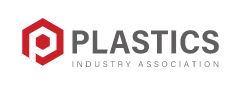
NPE2024: The Plastics Show, over 1 Million Sq. Ft. of exhibit space sold at space draw exhibition
For the first time in six years, NPE heads to Orlando May 6-10, 2024 The Plastics Industry Association (PLASTICS) just announced
For the first time in six years, NPE heads to Orlando May 6-10, 2024 The Plastics Industry Association (PLASTICS) just announced
TAB Wrapper Tornado allows Penn sheet metal to wrap long pallet loads fast Metal fabrication company Penn Sheet Metal, Allentown,
If you have read the latest PLASTICS Size and Impact report, chances are you’ve learned that 89% of plastic products ended up
Daubert Cromwell, a global manufacturer of corrosion inhibitors and protective packaging for industry, announces Polly Huang as Director – Asia
The Plastics Industry Association (PLASTICS) has announced the 2023 Recycling Committee Executive Board. The Recycling Committee is a tactical committee that represents PLASTICS’
PAC Machinery (PAC) is bringing top automatic bagging machines and the NEW options in sustainable packaging it makes for these baggers
The advanced monthly retail sales estimates for December recently released by the U.S. Census Bureau showed another month of a
R.A Jones trials sustainable films on its Pouch King equipment, helping brand manufacturers transition to environmentally friendly packaging and meet
A Packaging Group (APG) is answering the call for more sustainable and environmentally-friendly packaging solutions. As consumers and businesses alike
Rice Lake presents the iDimension Plus XL static dimensioning system, the standard for weighing and measurement solutions for efficiency in
The Reusable Packaging Association (RPA) is beginning 2023 with new executive committee members and additions to its board of directors. After serving
Daubert Cromwell, a global manufacturer of corrosion-preventive packaging for industry, has announced several changes to top-level management positions. Shawn Genz
Customers can expect a smooth, seamless transition to Neece; company founder and previous General Manager Fernando Serpa remains with the
Packaging machinery manufacturer TAB Industries, LLC has introduced a dual dispensing system on its TAB Wrapper Tornado orbital wrappers that
Loftware is a software company that has been around for 35 years and specializes in label operations. Josh Roffman, SVP
The Plastics Industry Association (PLASTICS) has announced that Anthony DiGrado has been named Manager of Digital Affairs, effective immediately. In this
Baldwin Technology Co. Inc. has appointed Adina Starke, a seasoned print and packaging professional with wide-ranging expertise, as Regional Sales
SupplyOne’s Packaging Management Program provides a roadmap to enhanced efficiency, sustainability, and cash flow SupplyOne, Inc., the largest independent supplier
● Kallik is the first label and artwork management solution provider to offer a fully mobile LAM solution with ground-breaking
SATO, a global pioneer in auto-ID and labeling solutions, marks the 60th consecutive year of sale of its longest-running product—the