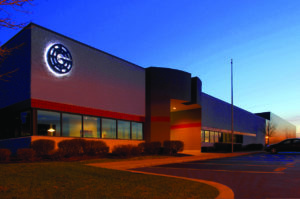
Genesee Global celebrates 20 years of ERP loyalty with Global Shop Solutions
Customer loyalty can be hard to find in today’s highly competitive manufacturing industry – unless you happen to be Global
Customer loyalty can be hard to find in today’s highly competitive manufacturing industry – unless you happen to be Global
Dedication to its customers, world-class customer service, premium product offerings, and willingness to provide experienced advice on the proper way
TVH has officially opened its new main office in Waregem, Belgium. Dubbed ‘The Hub’, the new facility was opened by
As an internationally recognized system integrator in the field of intralogistics, viastore completes TICO’s range of products and services, enabling
Targeted “quality enhancements” are designed to improve service life, lower maintenance requirements, and optimize overall product performance DESTACO has completed quality
B&B Attachments has appointed Marie Ridley as Parts Manager. Marie began her professional career in Forklift Engineering and Mechanical Maintenance.
TVH Americas, a global provider of quality replacement parts and accessories for the material handling and industrial equipment industries, was
2022 is shaping up to be a year like none other in the recent past, as supply chain disruptions force
DESTACO is excited to announce that the following 14 models in its popular Manual Hand Clamp product family are now
TVH Americas, a global provider of quality replacement parts and accessories for the material handling and industrial equipment industries, has
Motion Industries, Inc., a distributor of maintenance, repair, and operation replacement parts, and a premier provider of industrial technology solutions
The event will highlight global electrification efforts and showcase keynote speakers in the industrial electrification space ZAPI GROUP, a global provider
Continuing to expand its offerings of LED indicators for industrial control panels, LEDtronics introduces new additions to its family of
In December of 1980, I left college and got my first full-time job. We had just elected Ronald Reagan in
JW Winco’s new handbook will support designers and engineers with the largest selection of standard parts. Our handbook has the
Creform Corporation, a manufacturer of unique products for material handling has designed and produced a kitting cart that is used
A full line of shaft collars, rigid shaft couplings, and mounts that are corrosion-resistant for applications requiring frequent wash-down has
Rice Lake Weighing Systems’ powerful line of dimensioning solutions now includes the iDimension® LTL XL, designed specifically for freight with
Renewable Lubricants new Bio-Blast™ Penetrant is a high-performance, fast-acting, biodegradable penetrant that eradicates rust and dirt to quickly free corroded
Mactac®, a LINTEC Company, announces it has completed the acquisition of Spinnaker Coating, LLC, representing $130 million of specialty revenue