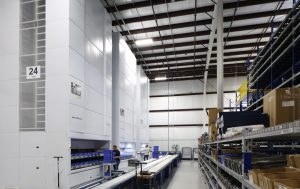
Carolina Handling named a Modula top performer
Carolina Handling has been named a top performer by Modula Inc., a manufacturer of vertical lift modules and automated storage
Carolina Handling has been named a top performer by Modula Inc., a manufacturer of vertical lift modules and automated storage
Nucor Corporation has announced the promotion of Thomas J. Batterbee to the position of Executive Vice President of Human Resources
Epax Systems, a supplier and installer of waste compaction systems, including stationary compactors, rolling compactors, vertical balers, and horizontal balers,
Comprised of the drive, motor and gear box, this new distributed drive system is available as a complete solution for
Although winter weather evokes images of warm fires, icy wonderlands, and snowball fights, it can also be highly destructive to
Among other benefits, the company’s new NITRODOSE® G3 SERVODOSER® can adjust liquid nitrogen flow rate without nozzle changeover Vacuum Barrier
Market challenges post-Covid – including rising living costs, project delays and bottlenecks – will need to be overcome in order
SalesLeads has released the July 2024 results for the new planned capital project spending report for the Industrial Manufacturing industry.
NORD offers a wide selection of gear units, electric motors, and drive electronics that work in unison to deliver efficient,
Industrial SalesLeads announced the June 2024 results for the new planned capital project spending report for the Industrial Manufacturing industry.
Robroy Industries® Enclosures Division has appointed Geoff Twietmeyer as General Manager. Mr. Twietmeyer holds an MS degree in Engineering Management
Hikvision, a manufacturer and supplier of security products and solutions that deliver the ideal combination of high performance and extreme
A U.S. Department of Labor workplace safety investigation has found a Woodbury plastic and resin manufacturer could have prevented a
Nucor Corporation announced it has agreed to acquire Rytec Corporation, a manufacturer and seller of high-speed, high-performance commercial doors. The all-cash
Pettibone Traverse/Lift, LLC is celebrating the 75th anniversary of the Cary-Lift, which became the world’s first forward-reaching, rough-terrain material handler
Avid Solutions, selected as the preferred delivery partner for hydrogen solutions by Rockwell Automation, has recorded exceptional revenue growth and
Cyclonaire Corporation has announced the appointment of John Elliot as Business Development Manager – Cementitious Materials. Elliot assumes this critical
Company Expands Global Marketing Organization with Strategic Appointments Haver & Boecker Niagara, a provider of screening, pelletizing, and mineral processing plants
Booth to feature company’s latest machines to maximize profitability and productivity for concrete professionals From battery-powered equipment to portable power
DIEFFENBACHER collected donations during its 150th-anniversary celebrations DIEFFENBACHER welcomed numerous business partners to a festive stakeholder event in its specially