episode of The New Warehouse, Nick D’Alessio, Senior Business Development Manager at Brother Mobile Solutions, joins Kevin live
Option on TAB Wrapper Tornado Meets Increasing Demand for Entry-Level Automation Packaging machinery manufacturer TAB Industries, LLC, Reading, Pa., has
Phillip Akhzar, Founder of Arka, joins The New Warehouse to discuss customizable sustainable packaging. Arka is an e-commerce platform and
ShipX is an innovative platform that brings together a variety of assets across the United States to provide fast and
Lansmont Corporation, part of the Physical Properties Testers (PPT) Group, is extending its investment in packaging durability testing and research