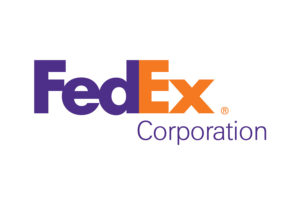
FedEx announces 2024 shipping rates, fees and surcharge increases
FedEx Express, FedEx Ground, and FedEx Freight, subsidiaries of FedEx Corp. will adjust shipping rates on January 1, 2024. •
FedEx Express, FedEx Ground, and FedEx Freight, subsidiaries of FedEx Corp. will adjust shipping rates on January 1, 2024. •
ORBIS® Corporation, an international provider in reusable packaging,will highlight the latest in reusable packaging solutions for a sustainable supply chain
CASSEL Inspection, a custom provider of inspection solutions for food production, plastics, pharmaceuticals and more, will be on the exhibit
Award ceremony to take place September 12 at 3 pm PST at PACK EXPO Las Vegas in the RPA Pavilion
Entire system performance increased by ten percent Shuttles unite performance with reliability, a rugged design, and energy efficiency Maximum availability:
Looking for high speed case forming and labeling all in one efficient solution? Then be sure to add Wexxar Bel to your
Cabka, a provider of reusable transport packaging made from recycled plastic, has announced its participation in the upcoming Pack Expo
Patrick Davis has been appointed Regional Sales Manager for Brenton, a role in which he will be working with east
Orbital wrapper manufacturer TAB Industries, LLC, Reading, Pa., has named Kevin Slick sales associate. Bringing nearly five years of business-to-business
Matrix will be highlighting its vast portfolio of vertical form fill seal and pre-made pouch solutions and demonstrating how they
The Plastics Industry Association (PLASTICS) has submitted comments in response to the Environmental Protection Agency’s (EPA) request for public input
In this episode of the New Warehouse Podcast, Kevin Mireles, the former Chief Sustainability Officer at Delivered, sheds light on
The ability to collaborate between brands to develop and execute integrated solutions is what defines the power of ProMach. A
HexcelPack, a developer of eco-friendly, paper-based protective packaging solutions to replace bubble and air pillow packaging and other plastic, paper
In today’s episode of the New Warehouse podcast, we have a special guest, Cory Connors, the Director of Sustainable Packaging
A 30% footprint reduction without sacrificing throughput makes the Micro VCCL is a must-see Las Vegas attraction When it comes to
Orbital wrapper manufacturer TAB Industries, LLC, Reading, Pa has earned another patent for an advance in stretch wrapping. Following a
FoldSerter Color™ now gives e-commerce fulfillment companies flexibility to add full color documentation to each order, with an unlimited amount
Ideal for applying self-laminating & flag labels to wires, cables & harnesses, company’s durable VortexID can handle up to 20
Customized packaging solutions help customers achieve sustainability goals without sacrificing performance or profitability SupplyOne, Inc., a supplier of custom corrugated