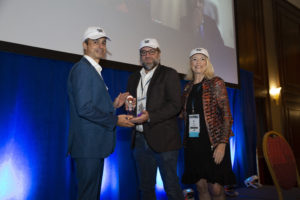
Secro wins approval from the International Group of P&I Clubs
The transformational electronic platform provides speed and security The International Group of P&I Clubs (the Group) added Secro as an
The transformational electronic platform provides speed and security The International Group of P&I Clubs (the Group) added Secro as an
Orbital wrapping machines in the TAB Wrapper Tornado line from TAB Industries, LLC, Reading, Pa., enable packaging and material handling
The deal expands ProMach’s international footprint and global retort capacity to readily serve global brands requiring the sterilization and pasteurization
The shipments of primary plastics machinery (injection molding and extrusion) in North America slowed in the third quarter according to
Integreon Global, a family of companies that ensures product integrity and protection through innovative materials, testing services, packaging, monitoring solutions,
OPTIMA pharma is continuing to strengthen its market position in the USA As of September 26, 2022, John Groth took
TAWI, the inventor of the vacuum lift (also known as a vacuum tube lifter) has launched a new, portable vacuum
Orbital wrapper manufacturer TAB Industries, LLC, Reading, Pa., has unveiled anti-vibration levelers on its TAB Wrapper Tornado line of orbital
Aquapak Polymers, a provider of polymer technology that offers excellent functionality, recyclability, and environmental credentials, has partnered with Industrial Physics,
Miracom Computer Corp., a supplier of post-press production controls and software to the newspaper industry, has expanded its solutions portfolio
Upgrades will substantially reduce lead times and improve plant safety AGE Industries, Ltd, a supplier of custom paper tubes, innovative
Members of the Plastics Industry Association (PLASTICS), working in conjunction with RiverLink, an Asheville-based conservation organization, participated in a clean-up event at River
The award recognizes 10 professionals who demonstrate leadership in packaging Alison Zitzke, senior product manager for ORBIS® Corporation, has been
Welcome to The New Warehouse podcast live from MODEX 2022! In today’s episode, Kevin talks with Sparck Technologies, a company
New development combines pioneering KHS technologies Recyclable PET bottles for CSDs made of 100% recyclate Maximum product protection and elimination
The campaign aims to push back against Amazon’s treatment of third-party sellers and create a level playing field The National
The Plastics Industry Association (PLASTICS) filed comments today with the General Services Administration (GSA), in response to advance notice of
With summer nearing a close, the Reusable Packaging Association (RPA), the world’s premier trade organization for reusable packaging solutions that advance the
Create shrink bundled packages with a single roll platform with printed or clear film; SRX uses a bottom overlap seal
The Corrugating Machinery Division of Mitsubishi Heavy Industries America (MHIA), a supplier of corrugating and box-making machinery, is pleased to