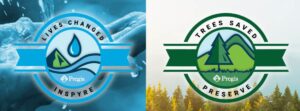
SupplyOne receives prestigious Pregis Inspyre and Preserve awards
SupplyOne, Inc., the largest independent supplier of corrugated and other value-added packaging products, equipment, and services in North America, just
SupplyOne, Inc., the largest independent supplier of corrugated and other value-added packaging products, equipment, and services in North America, just
SupplyOne, Inc., the largest independent supplier of custom corrugated and other value-added packaging products, equipment, and services in North America,
NPE2024: The Plastics Show announced its final registration and paid exhibit space results, totaling 51,396 registrants and 1,106,767 square feet, respectively. Held from May 6-10
Welcome to The New Warehouse Podcast! Today, we have Ken Rohleder, the president of IQpack, joining us. IQpack specializes in
2024 event raises over $370,000 to support practitioners and patients in the Pediatric Simulation and Resuscitation Program ORBIS® Corporation, a global
The Plastics Industry Association (PLASTICS) has unveiled a new video as part of the Recycling is Real advocacy campaign, dedicated to promoting and
Chris Shay is their point of contact for Matrix vertical form fill and seal packaging customers in the South-Central region
SupplyOne, Inc., just announced that it has expanded its footprint to the West Coast with the acquisition of Columbia Corrugated
ORBIS ® Corporation has earned recognition as a Partner-level supplier for 2023 in the John Deere Achieving Excellence Program. The
SupplyOne, Inc., the largest independent supplier of corrugated and value-added packaging products, equipment, and services in North America, announced that
Seagull Scientific, LLC, (“Seagull”) maker of BarTender®, the global leader in software to print, mark, and code labels, RFID tags,
Partnership unites community members and resources to provide supplementary weekend food to students in the Kettle Moraine School District ORBIS®
In his new role, Watterworth will be working directly with Orion channel partners to build relationships, train staff and provide
Menasha and Neenah Mayors declare May 21st as ‘Menasha Corporation Day’ in honor of ongoing community support In celebration of
PAC Machinery (“PAC”) has announced the retirement of its President, Serge Berguig after 40+ years with the company. Serge is
Industry-Wide Competition Celebrates Greatest Achievements and Innovations at SuperCorrExpo® TAPPI and AICC, co-producers of SuperCorrExpo®, have announced that entry for
The Food Product Innovation and Commercialization Center (FoodPIC) supports the development of food products from concept to shelf Tetra Pak and
NPE2024 Captivates and Inspires Global Leaders and Rising Stars to Shape the Future of the Plastics Industry NPE2024: The Plastics
Company to showcase label feeders and product solutions to simplify automation. IDENTCO will highlight its automation capabilities and PCB labeling
The Marsh Bellofram Group of Companies has announced a reorganization of its sales territories and a new, more holistic approach