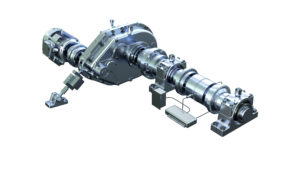
Regal enhances its Industrial Powertrain capabilities
End-to-end solutions optimize efficiency within bulk and unit material handling, metals, pulp and paper, mining, and other critical industrial applications
End-to-end solutions optimize efficiency within bulk and unit material handling, metals, pulp and paper, mining, and other critical industrial applications
New Eaton PowerXL™ DM1 micro variable frequency drives help customers increase space savings in multiple environments Offers proven performance efficiency
STXI Motion, a global motion control, and servo solution company, introduces the PRHD2 high-performance permanent magnet synchronous servo motors from
Continuing to expand on a product category that it has been manufacturing for over 38 years, LEDtronics® introduces its latest
On this episode, I was joined by Dave Baiocchi of Resonant Dealer Services. We focused the discussion on something I
TVH in the Americas (TVH), a global provider of quality replacement parts and accessories for the material handling and industrial
The award-winning products designed to fill the gap between induction and servo motors Bison Gear & Engineering Corp., a provider in the
Thomson Industries, Inc., a manufacturer of linear motion control solutions, celebrates its 75th anniversary this year. Activities and celebrations throughout the year
TVH in the Americas (TVH), a global provider of quality replacement parts and accessories for the material handling and industrial
The North American subsidiary of the KION Group, KION North America, has completely revamped its online portal for its dealer
All Integrated Solutions (AIS), a division of MSC Industrial Supply Co., announced that it has received an Outstanding Quality Award
TVH in the Americas (TVH), a leading provider of quality replacement parts and accessories for the material handling and industrial
To help prevent accidents at aisle ends and other high-risk intersections, Rite-Hite has introduced the Safe-T-Vu™ Warning System, a rack-mounted
Innovative load binders for safer and more efficient load securement The Crosby Group, a global provider in lifting, rigging, and
Comprised of the drive, motor, and gearbox, this new distributed drive system is available as a complete solution for motor-mounted
Last month I started a series on the customer experience (the CX). To refresh your memory (or if you missed
The new lightweight two-gas monitor offers more accurate alarms and minimizes maintenance with a two-year runtime Industrial Scientific, a global
Motion Industries, Inc., a distributor of maintenance, repair, and operation replacement parts, and a premier provider of industrial technology solutions,
On this episode, I was joined by the VP and Head of Product at KINETIC, Chris Kuruc. KINETIC is a
A new multifunction handle is designed for right-hand operation APEM, Inc. announces the launch of its new RT handle, an