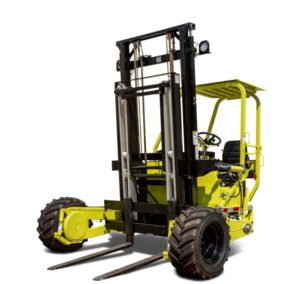
Frontier Forklifts joins Donkey Forklifts as Southeast Texas dealer
Donkey Forklifts®, an American-made forklift manufacturer known for its versatile and reliable equipment, has announced a new partnership with Frontier
Donkey Forklifts®, an American-made forklift manufacturer known for its versatile and reliable equipment, has announced a new partnership with Frontier
In celebration of Carolina Handling’s 58 years in business in 2024, the Charlotte, North Carolina-based intralogistics company has awarded 58
Proceeds benefit Fargo-area community with more than $1.291 million raised since 1984 The 60th annual Bobcat North Dakota Open again
H&E Rentals announced the opening of its Frederick branch, the company’s third location in the state of Maryland. H&E has
H&E Rentals has announced the opening of its Lufkin branch, the company’s 31st location in the Lone Star State and
Program advances Hyster-Yale’s commitment to veterans, enables manufacturer to recruit talent from the world’s most highly trained and motivated workforce.
H&E Rentals has announced the opening of its Amarillo branch, the company’s 30th location in the state of Texas. H&E
Bobcat Company recently brought material handling into the Bobcat brand, transitioning from Doosan Industrial Vehicle to Bobcat in early 2024.
Today, the Manitowoc Company, Inc. reported a second-quarter net income of $1.6 million, or $0.04 per diluted share. Second-quarter adjusted
Total revenues increased $19.7 million year over year to $488.1 million Construction Equipment and Material Handling revenues of $294.9 million
Raymond West Intralogistics Solutions and Toyota Lift Northwest announced that effective immediately, they have joined forces, marking the formal integration
H&E Rentals has announced the opening of its Springfield branch, the company’s fourth general rental location covering the state of
Yale Lift Truck Technologies announces that it has been recognized by the SupplyTech Breakthrough Awards as the 2024 Material Handling Company of the
H&E Rentals has launched a Mental Health and Hope training module to shed light on the mental health crisis that
Effective August 5, 2024, H&E Rentals (H&E) announces the opening of its Cedar Rapids branch, the company’s first general rental
Yokohama TWS North America awarded for going ‘Above & Beyond’ in customer service for the Americas The top supplier award
Revenue up by 2 percent to € 5.736 billion (H1 2023: € 5.617 billion) Adj. EBIT improves 28 percent to
H&E Equipment Services, Inc. reported financial results for the second quarter that ended June 30, 2024, including further expansion of
For over 86 years, Toyota has built a reputation for reliability, innovation, and leadership in the automotive and industrial sectors.
This special episode comes to you from this year’s WERC Conference. This episode, sponsored by Big Joe Forklifts, dives into