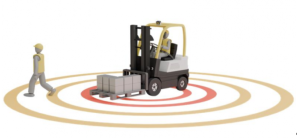
ELOKON launched a dual-layered safety system for maximum forklift and pedestrian protection – ELOshieldAI
New solution combines ultra-wideband (UWB) proximity detection and AI-powered, tagless vision technology to prevent collisions in high-risk industrial environments ELOKON,