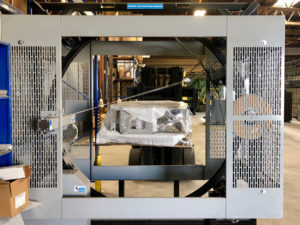
Inflation-adjusted economic justification tool projects labor savings from packaging automation
Orbital wrapping machine manufacturer TAB Industries, LLC, Reading, Pa., has updated its online Economic Justification Tool to reflect surging inflation
Orbital wrapping machine manufacturer TAB Industries, LLC, Reading, Pa., has updated its online Economic Justification Tool to reflect surging inflation
The cannabis industry is growing at an unprecedented rate, and with that growth comes the need for innovative technology solutions.
Serpa, a secondary packaging solutions manufacturer, will exhibit its newly redesigned P150 Intermittent Beverage Cartoner at booth N-5548 at PACK
PAC Machinery, providers of packaging equipment, announces the company’s largest exhibit ever at PACK EXPO International (Oct. 23-26; McCormick Place, Chicago),
Fairbanks Scales Inc., the oldest scale company in the U.S. and the world’s leader in weighing equipment, announces it will
Orion Packaging Systems, a ProMach brand, is displaying its vast array of stretch and pallet wrapping solutions, including its S-Carriage
GEODIS, a world provider in transport and logistics, today announced that it has signed an agreement to acquire the American
Available with Automatic or Manual dispensers for various shipping speeds, the company’s HexaFil™ combines product protection and sustainability HexcelPack, a
The Plastics Industry Association (PLASTICS) has launched a new campaign in an effort to raise awareness regarding the potential environmental
Partnership with the Ozaukee Youth Apprenticeship Program helps showcase careers in packaging to high school senior Sam Kurten Almost everyone
Custom corrugated boxes and fiber tubes protect products and the environment and build brand image The subject of packaging and
Introducing the newly revised One Voice Factory Acceptance Tests – Protocols for Capital Equipment in the CPG Industry work product,
A new report from ORBIS Corporation’s parent company highlights social and environmental actions Menasha Corporation, ORBIS Corporation’s parent company, has
Innovative Packaging Technology is recognized for its superior protection; Keeps critical components safe during shipping and storage RP System from
The TAB Wrapper Tornado from orbital wrapper manufacturer TAB Industries, LLC, Reading, Pa., allows metal parts and products with sharp
Create shrink bundled packages with a single roll platform with printed or clear film; SRX uses a bottom overlap seal
For years, major corporations, service providers, and government agencies have surrendered to the temptation to cloak their cost-saving efforts in
End-to-End Packaging Solutions for mitigating labor, efficiency, and waste-reduction challenges SupplyOne, Inc., the largest independent supplier of custom corrugated and
The Plastics Industry Association (PLASTICS) has announced that Dr. Perc Pineda has returned to fulfill the role of Chief Economist,
The brand-new Emerging Brands Summit, produced by PMMI Media Group, will launch at PACK EXPO International 2022 (Oct. 23-26; McCormick Place, Chicago).