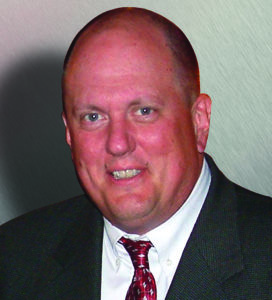
Under-promise and over-deliver
The title of my column is the mantra of many aftermarket professionals in our industry. Nobody ever wants to get
The title of my column is the mantra of many aftermarket professionals in our industry. Nobody ever wants to get
S3TL ferrules improve wire connections to screw and push-in terminals IDEC Corporation has released a complete product line of S3TL
Siemens just announced the immediate availability of a new enclosed drive system, the SINAMICS G120XE, designed specifically for the demands
The Model 93 LED headlight offers 5-in-1 functionality for a wide range of applications, including original equipment manufacturer (OEM) designs
Ergodyne announced the launch of an all-new Aerial Bucket Series designed specifically for safer, easier work in bucket trucks and
Myers Industries, Inc. has announced that it has acquired the assets of Mohawk Rubber Sales of New England Inc., which
Motion Industries, Inc., a distributor of maintenance, repair, and operation replacement parts, and a premier provider of industrial technology solutions,
As 2022 grinds toward the midway point conditions have not really been improving. The climate continues to be driven by
Myers Industries, Inc. has announced the upcoming departure of Sonal Robinson, Executive Vice President and Chief Financial Officer. Ms. Robinson
She Builds Grants initiative supports nonprofits that empower and educate women pursuing careers in the trades KEEN Utility, the work
Fenner™ Precision Polymers, a Michelin Group Company and world provider in reinforced polymer technology announced the move of its corporate
As the bags become thinner and flimsier, the more carefully they need to be treated. With the new BGX suction
The Appleton Contender 4/4X Series factory sealed design significantly reduces maintenance and replacement costs lowering the total cost of ownership
Building on the success of its predecessor, KEEN Utility’s Kansas City+ is a standout introduction for Spring ‘22. Heavy on
Kollmorgen, a global provider in motion control systems, has announced the new TBM2G series of frameless servo motors, introducing features
Signode, the global manufacturer of a broad spectrum of automated packaging equipment, tools, and consumables, has launched its new BPT
Force Control Industries designs, manufactures, inventories, and services industrial clutches and brakes from their Fairfield, Ohio factory. This family-owned company
If precise, quiet, and dynamic linear movements are required, linear guide rail systems are indispensable. For special applications, JW Winco
With the introduction of the Cincinnati Wellington, KEEN Utility incorporates modern, lightweight materials into a time-tested pull-on style for heavy-duty
Fairbanks Scales Inc., the oldest scale company in the U.S. and provider of weighing equipment, has announced they will be