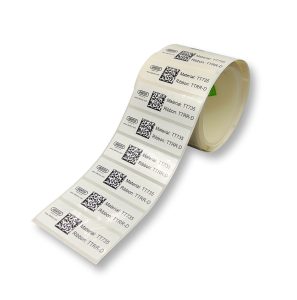
IDENTCO is chosen by Prominent Kayak and Watercraft Provider for label durability
The company’s rugged TT735 Thermal Transfer Labels thrive during thorough comparison tests spanning an exceptionally rare 7,000 hours. IDENTCO has
The company’s rugged TT735 Thermal Transfer Labels thrive during thorough comparison tests spanning an exceptionally rare 7,000 hours. IDENTCO has
ProMach, a worldwide provider of processing and packaging machinery and related solutions, announced today that it has acquired HMC Products,
Add Rennco in booth S-3660 to your PACK EXPO 2024 itinerary to see how its vertical bagging solutions can add
CKF Systems was delighted to have been chosen by Primafruit to develop a new bespoke robotic de-palletising and re-palletising system
London Packaging Week’s Innovation Awards honour groundbreaking designs, including Bowmore ARC-52 Mokume, Highland Park’s 54-year-old decanter, Coca-Cola’s label-free Sprite Naked,
Automated TAB Wrapper Tornado smart controls to be shown in two sizes At FABTECH Orlando booth #S-11128, orbital stretch wrapper
For pharma bottles of various shapes & sizes and will introduce a serialization module for flat cartons, and demonstrate a
Brands, converters & packers can support the circular economy with latest adhesive innovation Marking a world-first, UK-headquartered Power Adhesives has
This year’s LabelExpo, September 10-12 in Chicago, is all about sustainability. Visitors will have the opportunity to network with industry
Mitsubishi Heavy Industries America (MHIA) Corrugating Machinery Division, a corrugating and box-making machinery supplier, announced its participation in SuperCorrExpo® 2024.
MAXXDRIVE industrial gear units from NORD DRIVESYSTEMS deliver significant output torques, quiet operation, and long service life for heavy-duty industrial
Jude Allan, Chair of IOM3 Packaging Society and interim Managing Director of OPRL, discusses how the evolving landscape of material
CL&D’s new South Carolina facility, its second in the state, positions the company to increase its flexographic production capabilities to
NORD offers a wide selection of gear units, electric motors, and drive electronics that work in unison to deliver efficient,
The company has completed three acquisitions in 2024 alone, bringing its overall count to forty-one acquisitions over its 25 years
Latin American Salmon Supplier Introduces Products with Biodegradable Packing Bioelements Group has announced that Bioelements will be supplying biobased, biodegradable,
SUN Automation Group (SUN) will attend SuperCorrExpo at Booth 1731 at the Orange County Convention Center in Orlando, Florida from
The Plastics Industry Association (PLASTICS) has released the inaugural Plastics Demand Estimate Report. The report estimates the plastic demand estimate
PAC Machinery has announced the new Rollbag® R3200 Fulfillment Paper Automatic Bagger. This innovative model, also available in an XL
When it comes to trade shows and events, a key focus for potential attendees is the return on investment (ROI).