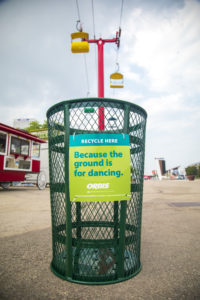
Orbis and Milwaukee Festival Inc. continue partnership to increase sustainability efforts at Summerfest
ORBIS® Corporation, an international reusable supply chain packaging provider, is continuing as the Official Sustainability Partner of Milwaukee World Festival,